关键词
复合材料 ; 编织增强 ; 悬垂 ; 灌注 ; 数值模拟
1. 引言
商用飞机工业正不断发展更强大、更轻便的结构。复合材料,尤其是碳纤维增强塑料,已经普遍成为传统铝合金的替代品。碳纤维增强塑料具有出色的强度和刚度、良好的结构阻尼和能量吸收特性,以及更佳的疲劳强度和耐腐蚀性[1]。此外,它们使高度集成的复合结构设计具有更大的灵活性,大大减少零件数量和对机械紧固性的需求。例如,1985年,空中客车公司在A300和A310机型上引入了复合垂直尾翼,在2076个原有金属部件的基础上减少了95%的零件数量[2,3],减少至95个组件,并使飞机减重400 kg,同时也节省了生产和组装成本[3]。
初,纤维增强复合材料仅用于商用飞机的三级结构,并且仅占整体结构重量的一小部分。然而,到20世纪90年代中期,复合材料广泛应用于几乎所有二级结构,并且占总结构组成的15%~20%。如今,新一代的宽体飞机,如波音787和空客A350,已经在大部分机身上使用纤维增强复合材料,其占飞机结构重量的50%以上[4]。窄体飞机方面也取得了类似的进展,庞巴迪C系列和联合航空制造公司的Irkut MC-21实现了复合材料组成超过40%[5]。图1显示了自20世纪70年代以来复合材料在商用飞机中使用量的增加情况。
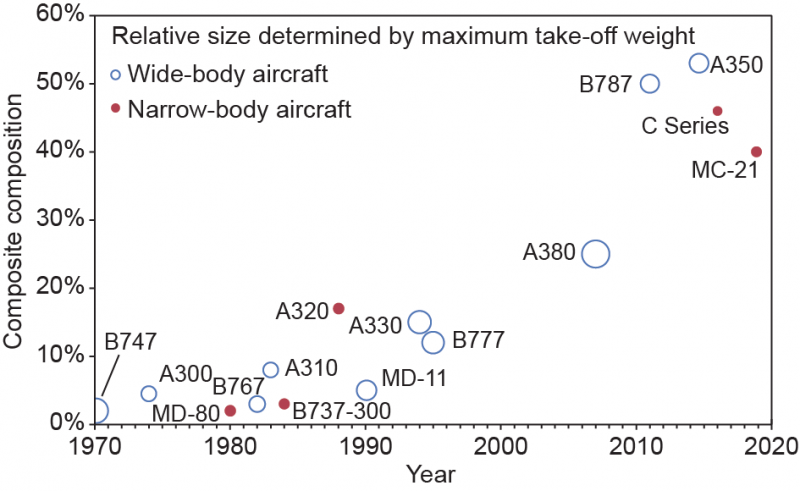
1.1. 材料及加工
航空航天复合材料通常由单向(UD)碳纤维堆叠片材制成,这种片材经树脂预浸渍(称作“预浸料”),并且可用于生产具有惊人刚度和韧性的层合板。但是,为了制造更具韧性和弹性的结构,可以使用编织增强材料。编织增强材料由编织碳纤维丝束制成,可以以干燥或预浸渍的形式使用。和UD预浸料相比,编织增强材料以降低刚度(10%~30%)和轴向强度(15%~35%)为代价,获得更优的加工性能、抗冲击性、损伤容限和切口灵敏度[6]。此外,编织增强复合材料具有出色的平面外力学性能、更好的剥离强度以及较少的裂纹增长。较之复杂模具,干燥的织物也表现出更好的成型能力,尤其是对于双曲面结构,UD预浸料和胶带则经常出现裂缝[6]。编织增强材料的结构对复合材料性能的影响也很大,这意味着可以根据具体要求而调整材料[7]。因此,在工业中广泛使用各种各样的机织、针织和非卷曲织物。
预浸料的加工通常依靠热压罐中高热量、高压力条件下的固化周期来生产高质量的终部件。然而,在许多情况下,足够大的、用于生产航空复合材料结构的热压罐可能非常昂贵,尤其较之类似尺寸的烘箱,热压罐的价格高出3~10倍[5]。因此,非热压罐预浸料技术,如柔性模具树脂浸渍工艺(RIFT)[8],在低产量及大、中规模应用中正逐步替代传统预浸料方法。RIFT方法通常在树脂注入模具之前,在真空条件下使用柔性工具在刚性模具上形成干燥的纤维增强材料。填充之后,该部件就在室温或者高温条件下真空固化。因为不需要热压罐,这种方法可以大大降低制造大型复合结构的资金和持续成本。与易腐烂的预浸料相比,将非热压罐预浸料技术与干燥编织增强材料相结合,不仅可以减少材料浪费,还能够显著提高储存期限[1]。
然而,将树脂灌注制造工艺推广于航空航天工业的过程中,可靠性和可重复性问题依然是两大难题。这些方法在很大程度上依赖于操作者的技能和经验,因此会产生大量的时间和材料成本。在大型高度集成的航空复合材料结构的发展过程中,反复试验法的缺点更为明显。模拟树脂灌注制造过程的研究旨在以更经济的方式解决可靠性和可重复性问题。
1.2. 过程模拟
树脂灌注过程对于模型来说十分复杂。每次应用根本上取决于增强材料在形成时的力学行为、树脂在灌注过程中的流变行为,甚至树脂固化过程中的化学行为。
此外,这些行为在编织增强材料中可以在不同的尺度上发生根本的变化。通常在三个层次上对这些材料的行为进行研究:宏观尺度、介观尺度和微观尺度。宏观尺度是指整个织物层或者整个预制件行为。介观尺度是关于编织组织的内部结构以及纱线本身。微观尺度侧重于每根纱线的单根纤维。图2显示了编织增强材料三种不同等级的尺度。
从建模角度来看,宏观尺度假设了整个编织预制件的均匀性,由于其快捷、简便,因而成为常采用的方法[9]。介观模拟通常试图重新创建复杂的纱线几何形状及其在织线组织内的相互作用。因此,介观模拟需要更大的计算量,而且对于模拟大型领域来说效率不高。后,微观模拟通常旨在复制纱线内单根纤维的分布和相互作用。因此,微观模拟具挑战,其一般仅限于解决尺度极小的结构问题。
计算能力的提升和用户友好型软件包的激增促进了不同规模的树脂灌注在各方面的大量研究。一般来说,制造过程分为两个主要研究领域:“悬垂”,即增强材料的物理成型,以及“浸渍”,即树脂通过增强材料的流动成型。研究这两个领域时,通常假定它们为独立的过程。然而,编织品变形和注入行为之间存在着已知联系,这对于具有复杂曲面的结构极其重要[10]。根据这一联系,尝试开发一种“集成设计工具”,用于预测编织增强复合材料结构的成型、浸渍和终性能[11,12]。
本文综述了编织增强复合材料灌注过程建模的发展,涵盖了悬垂模型、材料表征和灌注模型等领域的一系列研究成果。本文还重点论述了上述研究的研究者近在先进多物理场过程模拟应用方面的工作。
2. 悬垂模型
研究人员已经针对多种应用研究了在复杂模具上的织物悬垂的物理响应和模拟。除了工程领域对于复合增强材料的关注,服装和动画行业也对织物悬垂的模拟进行了研究。种用于预测织物悬垂行为的分析模型采用基于几何映射的方案。随后,在20世纪90年代,非工程应用中出现基于粒子的美学方法。然而,如今精确、可靠的计算方法依赖于连续、离散或半离散方法。这些都需要对织物的力学性能有一定的了解,才能真实地模拟变形行为。因此,为了支持预测模型,大量研究工作致力于更好地理解和表征织物的变形机制。
2.1. 力学性能
每种建模方法都建立在不同的假设之上,因此需要不同的材料力学性能来模拟织物行为。例如,在涉及一小部分独立纤维的微观模型中,只需要考虑纤维的弹性性质及其相互作用。在机织纱线的介观模拟中,仅需考虑摩擦力和纱线性能。另外,宏观模型经常忽略纱线和纤维的细节,并将织物视为均匀的材料层。因此,在宏观模拟中需要考虑织物的力学性能;鉴于这一性能,面内剪切被认为是主要的变形机制[13]。增强纤维的高拉伸强度使得拉伸性能对于宏观织物行为而言非常重要。另外,这些织物相对较低的弯曲强度仅用于改善起皱性能的预测[14],或被完全忽略[15]。
由于大多数研究旨在探讨编织增强材料制造复合材料结构的宏观行为,因此织物拉伸、剪切和弯曲性能的表征仍然是重点。尽管缺乏合适的标准,但这些特性通常是通过实验来表征的。然而,为了预测宏观行为,需将详细的介观尺度或微观尺度模型与实验表征的纱线或纤维性质相结合并进行研究[16,17]。对于开发新的编织品或用于表征由相同的纱线或纤维制成的一系列不同的织物,这些预测方法或许更加可取。宏观实验表征通常用于确定特定预先存在的材料的特性。
从力学角度来看,研究证明悬垂行为难以准确复制。编织的经纱和纬纱表现出极大的拉伸强度和刚度,但在剪切和弯曲模式下极易重新取向。因此,任何模拟悬垂都必须准确说明由剪切载荷引起的纱线重新取向[18]。鉴于纱线重新取向的重要性,悬垂研究通常采用剪切角或γ参数来监测局部变形。如图3所示,这是表示织物中经纱和纬纱之间角度变化的程度。在初始未变形状态下,经纱和纬纱垂直,相对剪切角为0°。然而,施加剪切载荷时,织物发生格栅行为,且剪切角随之增加。后,纱线之间的缝隙闭合,开始侧向压缩,导致“锁定”效应和极大的抗剪切力。根据预成型件的结构,这种情况通常发生在30°~60°之间的剪切角。经过该点,进一步的剪切载荷可能会导致面外屈曲行为,该行为也被称为“起皱”。出于模拟目的,通常忽略起皱行为,因为其难以复制。同样,悬垂模型通常忽略交叉处纱线的滑动。
2.1.1. 拉伸表征
织物的拉伸性能是由每根纱线内纤维的刚度引起的,但在悬垂时仅起到次要作用。一个纱线方向的拉伸载荷对另一个纱线方向的拉伸性能能够产生影响,这表明悬垂模型需要双轴表征来支持[16]。然而,在各种加载速率下,构建和操作用于测试经纱和纬纱方向上十字形样品的双轴钻机颇具挑战。因此,通常在双轴行为可以忽略的假设下,没有双轴测试标准,经常采用单轴“抓取”和“条带”[19]测试。
2.1.2. 剪切表征
编织增强材料的剪切行为往往是高度非线性的。在低载荷下克服初始摩擦之后,织物纱线在剪切载荷下的转动相对自由。然而,随着材料终达到“锁定”状态,剪切阻力呈指数型增长。早期的织物剪切行为研究采用Kawabata简单剪切试验,将样品的其中一段固定,另外一段横向剪切[20]。然而,这种方法是为服装行业开发的,并且仅限于剪切变形较小的编织增强材料[21]。鉴于这一限制,如今,画框测试和斜拉伸测试更为普遍,这两者都依赖于轴向测试。
画框测试使用正方形或十字形样品,将其夹在具有枢接结构的菱形框架中[22]。然后使用标准拉伸测试机器拉伸框架的两个对角来剪切织物。该方法具备良好的重复性,并且在整个样品中显示出均匀形变。然而,固定和对准问题都会影响实验结果[23]。或者,可采用简单的固定装置进行斜拉伸测试,以避免固定或对准问题。将长方形样品根据受力方向平分为经纱和纬纱两个方向(织物“偏压”方向)。在标准拉伸试验台上进行试验时,整个样品的剪切形变分布不均匀,只有中心菱形区域受到纯剪切。此外,在较高载荷下,固定的边缘附近可能发生纱线滑移。因此,为了获得准确的实验结果,应使用光学应变测量技术,如数字图像相关法(DIC),而非直接运动学计算[23]。近的研究证明了双向斜拉伸试验的拉伸和剪切性能的耦合,其中也可以对样品施加横向负荷。这一研究发现,额外的纱线张力会影响剪切行为,也会减少面外屈曲(起皱)的发生[24]。然而,尽管不少研究致力于建立测试基准[25],但是织物剪切测试至今仍然没有标准。
2.1.3. 弯曲表征
由于纱线和纤维之间的内部摩擦,编织增强材料在加载和卸载时表现出弯曲滞后现象[26,27]。因此,假定线性弹性弯曲行为的传统悬臂弯曲测试对于这些相对较厚和坚硬的材料来说并不理想。Kawabata评估系统对织物的弯曲测试也是如此。因此,通过结合机械和光学测量技术,改进原始悬臂梁测试,以确定非线性和非弹性弯曲行为[26]。另外,Harrison等[24]基于对剪切张力耦合实验期间产生的褶皱的研究,提出了一种用于表征弯曲行为的反推法。预成型材料的弯曲特性会影响悬垂过程中褶皱形成的性质,对于复杂复合结构的制造和开发来说,这是个重要的问题。
2.2. 早期悬垂模型
早用于预测织物变形行为的方法是由Mack和Taylor在1956年提出的基于几何映射的方法[28]。这些“渔网”模型或者“运动学”模型将织物描述为枢接网络,忽略所有纱线的拉伸和滑动。虽然这些模型相对简单而且有效,但是不能解释压力、拉力或剪切闭锁等机械现象,所以仅限应用于无孔、桥和复杂曲线的简单问题。因此,运动学模型终被更强大的形成算法所取代[29]。20世纪90年代,电脑动画和服装工业研究了基于粒子的悬垂模型使用情况,此模型将织物描述为具有有限材料性质的微机械结构元素的不连续片层[30]。尽管上述模型在美学意义上获得了成功,但忽略了所有变形及压力的技术计算,因此并不适用于工程应用。后来,这些模型被连续、离散和半离散模型所取代。
2.3. 连续介质方法
用于悬垂模型的连续介质方法从扩展已有的有限元金属成型模拟开始[31]。该宏观尺度模拟需要标准的有限元,通常是壳单元或膜单元,并且假定编织增强材料是均相片层材料。因此,基于连续介质的悬垂模型的准确性主要取决于其本构模型的实现和材料性质的定义。这种方法的一大限制在于不能预测纱线的滑动,除非该行为是材料的固有属性。此外,面外行为也通常被忽略[32,33]。
虽然大量的本构模型已应用于连续介质方法来模拟织物悬垂,但是通过采用非正交方法和各向异性方法,能够采用更有效的方法跟踪并更新纤维变形的方向。较之大部分有限元软件包里的标准正交方法,这些更新的材料行为规律明确表现出这些方法的显著改进。超弹性模型和次弹性模型是两种更成功的、用于编织增强材料的本构模型方法。超弹性模型考虑到大变形、各向异性和非线性弹性因素,所以常被用于在高应变下表现出弹性行为的橡胶或弹性泡沫。这些方法由应变能量泛函计算应力,并且能够在织物悬垂时跟踪纤维变形的多重方向。Ten Thije等[34]结合了一种这样的方法,该方法来自亥姆霍兹自由能定律。
相比之下,次弹性模型在包含材料的拉伸模量和剪切模量本构参数张量的情况下,将应力增加与应变增加直接相关。次弹性本构模型对于具有可逆非线性行为的材料为有效,通常应用于大应变下各向同性分析[35]。不过,对于织物悬垂模拟,Yu等[36]和Xue等[37]已对非正交次弹性模型进行了研究。这些模型已经应用于织物悬垂相关的各个方面[32,38],包括纱线行为的介观尺度模拟[35]。目前,已采用非正交次弹性连续介质方法对机织复合增强材料的宏观尺度模拟进行了研究[33,39,40]。较之Jaumann和Green-Naghdi传统的假定正交变形行为的方法,超弹性和次弹性本构模型都表现出显著改进[34]。
2.4. 离散和半离散方法
离散和半离散方法考虑了材料内部的离散织物甚至是纤维的排列和相互作用,避免了编织增强材料在宏观尺度的均化,取而代之的是织物介观尺度或微观尺度的特征。目前仍无法实现每条纱线内的每根纤维在介观尺度和微观尺度上的模拟,因此,这些离散方法尚需一定程度的简化,通常用梁元或桁架单元来代替纱线,使用弹簧来模拟相互作用或剪切效应[41]。介观尺度模型研究用含有48个离散梁元的集合来代表纱线,代替了数千根独立的纤维[42]。该方法运用了增强的运动梁模型以及先进的纤维摩擦和接触算法,以便更好地预测编织增强行为。由于所有的材料连续性假设都被限制在纤维束上,因此在介观尺度上,有望模拟纱线滑动行为。然而,由于计算量的关系,这一方法不可用于整体宏观尺度模型。
在其他研究中,为了更好地预测不同织物的介观尺度行为,在三维固体结构内的重复单元(RUC)对纱线进行模拟[43]。如果能够准确定义织物的变形和接触作用,那么这一方法就有望预测纱线的滑动。然而这些行为难以表征,所以这些模型对于介观尺度的应用还有很大限制,一般用于预测材料的特性[16]。
结合离散方法和连续有限元的实验,得到半离散方法这一混搭组合,由特定元素的连续片层来代替编织增强材料。为了提高效率,每种特定元素都由整数个织物RUC[44]组成,这意味着整体宏观尺度模拟具有可行性,可以结合弯曲行为更好地进行褶皱模拟[45]。比如,Allaoui等[46]采用半连续悬垂模型来解释弯曲行为,提高了对冲压成型过程中褶皱行为的预测。半连续方法直接从纱线张力、面内剪切和弯曲定义了单元结构负荷,而非从应力张量进行定义。因为半离散方法采用了连续介质方法,忽略了纱线的滑动,所以其可能会高估面内刚度。然而,半离散方法比连续介质方法对于材料的综合特性要求更少,并且比离散方法更有效。后,研究显示,尽管开发半离散方法相当复杂,但其是织物悬垂模拟实际的方法[47]。
3. 灌注模型
树脂灌注模型的主要目的是预测流体流动行为以及证明在树脂的工作期限内能够成功地进行生产,避免在部件内留下干点和空隙。此外,灌注模型也能够帮助设计和开发生产策略,尤其是确定出料和进料的位置,以及流动增强介质分布[48]。
通常采用Darcy法则来描述树脂通过复合增强材料的灌注行为,如方程(1)所示,该法则假定牛顿流体低流速通过多孔介质是合理的:
这个方程将流速v、渗透率K、流体黏度μ和系统压力梯度ΔP相互关联。上述参数中,流速和压力梯度在大部分生产情况下都容易测量和控制。但是,织物渗透率是一大难点,必须通过实验方法或者模型预测来表征,以便有效地进行灌注行为模拟。
3.1. 渗透率表征
渗透率表示流体通过多孔材料的容易程度。对于编织增强材料来说,大部分灌注应用依赖于各向异性平面渗透性质。然而,在厚度较大的情况下,厚度方向的渗透率也十分重要。研究显示,大部分预浸渍织物的横向渗透率比面内渗透率小1或2个数量级[49],因此对于薄层织物的流动影响不大。
织物中的各向异性渗透率通常由两个主要的渗透率值K 1 和K 2 以及主要渗透率方向φ定义[50]。尽管织物渗透率在灌注模型中十分重要,对该领域也进行了大量研究[51],但是迄今为止仍没有标准的测试确定这些性质。根据文献记载,现有的测试方法具有很大的差异性[52,53]。这一差异来自于复杂流体的两个尺度:黏性流体在纱线间的流动以及每根纱线中纤维之间的毛细流动[54]。机织纱线的随机性、对于手工操作的敏感性以及厚度效应也是实验差异性的原因[55,56]。因此,初关于基准渗透率测试的尝试表明,对于同种材料,不同实验室和不同实验方法可能会产生整整一个数量级的差别[52]。即使在同一个实验室,相似的方法也可能导致超过±30%的相对标准偏差[52]。不过,新的基准测试结果显示,此误差明显减少,不同实验室采用同种方法能够达到±20%的相对标准偏差[53]。
3.1.1. 实验方法
渗透率表征实验通常用来确定编织增强材料的面内性质,而非贯穿厚度性质。两种常用的面内表征方法是线性流动实验和辐射流动实验。线性流动实验监测线性流动前沿从增强材料矩形样本的一端流向另一端,而辐射流动实验跟踪椭圆流动前沿从入口处出发的二维走向[50]。恒压或恒流速状态下,两种方法都能够用于材料的饱和状态(预浸渍)和不饱和状态(干燥)。测试流体通常采用能够代替加热树脂的植物油、玉米糖浆、机油或硅油。线性测试通常显示出更好的重复性[53,57]。然而,对于各向异性织物材料,线性测试的实验次数远多于辐射测试,辐射测试能够仅通过一次实验就确定各向异性渗透性质。
渗透率实验通常依赖于可视化实验方法[58],但是也经常使用热量、电和压力传感器[59]。Ahn等[60]研究了用于三维渗透率表征实验的埋入式光纤传感器。任何情况下,都要确保测试腔具有足够刚性,以抵抗可能影响流体行为和渗透率计算的挠度。
3.1.2. 预测模型
为了克服实验表征方法的繁琐和不可靠问题,大量研究工作已经对预测渗透率模型进行了研究。初,Kozeny开发了多孔材料的渗透率模型,随后Carman[61]对其进行了修正。Kozeny-Carman公式假定了通过一组管路的层流流体,以代表通过多孔材料时的渗透行为,这个公式依赖于几个不可测量的参数。另外也提出了用于预测UD增强材料渗透率的润滑模型[62],该模型假定了正方形或六边形纤维堆积方式。但这些模型都不能严格用于真正的双尺度问题,因为在双尺度问题中纱线间大孔和纱线内微孔同时存在。其他研究在不同程度的几何简化条件下,通过织物结构RUC来模拟流动[63,64],其中一种就是使用晶格玻尔兹曼模型[65]。所有方法都基于理想化的纱线截面和波纹。实际编织增强材料的截面也通过光学相干断层扫描进行成像,用于预测渗透性质[66]。
Nedanov和Advani[67]以及Takano等[68]运用另一种两步法来进行渗透性的预测,从而解释双尺度渗透性的影响。先根据单根纤维之间的流量计算纱线内部渗透性,然后确定通过大孔的纱线间的流量。一般认为,纱线内部渗透性比织物结构小两个数量级[67],因此通常被忽略。其他运用到基于体素的有限差分法[69]、三维代表性体积单元法[70]或降维网格法[12,71]的模型也得到了发展,以提高效率。丝束间距和铺层等随机变量也被用于编织增强材料的研究[72,73],但在预测渗透性模型中并未得到充分考虑。
尽管这些表征模拟相对来说较为迅速,但它们倾向于通过多孔织物的增强来过度简化真实的流动情况。此外,这些方法的有效性和准确性仍然依赖于大量的实验测试。因此,尽管这种方法存在重复性问题,但考虑到精确度,渗透性实验法仍然是选。
3.1.3. 形变依赖性
织物形变对渗透性有显著影响,例如,纱线重组能够影响材料的孔隙率和纤维体积分数。在制造简易平板时,这并不是问题。然而,在制造具有较大曲率结构的材料时,广延的剪切变形将对渗透性以及灌注过程中树脂的流变性能产生强烈影响。这种现象得到了广泛研究;在许多情况下,由于剪切力的作用,因形变而改变的材料渗透性能够产生超过50%的波动[12,70,71,74]。Hammami等[74]发现由于剪切角增加,K1 主渗透性值增加,同时K2 值减小,导致缝合双向非卷曲织物的各向异性增加四倍。Slade等[75]对缝合织物和机织织物进行了类似的观察。与之相反,Endruweit等[59]发现随着剪切角增加,多种织物结构的两个主要渗透性值呈现总体下降的趋势。进一步的实验和数值研究表明,随着剪切变形的增加,渗透性下降的趋势是相似的[10,64,70,76]。
3.2. 流量模拟
通常使用Navier-Stokes方程和Darcy定律[方程(1)]的推广形式模拟流过多孔介质的流体,包括对流项和扩散项。在工业上使用的大多数流动模型都依赖于近似均匀连续的预制件区域,并且,在可能的情况下忽略贯穿厚度效应、饱和度、压实和热传递。边界元法等早期的方法存在质量守恒问题,而拉格朗日有限差分法局限于简单的几何形状[77]。由于材料日益复杂,发展了许多纯粹的有限元法,用于解释材料间热交换、压实和全三维流动的情况[78]。另外,“水平集”方法已经显示出颇具前景的二维结果[79],但尚未能够推广至更具挑战性的问题。然而,通用的灌注建模方法倾向于控制体积/有限元(CVFE)法和流体体积(VOF)法。
3.2.1. 控制体积 / 有限元法
CVFE法在各种情况下相对有效、准确,并且能够考虑合并流量和可变的预成型件厚度,因此在灌注建模中非常常见[49,80–83]。这些方法通过仅仅模拟树脂相简化了灌注问题,忽略所有气体,使用时域中的显式积分来解决小的连续稳态流问题。
Phelan[83]于20世纪90年代后期提出的流量分析网络法是CVFE法的代表。利用这种方法,域被分为单元和节点,同时每个节点独立地控制体积分配,如图4所示。利用基于达西定律和不可压缩的牛顿流体的质量连续性方程的有限元法来确定入口和流动前沿之间的压力梯度,随后计算速度场以及与流动前沿相邻的每个控制体积所需的填充时间。其次,将填充一个单元所需的短时间用作下一个时间的增量,其确保流动前沿至少前进了一个控制体积的距离。然后其他相邻的单元仅仅被“部分填充”,这就确定了新的流动前沿位置的数值。由于只需求解一个微分方程,即使对于粗糙的网格,这种方法也是十分有效、稳定[84]。但是,由于每次的时间增量只能填充一个单元,因此,对于具有较大数量控制体积的模拟,解决速度缓慢。
Bruschke和Advani[80]使用CVFE早期模型来模拟纤维预制棒材料中的二维、等温、各向异性的流动,其他研究人员也纷纷效仿这一做法[82]。如Park和Kang[85]所描述的那样,使用浮动假想节点和元素的方法也能够使流动前沿变得平滑。此外,?imá?ek和Advani[49]使用特拉华大学开发的液体注射成型模拟软件,进行人造丝束饱和度的建模。
3.2.2. 流体体积法
VOF法[86]的基础是较老的标记单元方法[82],它能够模拟一组拉格朗日标记粒子穿过计算欧拉网格的情况。这些方法对于多相流的模拟是理想的,在多相流中存在两个以上的流体,但这些流体不能占据相同的体积。在VOF仿真的每个控制体积中,所有相的体积分数总和为1,并且对于所有流体相,采用同一组控制方程来表述。方程(2)~(4)分别表示流体连续性、体积分数和动量。
同时,因为这种方法需要求解偏微分方程组,所以如果没有建立好网格和离散化时间,求解时就会遇到收敛性的问题。然而,VOF法在模拟明渠等渗透特性差异明显的区域非常有效,在这种情况下,CVFE法则不可解[84]。
3.3. 其他思路
除了影响树脂流动行为(渗透性、压力、黏度和入口/出口位置)的基本建模因素之外,还有许多其他因素也能够改进流体建模。由于编织增强材料的属性本质上是可变的,且易于处理和切割,目前已经开发了一种可以预测和说明潜在流动干扰的概率工具[87]。鉴于在边缘或节点处的轨迹跟踪效应能够显著影响流体流动现象,因此,任何既定的灌注方法都必须考虑到这一点,这非常重要。
对被动控制也进行了一些研究,如附加出口,当树脂填充通过时,出口关闭,以及常被用于真空辅助树脂灌输过程的流动增强材料。建模时,被动控制会在优化灌注方法的过程中增加复杂性;因此,使用高级算法来更好地预测流动增强介质的佳形状和位置[88]。当存在大量变量时,用于优化入口和出口位置的“蛮干”算法极其耗时。因此,质心Voronoi图[89]等更复杂的方法已被证明能够大大减少有效优化所需的仿真迭代次数。对主动流量控制措施也进行了研究,如在零件的不同入口位置处使用活压或流量控制[90]。然而,这些方法明显使预测建模变得更为复杂,因为建模时必须考虑用于附加传感器和变流量入口的合适位置。
贯穿厚度效应、工具压实和空隙形成都可能成为灌注过程中的重要问题。对于许多薄的复合材料部件,贯穿厚度效应和工具压实往往被忽略。然而,对于较厚的叠层,则需对三维流动和工具压实进行准确预测。对于依靠柔性加工的工艺而言,工具压实尤为重要,因为树脂渗透增加内部模具压力,这将导致工具变形[91,92]。例如,已对短切原丝毡灌注过程中干湿压实的效果进行了研究,并且使用一维Galerkin有限元法[93]进行了模拟。压实行为的介观尺度力学建模也与实验测试结果一致[94]。灌注过程中空洞的形成和运动十分常见,并且对预制件的饱和度和终部件性能造成显著的影响[95]。近期的研究工作使用了无量纲的“修正毛细管数”来预测基于具有一定比例黏性力和表面张力的树脂流动前沿处的空隙形成、泡沫压缩和运动情况[54]。
4. 过程建模
完整模拟树脂灌注制造过程极具挑战,因为需要考虑预制件的力学性能、树脂通过变形材料的流动,甚至在一些情况下的固化行为。材料的变形会影响渗透性、饱和度和空隙,这使得情况更为复杂。另外,对于采用柔性材料的工艺来说,相当大的压实效应可能会影响灌注过程中的填充性能。
鉴于这些挑战,建立一个能够包含所有必要影响的模型相当困难。然而,研究人员正在开发一种能够解释部分多学科影响因素的模型。传统的模拟将成型和灌注视为完全独立的过程,因此,新的模型将更为完善。
早在15年前,Lomov等[11]和Verleye等[12]提出了能够预测整个制造过程和终部件性能的概念——“集成设计工具”。近的研究工作在考虑饱和效应的基础上解释了结构变形对灌注过程的影响[96,97]。但是,在本文的后面几个部分将提到,这种过程建模近才被实验彻底验证[98]。
5. 多物理场流程模拟的论证
已开发出一种多物理场流程模拟,能够更真实地预测真空辅助树脂灌注过程中的结构变形和树脂流动情况。如图5所示,该流程模拟集成了一系列特征测试和数值模型,以实现这一目标[98]。该模型的基础是一个连续悬垂模型,先被ABAQUS ? 用于预测结构变形的程度。然后将该模型的结果传递给ANSYS Fluent ? 灌注模型,以预测树脂流经变形的增强材料的流动情况。尽管形变依赖的渗透性以及悬垂结果也相当重要,悬垂模型的准确性取决于结构拉伸和剪切特性的表征,而其准确与否也决定着灌注模型是否正确。一个具体的自定义的子程序(如ABAQUS/Explicit ? 中的VUMAT子程序)定义悬垂材料模型以及材料属性,以便实际地追踪非正交的纱线旋转过程。类似的,在ANSYS Fluent ? 流动模型中,自定义函数(UDF)的子程序可用于在灌注区域上分配可变渗透性属性。该多物理场流程模拟的完整细节可参阅文献[98],下文将重点介绍其新的应用,并且验证全尺寸成型实验和灌注试验。
5.1. 全尺寸实验
为了评估多物理过程模型的有效性,真空灌注实验在一个大的“双圆顶”材料上进行。文献中详细记载了这种用于成型研究的常见复杂几何形状[33,40]。这种压入式模具由结构泡沫构成,涂覆,并凹入120 mm深、尺寸为950 mm×550 mm的外框中。外框与双层圆顶材料高度相同,与将真空袋直接放置于模具顶部正上方相比,可以使真空袋与模具更好地贴合并防止起皱。
将干燥的平纹碳纤维材料的单层切割成800 mm×500 mm,使其具有0°/90°或–45°/45°的纱线取向。然后,用50 mm银网格标记,以在整个成型和灌注过程中能够进行光学测量。将预成型材料、三个真空口和一些额外的配件放置在模具上方、真空袋下方[98](图6)。袋子在框架边缘密封,真空口连接真空泵,开始成型。一旦袋子和织物材料被拉到模具底部,模具长端的副真空口则连接到真空泵上,口关闭。彻底检查袋子和织物增强材料的整合性,以避免材料的凹陷区域中受到桥接的影响。
灌注时,将端口连接到储油器上,打开储油器激发流体流动。使用橄榄油作为典型的测试流体,因为它具有0.084 Pa·s的标准室温黏度,这与典型的灌注树脂具有相似的黏度(0.001 ~ 0.3 Pa·s)[8]。测试过程中,定期拍摄图像,记录每个样本的流动过程。图6直观地描述了全尺寸演示实验的成型和灌注过程。
5.2. 悬垂模型
在ABAQUS/Explicit? 中采用一个连续的悬垂模型用于典型的双圆顶部分,这类似于Khan等[33]、Peng和Rehman[40]的研究工作。单个织物层作为连续的薄膜元件片,而定制的VUMAT材料子程序为其提供低弹性材料模型。该子程序设计用于追踪整个成型过程中实际的非正交纱线取向,并根据实验表征的拉伸和剪切性能(E和G12 )来计算材料响应性。该子程序的开发和实施在文献中详细记载[99]。该研究忽略了材料的弯曲效应。
根据标准ASTM D5035-11[19],对于具有3K丝束和0.193 kg·m–2 面密度的干碳平纹织物,织物拉伸性能由单轴条测试确定。实验记录下了具有近似线性的弹性响应,拉伸模量E为15 GPa。
进行斜拉测试以表征平纹织物的剪切行为,通过使用DIC来增强应变测量。该测试的完整细节已发表[100]。研究发现,一个指数函数适用于高度非线性剪切响应。因此,用方程(8)来描述织物的剪切模量G12 ,从而发现低剪切角下纱线旋转的相对自由度和明显的剪切锁定现象[33,39,40]。
5.3. 灌注模型
鉴于该建模侧重于论证变形依赖渗透性行为,因此假定等温条件,并且大大忽略饱和度和压实效应。考虑到灵活性和可靠性,将ANSYS Fluent? 应用于灌注模型,主要采用欧拉VOF方法。因此,在灌注过程中,充满树脂和空气的整个区域可被视为相互贯穿的连续相。
为了验证灌注模型,在一定的织物剪切变形范围(0°~40°)使用非饱和径向流动实验进行渗透性测试。实验方法和渗透性计算的全部细节记载于之前的研究工作[101]。渗透性测试结果显示K1 值增加,K2 值随着剪切角增加而普遍下降。因此K1 增加和K2 减小的综合作用结果就是直接导致各向异性的大幅增加。然而,由于渗透性测试是在刚性板之间进行的,而全尺寸实验在套袋膜下进行,所以需要进一步校准。在实验观察的基础上,整个剪切角范围内以及在所有具有不同材料取向的建模中,将恒定校准因子K 1 和K 2 的数值分别定为0.667和0.5。灌注模型的多项式渗透性曲线由方程(9)和(10)定义。主渗透性方向φ可用方程(11)进行模拟,其方向从与纬纱初始方向对齐过渡到在较高剪切角度下与织物偏置方向对齐。
在ANSYS软件套件中,使用来自“变形几何”文件的节点位置数据对灌注区域进行重新建模,节点位置数据由悬垂模拟生成。在该软件中保留了对称象限和一个0.4 mm的域厚度,而新的网格由大约1000个元素组成。为了更好地表示入口条件,在域中分割出一个直径50 mm的区域。如图7所示,自由滑动(对称)边界条件被应用于除了入口和单个出口以外的所有畴壁[98]。入口和出口压力分别为101.3 kPa和0.3 kPa,未变形的基准材料孔隙率为0.724。根据实验测量的黏度-温度曲线,0°/90°和–45°/45°取向情况下的油黏度分别为0.0756 Pa·s和0.0993 Pa·s。
初始化模型之后,运用UDF子程序来收集和存储所有来自“分布式属性”文件的信息,将局部剪切角度转换成基于方程(9)~(11)中的局部渗透性。然后将这些属性按照单元逐个分配,即可得到基于原始剪切变形的复杂流动特性图,如图7所示。
5.4. 结论
5.4.1. 悬垂
不同样品在不同取向上重复测试,证明平纹材料能够很好地与模具贴合,没有任何起皱迹象。在每个测试的四个象限中观察到良好的对称性,样品边缘只有微小的磨损(图8)[98]。每个测试的四个象限的网格点位置平均并与模拟悬垂结果进行比较,结果发现预测的网格位置与平均实验结果相比误差小于2%。
此外,如图8所示,在每个对称象限的多个位置观察剪切角,以便与悬垂模拟结果进行比较。0°/90°取向样品的实验剪切角值在0°~36°之间几乎没有变化。对于–45°/45°取向样品,实验剪切角为–24°~15°。如图9[98]所示,在0°/90°和–45°/45°取向的情况下,实验结果和模拟结果终能够很好地吻合。
5.4.2. 灌注
灌注实验在两种织物的取向上都是可重复的,未显示出流道跟踪行为。为了更好地展示多物理场流程模拟的优点,即考虑到形变依赖的渗透性,传统的各向同性灌注模型也适用于类似的条件。基于来自实验渗透性表征的经校准的K1 和K2 平均值(K1 = K2 = 3.3×10 –11 m2 ),在灌注区域上应用材料的各向同性和均匀渗透性性质。0°/90°和–45°/45°取向样品的实验和模拟的流动前沿分别如图10和图11所示[98] (分别在1255 s和850 s情况下)。正如文献中实验验证的结果,模拟的流动前沿视为0.5相位的油和空气体积分数的等值线[98]。在各种情况下,多物理场模型与实验结果基本一致,而基本模型无法表征因局部剪切而引起的增强流动。图10明确显示了高剪切变形区域的各向异性行为。
值得注意的是,图10和图11的照片中存在由广角摄像机镜头导致的透视畸变,在圆顶的凸起区域,这一情况尤为明显。然而,由于确切的双圆顶几何形状和网格尺寸都是已知的,因此,每个测试的真实流动前沿位置很容易计算。由此得到图12和图13[98],显示在每个方向不同填充时间,多物理场模型实验和基本模型之间更准确的比较结果。这些结果表明,尽管更高级的模拟仍与实验结果存在不同,但相对于基本模型而言,改进了多物理学方法。
6. 总结
对于更大、更复杂的航空结构的需求日益增长,非热压罐成型技术能够满足对于编织增强复合材料的需求。同时,流程建模正逐步取代传统的部分开发方法,大大节省时间和成本。这类建模越来越依托于整合了各种学科模型的多物理场模拟。使用编织增强材料进行树脂灌注制造时,织物的物理悬垂和随后树脂流过材料的过程是该工艺的关键阶段。为了准确预测这些数据,已研究了一系列用于不同尺度的方法。为了支持建模,尽管在材料特性的表征方面已投入了大量的研究工作,但仍需进一步的研究和标准化,才能使流程建模充分包含编织增强材料的多尺度行为。
近开发的多物理场流程模拟相对于传统建模方法具有显著的提升。通过考虑变形对渗透特性的影响,这种先进的模型能够更好地预测全尺寸双圆顶灌注实验中的流动性能。但模拟结果与实验结果仍存在一定差异,可能是由于模型忽略了压实效应和渗透性的不准确而导致的。在这种情况下,单层测试为模型提供了研究实际流动行为能力的新方法。然而,为了在工业领域产生更大的影响,未来尚需对多层应用进行研究。