引言
随着人们出行越来越多地使用汽油、柴油等化石能源,机动车每年排放大量的CO?,地球的环境温度正逐渐上升。过多的燃油消耗也使我国原油对外依存度在2016年就已经远超国际安全警戒线,高达65. 4%。我国的汽车保有量正逐年增加,截至2018年12月底,汽车保有量已经高达2. 4亿辆。为了应对日益迫切的气候危机及我国能源对外依存度问题,需要大力发展新能源动力汽车。目前新能源汽车261万辆,仅占2. 4亿辆机动车保有总量的1. 09%,仍 有非常大的发展空间。
多国均推出了鼓励发展新能源汽车的政策,我国工信部推出的2018 新能源汽车政策中补贴较以往减少了20%,但是新的补贴方案更加鼓励电池能量密度高、续航里程高、百公里耗电量低的车型,这大大激励了整车厂对高续航、高能量密度电池系统的电动汽车开发。降低整车的质量能够提高电动汽车的续航里程,缓解人们的里程焦虑,并且同时降低了对百公里行驶电耗成本和电池总电量的需求,降低了电池的使用成本,这使得新能源汽车的轻量化效果比燃油汽车更加显著。国内某型号的纯电动城市客车,其质量减轻100、500、100、1500kg 以及2000kg,续 航 里 程 分 别 增加0.55%、2.83%、5.83%、9.01%及 12. 38%。
1 、动力电池系统轻量化现状
较传统燃油汽车而言,电动汽车多出了核心的三电系统( 电池、电机、电控) ,其中电池 Pack 整包占整车整备质量的18%~30%,电动汽车的续航里程越大,其电池Pack质量占整车质量比重越大,如图 1 所示。续航里程较大的雪佛兰Bolt、奔驰EQC、捷豹I pace 以及Model 3 等,其电池Pack质量占比均超过了26%,因此对能源汽车动力电池系统进行轻量化开发就显得尤为重要。
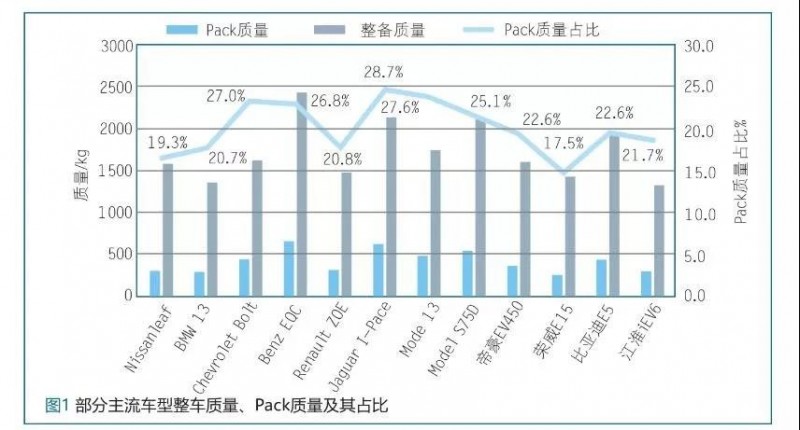
传统燃油车的轻量化研究已经受到了广大车企的重视,高强钢、铝合金、镁合金、复合材料及激光拼焊、热成型、液压成型、辊压等轻量化材料和工艺都得到了深入研究和广泛应用。新能源汽车由于电池Pack质量占比之大,不得不让各厂家均不断对电池Pack系统进行轻量化优化开发,如 Nissan Leaf代、第二代、第三代电池Pack含电24、30 及40kW·h,其Pack整包质量分别为272、293 及303kg,在同等电量下每代Leaf 的电池Pack均实现了不断减重。大众e-Golf 第二代含电35.8 kW·h,质量314kg,与代含电24.2kW·h 电池Pack 质量几乎相同。电动汽车中轻量化开发较优秀的如特斯拉Model3,电池Pack整包含80.5 kW·h 的电量,质量仅478 kg,整车整备质量已经和同级别轿车无异。
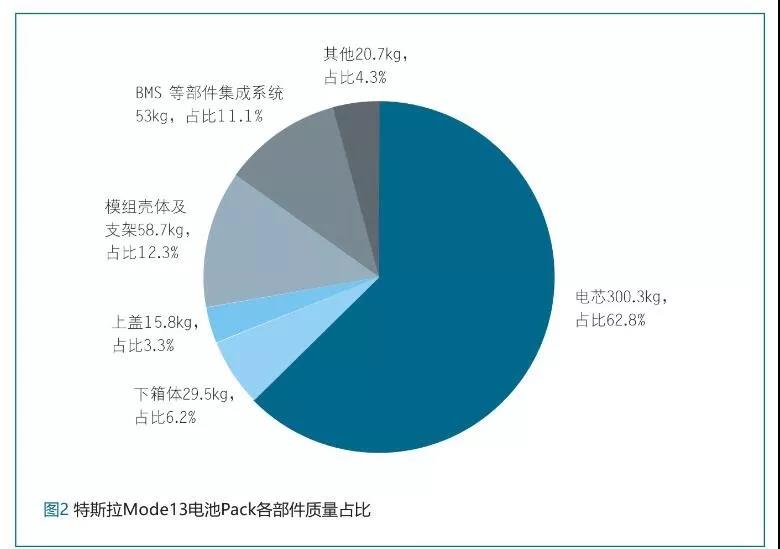
电池Pack各主要部件中,质量大的是电芯本体,其次为Pack下箱体、上盖BMS集成部件等。对特斯拉Model3 电池Pack拆解后称量各部件质量进行质量统计,见图3,电芯占据整个电池Pack质量的62.8%,其余部件为37.2%。
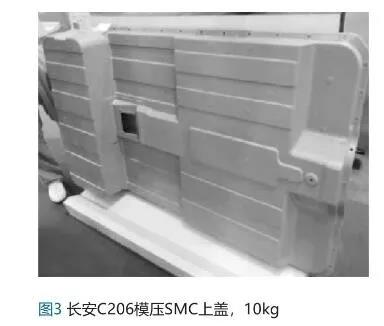
考虑用小质量的电池 Pack 存贮更多的电量,除了提高电芯能量密度之外,还需要降低除电芯中发生电化学反应的正极、负极、隔膜、电解液以外其他所有部件的质量,如电芯壳体、模组壳体、铝片、胶水、线束、连接片、Pack 箱体及上盖等。关于电池Pack的具体结构,SAW等研究了不同类型的电芯、模组、电池箱体、热管理部件、电池监控单元等部件如何系统地有效集成为一个电池Pack。
本文作者将从电池Pack的各个部件、模块系统论述如何通过材料替代、优化设计以及电池Pack与底盘集成方案对电动汽车动力电池系统进行轻量化开发。
2 、电芯的轻量化研究及发展
整车轻量化可以通过轻量化系数来评价,它为包中整备质量、投影面积、扭矩、油耗等系数的复杂函数值。电芯的轻量化系数在业界内暂无的计算方法,目前可以用电芯能量密度来简单评价电芯的轻量化水平,即电芯能量密度 ( 质量能量密度) 越高,其轻量化水平越高。电芯的能量密度直接决定整个电池系统能量密度的上限,提升电芯能量密度也是提高电池系统能量密度有效的办法。
汽车市场批量化生产应用的动力电池体系主要有两种:( 1) 磷酸铁锂动力电池; ( 2) 三元锂动力电池 ( 镍钴锰及镍钴铝体系) 。磷酸铁锂电池能量密度低,但安全性高,多用于专用车及客车; 三元锂电池由于能量密度大、续航里程高,主要用于乘用车。
目前国际锂离子电芯能量密度高为Panasonic 的21700 圆柱NCA体系电芯,其余主流厂家量产的电芯能量密度及体系见表 1。
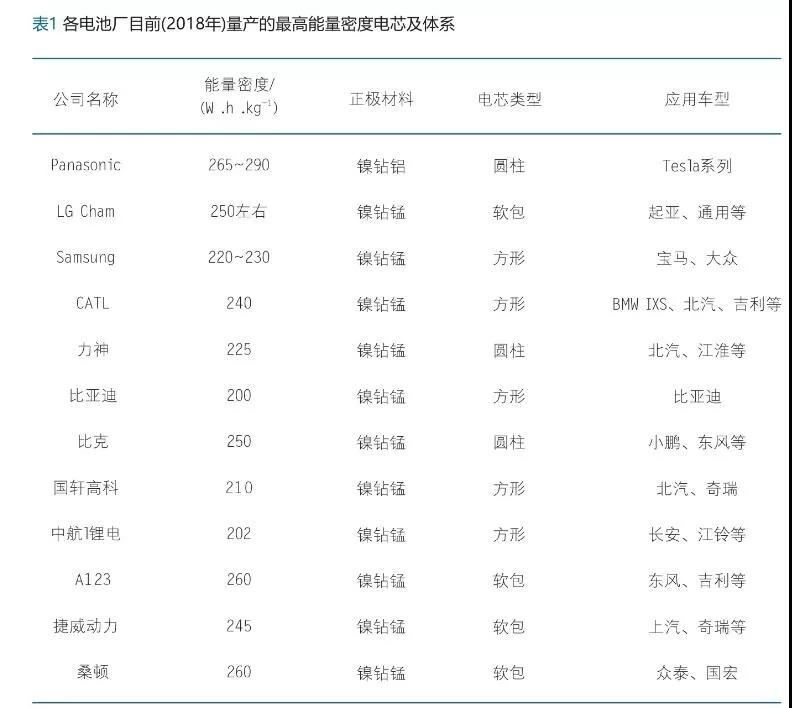
由于技术原因国内暂无厂家能量产NCA体系电芯。国内多家电芯厂商的NCM (811) 电芯技术路线体系均规划到2022年,其电芯能量密度可达到300~350 W·h/kg。现有NCM ( 811) 体系电芯的能量密度在短期内无法突破350 W·h / kg。各地高校、研究 所、厂家均正在大力研究以期能尽快突破并达到量产高能量度的电芯体系,目前在研较热门的3 个体系为固态电池、锂硫电池、锂空气电池,见表 2。
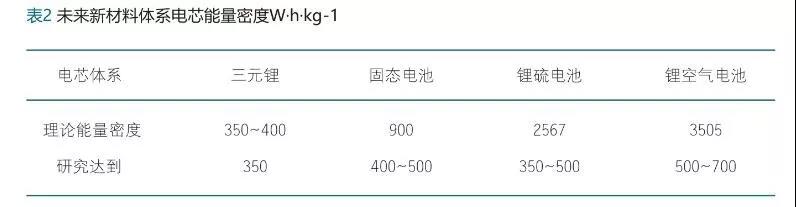
MISHRA 等讨论了近期锂离子电池正负极电极材料的发展并思考了未来的发展趋势。詹元杰、武怿达等对近期的300 篇锂离子电池论文进行了系统讨论,较为全面地介绍了当今锂离子电池的研究方向及突破。
电芯的轻量化系数 ( 能量密度) 更多地依托于新的高能量密度材料体系,含新的正负极材料、隔膜、电解质等。电芯其他部件中,如降低电芯壳体质量,也是降低电芯质量的措施。方形及圆柱电芯外壳由于需要一定的强度,多采用铝合金或不锈钢,未来可考虑强度更高的 7 系铝合金并通过降低厚度来达到减重的效果。软包电芯的铝塑膜较圆柱和方形电芯外壳具有天然的轻量化优势,故同体系、同电量电芯中,软包电芯质量会小。仅从电芯方面来看,软包结构是电芯轻量化的未来方向。
3、 电芯模组的轻量化研究及发展
电芯模组是包含若干电芯的一个电池模块,其作用是吸收电芯内部产生的应力及冲击,一是由于温度变化导致电芯产生的热胀冷缩,二是充放电导致的电芯体积变化。模组形状主要为方形,它主要由上盖、侧板、绝缘板、下塑料支架、上塑料支架、铝片等部件构成。
电芯模组的轻量化开发可以从模组壳体材料轻量化和模组结构轻量化设计及电芯优化排布入手。壳体材料可以采用全铝合金或者采用 7 系高强度铝合金并降低材料厚度来进行轻量化; 模组的结构轻量化设计及电芯优化排布,可以通过改进模组和热管理系统的设计来缩小电芯间距,以及错位排布来提升空间利用率,大限度地利用空间。模组内电芯的安装使用全塑料外框架,能大限度减轻质量; 在考虑安全的前提下,使用密度很低的灌封胶,解决模组层级的传热问题。模组其他部件中,如汇流排由铜替换为铝进行降重,并且可以进行挖孔设计,既减轻了质量,也起到了保险作用。LIU 等研究了如何设计18650 电芯的优化排布来提升空间利用率及耐冲击性能。
电芯模组的尺寸可以由车企高度定制化,减少模组的数量可以大幅降低模组壳体及其他附件质量,如Model3 的电池Pack仅采用4个模组。目前越来越多的车企采用VDA标准模组,可以降低成本、提高电池匹配的灵活性。对于模组轻量化而言,各电池厂商统一标准的模组更利于后续轻量化材料、工艺的大规模推广。
4、 电池箱体轻量化研究及发展
电池箱体是电动汽车高度定制化的零部件,也是电池Pack中除电芯外质量重的组件,有 T 字形、土字形、方形等。不同形状、尺寸的箱体一般均放置在汽车地板下方的安装支架上。电池箱体分为上盖和下箱体两部分,两部分用螺栓或者其他连接方式连接,中间被密封胶垫隔开达到 IP67 防水。
4. 1 电池箱上盖轻量化
电池箱上盖位于电池Pack上方,不承受侧面及底面的冲击,也不支撑整个电池组的质量,仅仅起密封作用。将电池模组密封于整个Pack箱体中,达到IP67或其他标准的密封效果。
电池箱上盖前期采用冲压钢板,如Nissan Leaf、BMW I3、Tesla Model3均采用 0.8 mm厚度冲压钢板。也可采用深冲铝合金板进行轻量化开发,较钢板有明显减重,使用厚度 1.5~2.0mm 铝合金上盖替代冲压钢板 可以降重20%~30%,但上盖铝合金在冲压性能上受到极大限制。若下箱体有足够的强度和刚性,上盖可以采用轻质增强塑料替代金属的方法进行轻量化,可采用 PP和PA为基材增强塑料。电池箱体上盖使用塑料制品的缺点是其电磁适用性以及低熔点会造成较大的安全隐患。PA 比 PP 的吸湿性更强,其成本也高于PP,故选择厚度3mm的PP玻纤增强复合材料来代替1mm厚的冲压钢板,降重可以达到50%。全铝车身的奇瑞小蚂蚁eq1电池箱上盖也采用了PP+LGF材料来进行进一步的减重。
电池箱上盖虽然为非主要承力部件,但箱体上盖也可以发挥辅助提升箱体强度的作用。基于此,上盖可采用碳纤维加强箱体强度以及进一步减重。通过研究1.5 mm厚铝板 ( 方案一) 、1. 5mm 厚碳纤维加强筋结构 ( 方案二) 及 0.5mm 厚碳纤维+3mm 厚铝蜂板+0.5mm 厚碳纤维 ( 方案三) 3 种结构方案,选定第三种方案,它较铝合金可以减重31%。LIU等采用 RBDO 方法对电池箱碳纤维上盖进行了模拟研究,其结果表明 CFRP上盖相较3mm 厚 Carbon-SMC 材料的 6.324kg 上盖再次降重到4.924 kg,降重比例达到22.14%。
由于碳纤维成本较高,以及PP、PA 基材复合材料的强度也偏低,目前绝大部分塑料上盖采用 SMC 复合材料模压而成。SMC 密度1.75~1. 5 g / cm3,厚度一般为2.5 mm。它较冲压钢板可以减重20%~30%,较铝合金上盖而言,虽并没有明显的减重效果,但是 SMC模压工艺可以制造深度非常大的上盖,可大大减小下箱体的高度,降低下箱体的质量,间接降低了整个箱体的质量。因此单双层模组排布的箱体以及单层模组排布的箱体越来越多地采用模压SMC制造箱体上盖,上盖高度可以与下箱体高度达到较大的比例。部分车型电池箱上盖材料及质量见表 3。
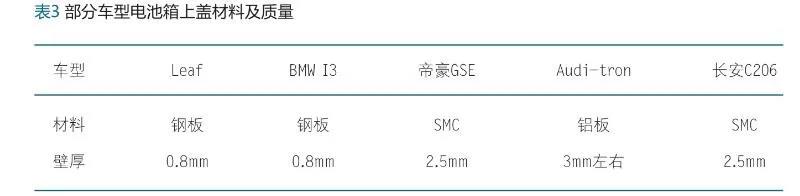
作者对吉利某车型电池箱体上盖的初步拟定同一结构的不同材料进行成型后质量的计算及对比,见表4。
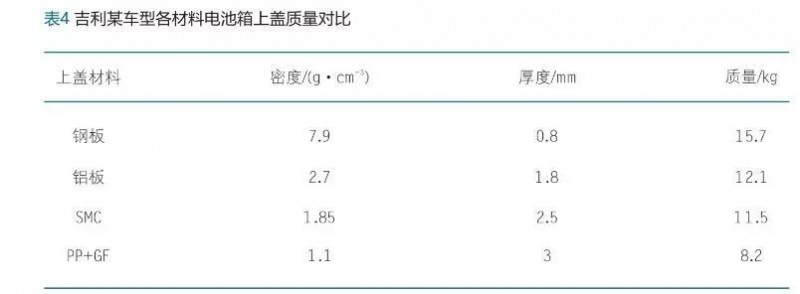
铝板上盖较钢板减重23%,SMC上盖较铝板减重5%,PP +GF上盖较铝板减重32%,长安C206车型模压SMC上盖见图 3。
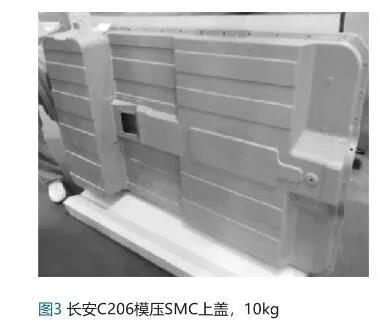
4. 2 电池箱下箱体轻量化
电池箱下箱体承担着整个电池组的质量以及自身的质量,并且抵挡外部的冲击,保护电池模组及电芯,是电动汽车重要的安全结构件。电池下箱体材料一般为钢、铝、增强塑料。采用冲压、焊接工艺成型的钢制电池下箱体,能够提供非常好的强度及刚性,成本也较低,但是质量较大,早期电动汽车如 Nissan Leaf、Volt 采用钢制电池箱体。但低成本、质量大的钢制电池箱体大大制约了电池 Pack 的能量密度,影响电动汽车的续航,故传统钢制电池下箱体技术路线已经基本被抛弃。
冲压铝板下箱体较钢板下箱体能明显降重,但是由于其拉延深度以及震动、冲击强度不足等问题,需要能力较强的车企结合车身、底盘进行集成设计来达到轻量化的目的,如 TeslaModel 3。
铝压铸电池下箱体相较于钢制电池下箱体有较多的优势,能够灵活地设计其形状和壁厚,能集成电池箱体侧壁吊耳、冷却通道以及其他部件整体压铸成型。但是压铸电池箱体尺寸偏小,从而限制了其在大型电动车上的使用。它更多地用 于PHEV 车型, 如大众 Golf GTE插电混动压铸电池箱、Audie-tron和 BMW X5 插电混动电池箱,如图 4 所示。
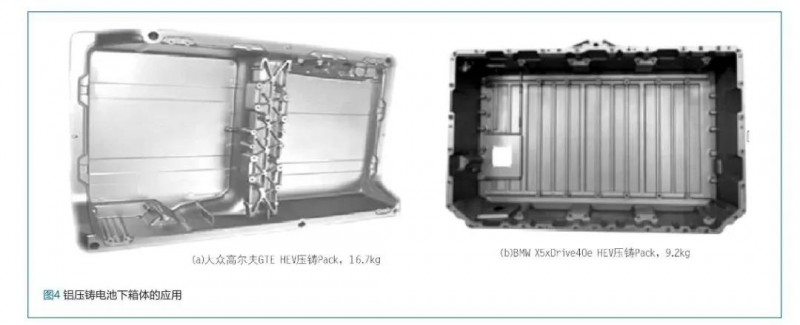
随着消费者对续航的要求越来越高,电池电量需求也越来越大,电池箱体的尺寸也相应地变得更大。目前车企普遍使用铝挤出型材、采用搅拌摩擦焊工艺成型下箱体底板,并与 4 块侧板焊接成型为下箱体总成,如图 5 所示。优点是较钢制电池箱体能减重30%以上,相较铝压铸电池箱体而言能成型尺寸更大的电池箱体,适应较大的车型。铝型材成本较低,能提供较大的强度及刚性,制约铝型材电池箱体大技术难点是连接技术以及尺寸控制问题。目前主流铝型材采用普通6063或6016,拉伸强度基本在220~240MPa之间。可以采用强度更高的挤出铝型材,如Constellium 的HSA6、AA66**( 性能超过AA6611)等材料,拉伸强度可达到 400MPa 以上,较普通铝型材下箱体能再减重20%~30%。
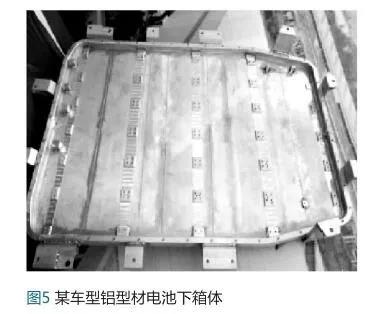
CHEN 等研究了通过对电池下箱体选材来进行轻量化开发,计算了铝、钢、钛板材下箱体的材料指数,以及相同刚性、稳定性下不同材料厚度。并模拟计算得出采用铝合金板材下箱体在不减小刚度的情况下,替代钢材能减重40%。
电芯的能量密度目前存在技术瓶颈,提高电池 Pack 的能量密度只能继续减小非电芯部件的质量,电池箱体减重当其冲。越来越多的机构正在研究塑料电池下箱体,汪佳龙等用碳纤维/环氧树脂复合材料替代Q235下箱体,通过有限元模拟、分析、计算后,碳纤维/环氧树脂复合材料在不减小强度的情况下,可以减重64%。
ZHAO 等采用碳纤维T300增强型树脂5208 对金属电池箱体进行材料替换并优化结构,模拟分析,它满足电池箱体相关强度性能,铝电池箱体质量的41.2kg 降至复合材料箱体的23.8 kg,减重达到42%。
BAUMEISTER等采用新型创新材料———泡沫铝复合三明治材料进行电池箱下箱体的开发,5mm 厚的三明治板满足耐热、静态力学等试验,采用该材料制作能转载20k W·h 电量的电池下箱体,较当前水平能减重10%~15%。
现代汽车公司 C H CHOI 等为了进一步降低金属电池Pack 下箱体的质量,联合开发了增强塑料下箱体。它以 PA6为基材,受制于碳纤维高昂的成本,该研究同时混入碳纤维和玻璃纤维,并不断变化 2 种纤维的含量,但总含量比例不低于40%,在满足疲劳强度、冲击、强度等性能下终得出优材料组分,质量由冲压钢材下箱体的35kg减少到24kg,降重达到 31%。
5 、电池 Pack 热管理系统轻量化
电池在充放电以及正常运行时均会放出热量,同时锂离子电池在低温时使用会对其造成不可逆的损害。基于以上两点,电池Pack需要配备热管理系统对电池进行散热和升温。早期电动汽车采用空气为热传递介质,如 Nissan Leaf 采用自然冷却方式,无电机、冷却液等,大大降低了电池 Pack 质量。但目前电动汽车随着电池能量密度、续航以及充放电速度的大幅提升,空冷已经完全不能满足安全需求,基本均需要采用液冷热管理系统。
液冷热管理系统包含冷却介质、压缩机、冷凝器、水冷板等,其中水冷板面积大、质量大,需要轻量化开发。目前大部分为口琴管式水冷板,铝挤出成型,壁厚约2mm 以上; 新型吹塑水冷板为铝吹塑成型,壁厚可较挤出口琴板减小一半,可降重 50%。
水冷板与电池Pack壳体集成一体化也是较明显的轻量化措施,取消了大面积的模组外水冷板,将其集成到电池Pack箱体下板中,如将冷却通道集成到箱体下板铝型材断面结构中。箱体内模组的冷却回路可以通过CFD流体模拟等措施进行优化设计,在能够达到满足要求的热交换情况下,大幅度减小回路长度,也能降低回路内冷却介质的质量,达到轻量化。
6、 电池 Pack 设计轻量化及电池 Pack 与底盘集成开发
6. 1 电池 Pack 轻量化设计
在传统材料及结构下,各家车企对其电池Pack不断地进行轻量化开发,部分主流车企的电池Pack质量及系统能量密度如图 6 所示。可见电池系统能量密度高的是特斯拉Model 3,其能量密度达到了168W·h/kg,但电池 Pack 系统成组率也为60%~ 65% 之间; Jaguar I-Pace 系统能量密度为147 W · h / kg,系统成组率也仅为56%。如此低的系统成组率让再次降低非电芯部件质量、大幅提升电池Pack 轻量化水平有了理论的实现空间。
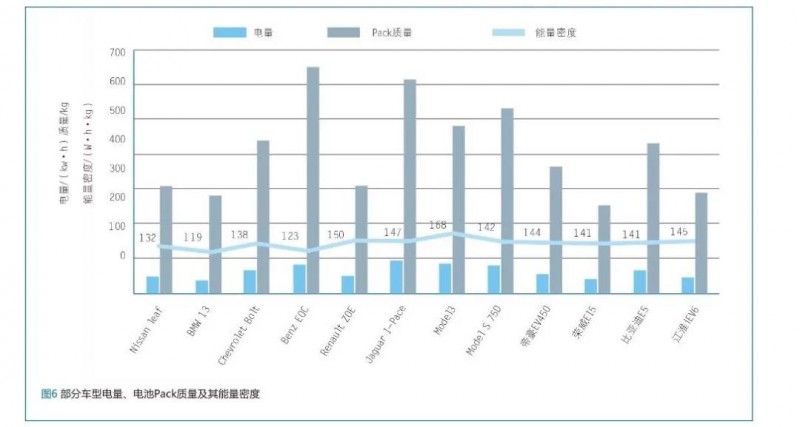
电池Pack采用铝合金等轻质的材料后,要想进一步对电池Pack 进行轻量化开发,则必须配合优秀的轻量化设计方案。电池 Pack 的轻量化设计大体符合轻量化设计开发的原则,即薄壁化、中空化、尺寸优化、拓扑优化、集成模块化设计等。
板材的薄壁化可以配合加强筋来满足强度要求,型材的薄壁化可以配合特定优化的断面来满足强度要求; 集成化设计在挤出铝型材电池包中可以将冷却板集成在箱体下型材板中,电池Pack 吊耳也可以由侧壁型材一次挤出成型。
TORNOW 等研究了电池Pack 如何以轻量化原则优先并综合乘客空间及批量生产进行优化设计及排布设计方法。SHUI等采用 4 阶段方法优化模拟电池 Pack侧壁厚度 ( EW) 、底部厚度 ( EB) 以及模组侧壁及底板厚度,在满足变形测试的情况下,较标准设计减重了11.61%,从18kg降低至15.9kg。
6. 2 底盘及电池 Pack 集成设计轻量化开发
当今的电池 Pack 只用于存贮、保护电芯及相关附件,为电动汽车提供电能。它不承受任何的车身载荷或吸收相应的碰撞能量,悬挂于汽车底盘下方。庞大的电池Pack与底盘形成了高度位置重合区域,也是电动车较传统汽车重的主要原因。因此急需对电动汽车的底盘和电池 Pack 结构进行集成优化。底盘与电池Pack的同步设计对电动汽车的轻量化开发有重要作用。如宾夕法尼亚大学的 MA 等将Tesla Model S85 的电芯模组采用全新Power Panel 三明治蜂巢结构设计,并且将电池Pack的两根底盘安装纵梁以及电池下箱体的加 强 横 梁 均 采 用Power Panel结构替换原有结构,在没有降低弯曲刚性和扭转刚性的情况下,Model S85 的底盘和电池 Pack实现了整车350kg的减重。
BMW非承载式车身结构的I3电动车,底盘承担了车身结构强度及保护电池Pack的作用,这大幅降低了电池Pack箱体的载荷,使I3 电池Pack箱体的底板和侧壁均采用铝板替代铝型材拼焊而成,大幅降低Pack壳体的质量。I3虽然并没有取消电池Pack壳体,但是也引领了越来越多的机构对底盘电池Pack进行了研究。
Tesla Model3 电池Pack提供了一个新的轻量化设计思路,其电池Pack做到了极致减重,没有采用铝型材,直接采用3. 2mm 铝板冲压后成型为2150mm×1450mm×103mm 形状的浅托盘,并且托盘四周没有其他侧壁模块,采用0.8 mm 冲压钢板作为上盖,直接与下托盘螺接、点焊为整个电池箱体。使装有80.5 kW·h 的电池Pack仅重478kg,相较于85kW·h 的Model S 85D 的电池Pack减重了15%,另外相 较于80 kW · h奔驰 EQC电池Pack 的650 kg,以及95k W·h 的奥迪 e-tron 的715kg 都有大幅减重。Model 3之所以 能够如此大胆地减重电池Pack,大幅缩减电池Pack的防撞击边框,是因为其优化了车身的防撞设计,使对电池Pack的碰撞冲击传导至车身高强度热成型钢结构件上,如图 7 所示。

CATL ( 宁德时代) 在其新的公司技术路线规划中指出,在电芯能量密度没有突破性进展的情况下,电池Pack的能量密度在 2022—2023 年要达到230~265 W·h/kg,需要与整车厂配合开发底盘与电池Pack高度集成的新电池结构部件。
ARPA ( 美国能源局) 联合Stanford大学进行了电池底盘的研究项目,使该部件 ( 电池底盘) 能作为汽车的结构件,电池与底盘集成为一体。电池底盘新部件的研发成功将电动汽车整车质量降低 40%以上,取消了传统的电池箱体,并优化了底盘及相关部件的结构。
WANG 等设计并模拟及试验验证了一种新型蝴蝶型结构多功能电池Module,具备相当高的强度,能替代车体底部部分结构件吸收汽车冲击及碰撞能量。该结构使其取消了电池Pack壳体,大大降低了动力电池系统的质量。电池Pack 与底盘集成一体化并且可灵活延伸其结构用于更改携带电量的电池底盘也在研究中,STURIN 等提出都市模块化车型 ( Urban Modular Vehicle,UMV) 概念,关注电动汽车创新车体结构设计的发展,将下车身结构分为可延伸的底板( 集成电池箱体) 和可替换的前后防碰撞模块3 部分,如图8所示。
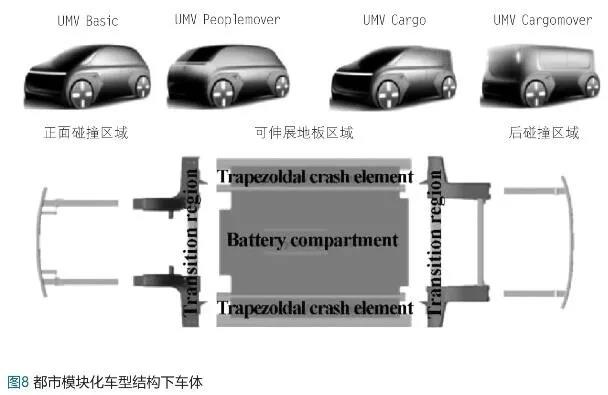
在 UMV 结构车体中,可以任意延伸电池底盘的长度,以及替换前后防撞模块,打造不同尺寸的微型车、A 级车,货车等。该下车身模块需要电池Pack与底盘的高度集成才能实现灵活改变车身尺寸及携带电量。该结构使电池Pack与底盘高度集成设计,轻量化效果显著。
7、 结论
电池Pack轻量化对新能源汽车整车轻量化有着重要作用,可以通过不断降低非储能部件的质量来实现。对于壳体包装部件而言,需要进一步减薄壳体厚度,以及加大研究高强塑料进行以塑代钢、铝的轻量化开发策略等; 对于电芯模组层级,不仅仅需要降低模组壳体质量,更需要对电芯模组进行设计优化排布,加大空间利用率。电池Pack箱体是除电芯之外重的部件,在普遍采用铝合金下箱体和增强塑料上盖的情况下,需要不断对其结构进行优化设计,降低壁厚并辅助以加强筋结构,减小下箱体高度,以及减小电池Pack整包高度。加强对塑料下箱体的开发研究,能大幅降低箱体质量。
BMW I3 及 Tesla Model3 电池Pack结构的出现,让人们对电池Pack与底盘进一步高度集成模块化设计开发有了更多的研究。未来电池底盘一体化结构能使电池Pack不再是仅仅只有存储和保护电芯模组的作用,而是作为整车的结构件,提高整车的弯曲强度和扭转刚度。电池底盘能大幅减少电池Pack箱体的部件,后期将彻底取消电池Pack箱体,电芯模组直接存贮于电池底盘中,这将大大降低电动车动力电池系统的质量,对其轻量化有重要意义。
本文作者:浙江吉智新能源汽车科技有限公司
李日步、王海林、吴东升、吴天男、高文龙、周瑞华