兰普夫公司的制造和工艺解决方案包括材料鉴定、综合质量保证和自动化方面等,方案适用于结构件和内部应用。这种方法的好处在具有高度几何复杂性结构(下凹、弯曲、凹陷等)和必须满足难度高的功能规格(电磁屏蔽、静电放电、冲击保护、阻燃)的部件制造中尤其明显。
量身定制的纤维放置包括确定的刚度和强度,通过在需要强度或重量优化的地方有选择地放置和排列碳纤维和玻璃纤维丝来实现大化。这优化了轻量化部件的结构性能--同时大限度地减轻重量,减少碳纤维消耗和成本。
特殊的液体树脂系统(具有或不具有FST特性)能快速有效地渗透到TFP预制件中:除了具有良好的润湿特性外,这些系统还适用于低温加工,例如,在40℃下进行树脂灌注。此外,关键的工艺步骤 - 如混合、脱气和计量 - 基本上都是自动化的。
该公司列举了用几乎完全由碳纤维复合材料制成的轻量化部件替代商业飞机中使用的不锈钢部件作为这种完整解决方案潜力的一个例子。该零件的重量减少到原来零件的五分之一左右,同时没有增加成本。
根据兰普夫公司的说法,用户通过这种显著的减重措施甚至实现了额外的运营成本节约。此外,只需生产5个预制板铺设工具。如果采用传统的复合材料设计方法和材料,预制板铺设工具数量将是75个。现在几乎所有的客机都采用了这个部件。
"通过我们的解决方案,在飞机减重与提高燃油效率方面,过程更加自动化和具有成本效益。我们高度熟练的专家团队处理设计复杂的复合材料飞机部件所需的所有任务-从草图到验证"。相关人员如此表示。
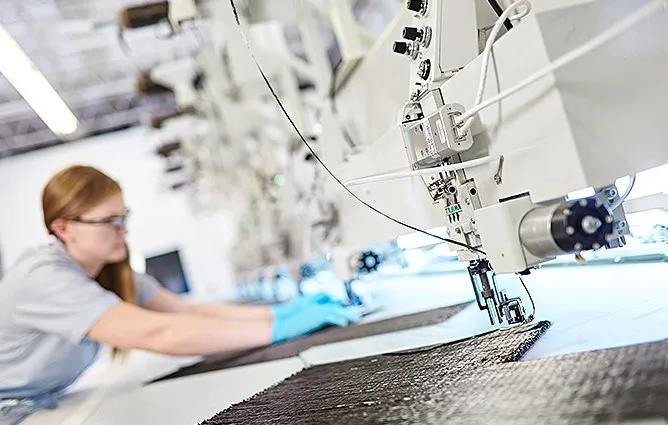
量身定制的纤维放置工艺有助于提高兰普夫公司的复合材料部件生产效率。