这一系列从设计到加工及批量化的过程均是在宝马集团位于兰德舒特的工厂进行的。由此产生的结构既具有成本竞争力,又具有可持续性。在上期文章基础上,本期文章将继续介绍更多技术细节内容。
04、批量产品的开发
作为批量产品开发的一部分,为了使用经过验证的解决方案来粘合前车顶弓,在前面需要另一个金属薄板(图3b)。除了产品要求(例如碰撞要求)外,批量产品的开发还包括证明系列产品的稳定生产和一致的产品质量。可持续发展的目标也必须实现,特别是通过小的材料消耗和回收材料的使用,保持相对于不断发展的金属薄板外壳结构的重量优势。
基本生产概念在批量生产中得到了确认,包括从碳纤维起始材料到部件的三个工艺步骤。步,连续纤维浸有用于UD插件的PA6基体中,通过拉挤成直杆并切割得到所需的产品长度;在第二步中,杆再次熔化,并通过夹具拾取,由于端齿轮已经通过单个夹具的移动进行调整,因此可以将其准确地放置在成型工具中。
后的轮廓是通过关闭成型工具来实现的。在接下来的循环中,尺寸稳定但仍然温热的杆(图3a)与钣金嵌件一起插入同一生产单元(图5)的注塑模具中,并用注塑化合物进行二次成型。回收的注塑材料也分三步生产:
粉碎预成型辅料并将其分解成纤维;
与PA6基体复合;
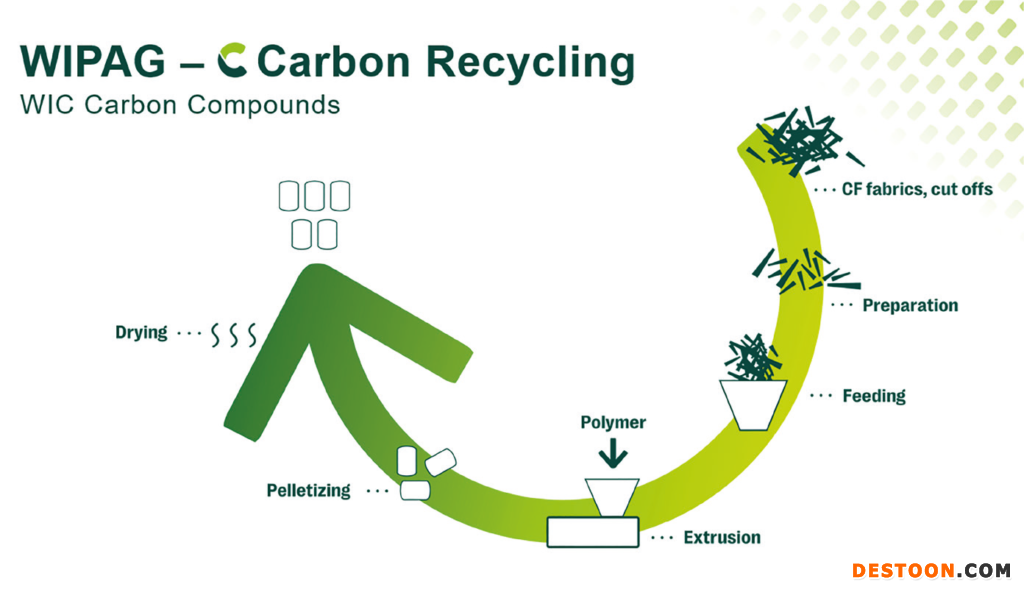
将熔化的颗粒注射到封闭的模具中(图4)。
成型棒和熔体成型注塑化合物中储存的热量足以实现粘结材料连接,从而通过热均衡过程实现良好的表面粘合。
从CFRP直杆、金属嵌件和碳纤维增强注塑颗粒开始,所有进一步的加工步骤都是在宝马集团位于兰德舒特的塑料生产单元的注塑机周围的生产单元(图5)中进行的。BMW iX的两个骨架部件,前车顶弓架(图3c)和后窗框是作为前车顶弓和后车顶前车顶弓制造的。数字化潜力被直接利用,因此在质量保证的框架内,从注塑成型和杆生产到车辆的追溯是可能的。
事实证明,插入预制纤维增强嵌件是一种优势,因为这会导致连续纤维的稳定位置,从而显著影响部件的机械性能。此外,在概念阶段镶件已经表明,含有注塑材料的碳纤维的收缩(已经很小)几乎不会导致组件变形,从而实现了非常稳定的过程。
第三个优点是,在注射成型过程中可以实现少于85秒的周期时间,尽管插入了一些零件,CFRP插入部分的结构壁厚超过10毫米。由于车身车间集成,前车顶撑弓零件的数量从四个减少到一个,而无需新工艺。这同样适用于后窗框架,它也使用骨架结构。油漆车间没有变化,因为PA6作为基体,KTL炉温度(约180°C)和熔化温度(220°C)之间的差值足够了。即使在这些温度下,纤维结构也为骨架部件提供了足够的强度,以承受在加热和冷却过程中产生的热量差异所产生的力。
05、部件设计和保护
早在概念开发阶段,软件工具被迭代地用于模拟组件设计和测试结果(弯曲和冲击测试),设计模拟工具以过程仿真为补充。在次测试后,观察到部件行为预测与测试结果吻合良好,并在开发过程中进一步细化。同时,还进一步实施了细节,以便于部件设计,同时消除错误来源。使用众所周知的系列工艺,可以在载荷或失效预测中进行明确的几何划分,以及CFRP插件和注塑框架之间的良好内聚连接,从而可以实现良好的部件尺寸标注。
到目前为止,部件尺寸的确定一直是纯迭代的,特别是通过手动调整短纤维增强注塑部件,然而,这可能会很快失去设计中的轻质结构优势。对于这种具有各向异性材料特性的混合涂层系统,尤其是非线性碰撞计算,尚不可能进行(半)自动拓扑优化。虽然使用了由碳纤维和热塑性PA6基体组成的双材料系统,但在结构上有必要考虑由插入杆和注塑框架组成的混合系统,该混合系统在纤维长度、含量和方向上有所不同。对于纤维重量相对较低(15%)的注塑组件,可以设想使用准各向同性材料。
06、可持续性、轻型结构和回收利用
宝马iX的前车顶弓是一个CFRP轻质组件,与金属板框架相比,重量减轻了45%。由于低输入重量、能量优化的碳纤维生产方法以及组件生产中开发的优势,与通常由高性能WU钢制成的多部件板框架相比,CFRTP骨架结构的二氧化碳排放量已经更好。
先,这种良好的结果是由于骨架施工方法的优势:没有生产浪费,这对于CFRP结构件来说是一种新事物,并且在注塑成型部件中可二次使用碳纤维(图4)。
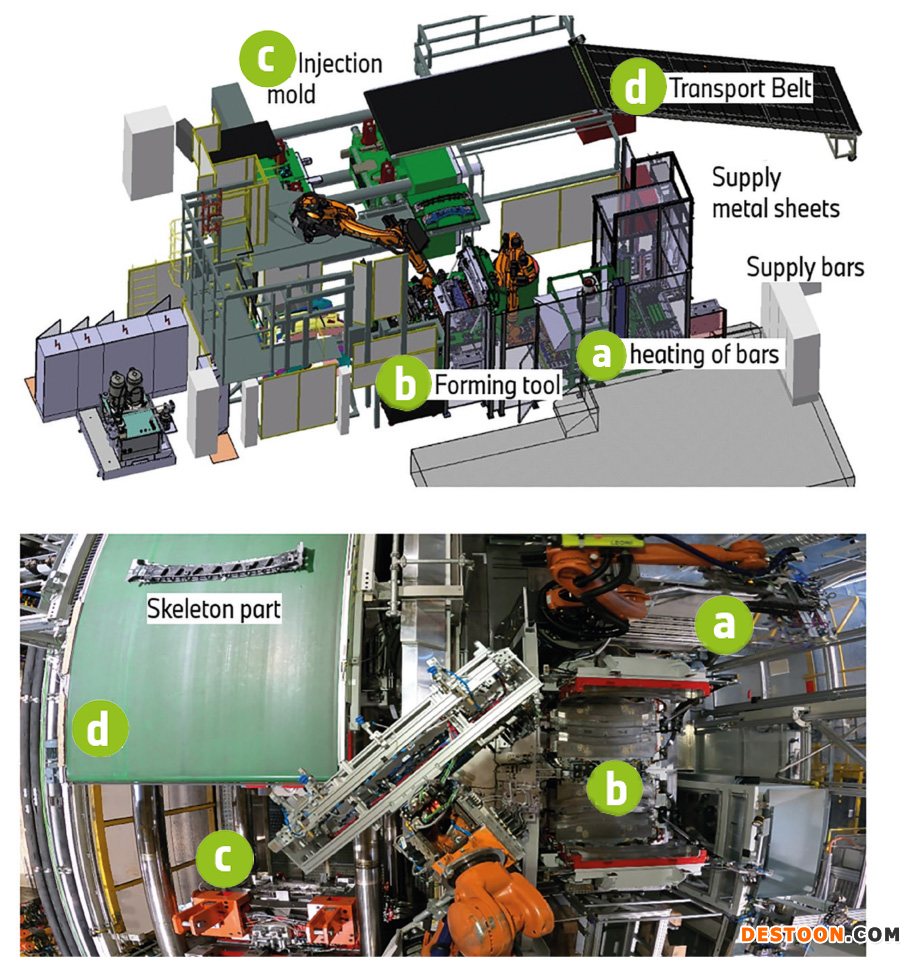
综上所述,新款BMW iX的前车顶弓和后窗是新骨架设计中的标准组件,它展示了如何以高施工标准在批量生产中实施此设计(图6)。因此,在十年内,与2010年基准年的手工生产为主相比,大规模汽车生产用CFRP部件的成本降低了80%以上。