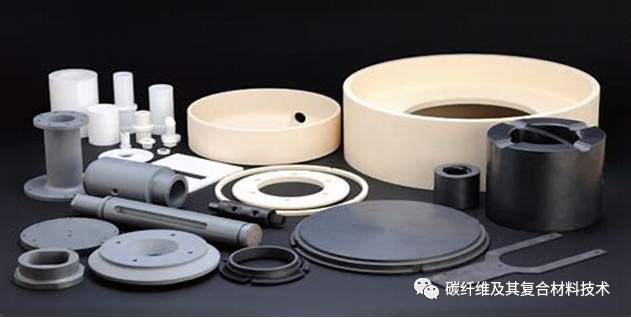
碳纤维/铝基复合材料的主要问题为碳-熔融铝的相互作用导致碳化铝Al4C3的形成。充满缺陷的碳化物层导致纤维强度下降,而碳化物层厚度随着时间的推移而增加,复合材料强度下降,如下图1所示,该图通过在800°C–36 MP–90 s下压力铸造得到的碳纤维/纯铝基复合材料,然后在600°C下热处理制备得到,纤维体积分数为14%,加热60小时后,约10%的碳纤维转化为碳化物。
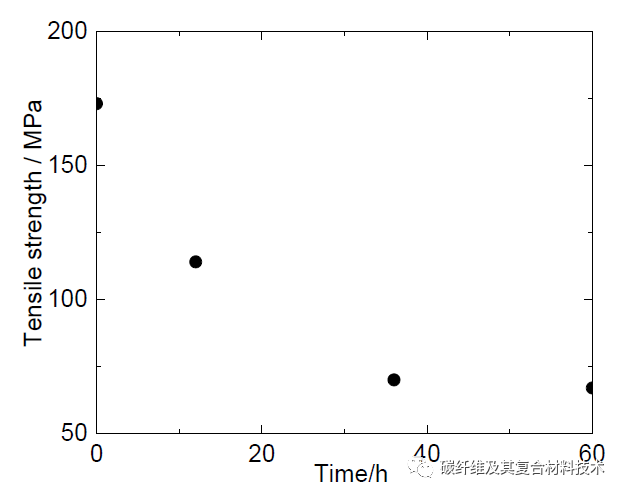
部分研究人员针对M40J基高模碳纤维和纯铝基体复合材料中碳化物界面的形成进行了细致的研究,他们通过在750°C–25 MPa–10 min条件下采用压力铸造制备了试样。发现由于碳快速扩散到熔体中,纤维表面缺陷上会出现碳化物夹杂。碳化物夹杂的生长导致相邻纤维之间形成脆性桥。纤维团簇降低了复合材料的强度。
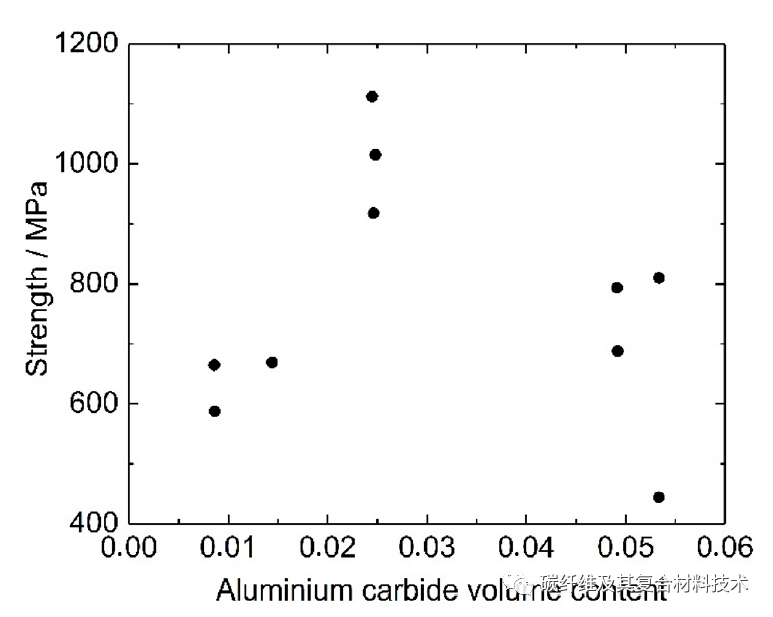
图2 碳纤维/铝基复合材料的弯曲强度与界面处碳化物相含量关系,其中纤维体积分数为46%
在过去的几十年中,碳纤维/铝基复合材料主要是作为具有高导热性和足够高强度的非结构应用材料而发展起来的。比如,采用强度为2200MPa、轴向导热系数为396w/(m∙K)的连续中间相碳纤维和纯铝作为基体材料。在接近铝熔点的650℃热压下制备了复合材料试样。
复合材料微观结构照片显示了一种非晶物质和一定数量的碳化物晶体,其强度和热导率的测量结果如图3所示。复合材料中临界纤维体积分数约为40%。在实际制造过程中纤维和铝之间的相互作用会导致纤维性能退化。复合材料在横向上的导热系数很低,这是由纤维上包覆的碳化物涂层的低导热系数决定的。
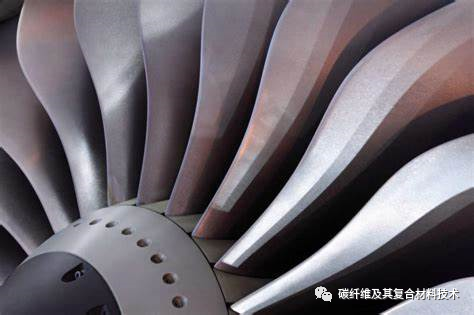
关于碳化铝对复合材料强度影响的最有趣的数据可能是由Portnoi等人发表的。研究人员通过在670至760°C的温度下压力铸造1分钟来制备复合材料。通过改变铸造温度会导致碳化物含量的变化,进而影响复合材料强度的变化(图2)。
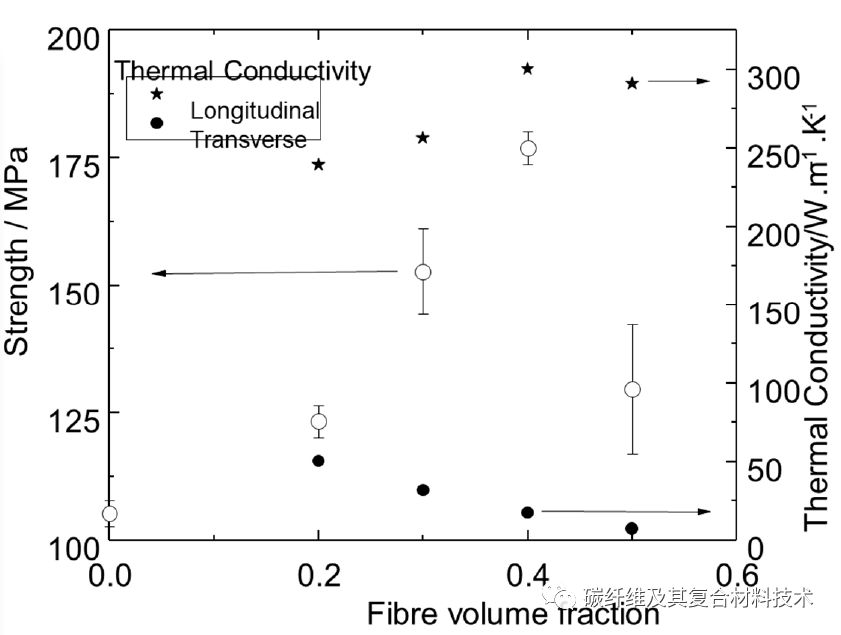
注意,复合材料的强度随着碳化物体积分数从约0.01增加到约0.03而增加。碳化物含量的进一步增加导致复合材料强度的降低。这可以通过纤维-基体界面的相应变化来解释。铝熔体不会润湿碳,因此短时间的熔体-碳接触会产生一层薄的碳化物层,这为纤维-基体界面提供了强度;但是充满缺陷的厚碳化物层导致纤维退化和界面强度降低。