用于高速生产和减轻重量的热塑性结构
弗劳恩霍夫协会与清洁天空2/清洁航空项目“大型客机”(“LPA- Large Passenger Aircraft”)的合作伙伴合作,首次在全球范围内成功证明,飞机机身的自动化兼容热塑性塑料制造方法既提高了高速生产的生产效率,又显着减轻了重量,从而使每次飞行的二氧化碳排放量减少了540公斤。该项目实现了10%的重量减轻和10%的生产成本节约,但远未充分发挥新设计与自动化生产相结合的潜力。
预集成结构和系统组件的自动化组装和连接过程
弗劳恩霍夫协会的贡献包括将全尺寸上壳与相应下壳的组装自动化,以形成直径为4米的8米长的“MFFD”机身段,以及开发用于热塑性CFRP接头的激光焊接和间隙填充工艺。
自动化方面的特殊挑战是,尽管组件尺寸很大,但精度要求很高,以及高连接力的管理和有限的可访问性。机身内部的这些局限性是由于两个180°壳体与结构和系统部件几乎完全预集成的开创性方法造成的。与目前在机身关闭后装备机舱和货物区域的方法相比,它为自动化、高速生产提供了相当大的优势。
通过焊接连接热塑性塑料
为了避免碳纤维含尘,在壳体精加工过程中已经使用了各种焊接工艺,而不是通常的钻孔和铆接工艺,这也是选择新型热塑性碳纤维复合材料的原因。
因此,机身段装配的自动化特征是两个半壳相对于彼此的精确定位以及上壳的单独几何优化。这确保了机身纵向接缝的连接区域可靠地低于焊接工艺允许的所需公差。焊接过程中外部产生的高连接力被自动压力工作站吸收并消散在机身内部,以防止损坏CFRP结构。
只有当定位、提供额外的连接元件、加热、间隙填充和压制等部分平行和部分顺序的运行子过程在时间和空间上由中央控制系统精确协调和监控时,才能保证完美的接头。因此,所使用的两种焊接工艺,一种纵向焊缝的CO2激光焊接和另一种纵向接缝的超声波焊接,都有望达到高度的完美。
飞机制造和…
所获得的结果为未来的飞机生产开辟了一系列新的选择,主要是使用轻质热塑性碳纤维增强塑料材料,并结合适用于该材料的连接工艺。与以前常见的铆接接头的集中载荷不同,它具有表面宽的力传递,这允许在较低的壁厚下具有相同的强度,从而进一步减轻结构重量,分别节省更多的燃料。与现状相比,在关闭机身之前预先集成外壳使自动化过程管理变得更加容易,从而可以进一步降低时间要求和成本,以实现高速生产。
…其他分支
结合从“MFFD”演示器中获得的知识,弗劳恩霍夫协会将为感兴趣的公司提供成熟的技术模块用于工业化。其他技术将被纳入后续的研究项目,以便在未来的生产中以更低的资源消耗实现更大的效率提高。除了飞机机身,目标结构还包括垂直尾翼和低温氢气储罐系统。在航空业之外,陆地或海上交通工具也是技术转让的重点。
致谢
所述结果由弗劳恩霍夫与项目合作伙伴合作开发(见https://s.fhg.de/9T4). 弗劳恩霍夫感谢项目合作伙伴的成功合作以及欧盟委员会的资助。

约克·罗斯(YorkRoth)(空中客车公司)很高兴代表所有MFFD项目合作伙伴(f.l.t.r)与LarsLarsen(DLR)、乔斯特·库普曼(JoostKoopman)(GKNFokker Aerospace)和本杰明·迪尔(BenjaminDiehl)(FraunhoferGesellschaft)一起获得2025年JEC复合材料创新奖。
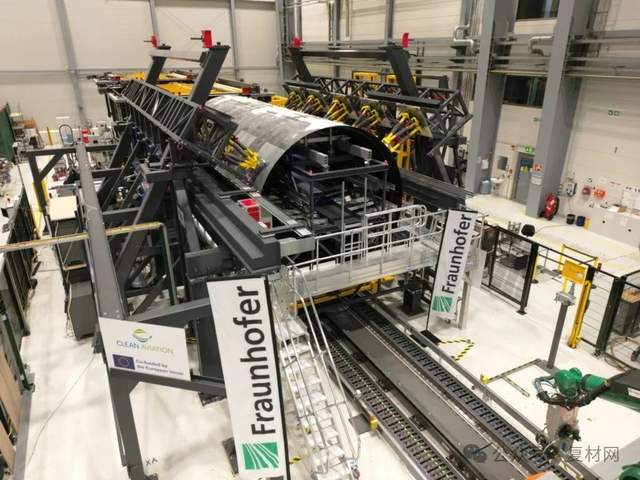
位于施泰德的弗劳恩霍夫协会的“MFFD”热塑性机身外壳装配研究平台。黄色的六足机器人清晰可见,用于保持和高精度调整上壳的形状和位置。
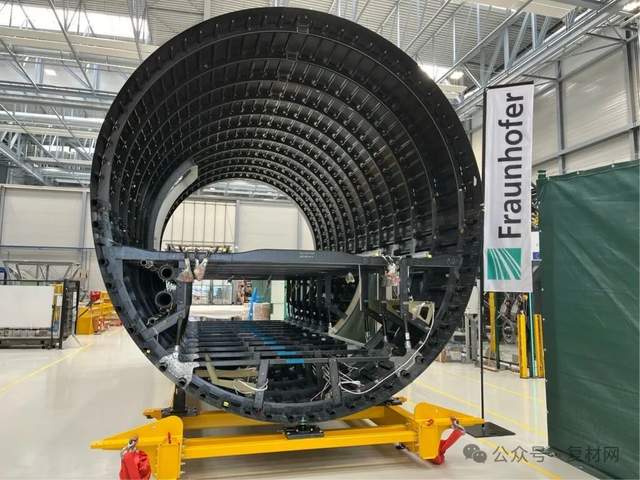
位于施泰德的弗劳恩霍夫协会通过热塑性焊接连接的“MFFD”飞机机身段。
原文,《JECComosites Innovation Award 2025 for the Multi Functional FuselageDemonstrator -MFFD》2025.1.13
杨超凡 2025.3.5