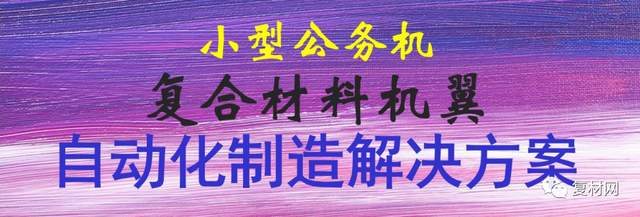
商业航空行业高度关注高效高速率制造的设计方案,但仍需要自动化、符合低速率制造结构。
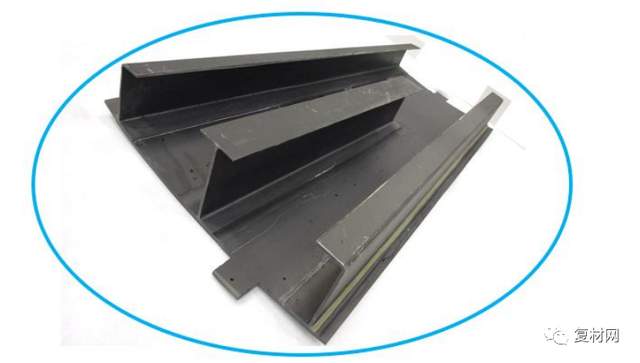
OPTICOMS“清洁天空 2”项目正在寻求一种设计、材料和制造解决方案,以实现低成本、自动化的复合材料翼盒制造,用于低速率飞机生产。该项目由以色列航空航天工业公司牵头,采用“工作-working”蒙皮的三翼梁设计。
用于商用飞机的复合材料航空结构的制造跨越了50多年的历史,并在21世纪初为波音787和空客A350开发的机身、机翼、尾翼、发动机等大型部件稳步发展。
这一发展的绝大多数取决于热压罐固化碳纤维/环氧树脂预浸料的使用,最初是手工铺设,然后最终通过自动铺丝、自动铺带和其他基于机器的工艺铺设。
这些材料和工艺技术适用于宽体787和A350,在疫情前,它们的制造速度为每月10-15架。然而,随着波音公司和空中客车公司展望未来,并考虑在单通道飞机的主要结构中应用复合材料,预计单通道飞机每月的建造速度为60-100,设计和M&P将有利于高速率、非热压罐、高度自动化的工艺。这些工艺包括树脂传递模塑、压缩模塑和液体树脂注入等。
但是,即使高速率制造业将主导商业航空航天领域,用于低速率飞机的复合材料航空结构的制造——包括支线飞机和公务机项目——不仅将持续下去,而且可以而且应该受益于高速率项目中部署的一些相同的成本、设计和M&P创新。
正是考虑到这一切,欧洲“清洁天空 2”号计划推出了OPTICOMS -小型飞机的优化复合材料结构。
OPTICOMS是一个由航空航天制造商以色列航空航天工业公司(IAI,Lod,Israel)领导的财团,其合作伙伴提供创新自动化技术、材料、软件、工具和机械。OPTICOMS的目标是评估低速率生产翼盒设计,该设计具有自动化制造、集成结构、非热压罐固化、大型结构粘接、创新制造和组装工具、牢固连接的结构健康监测和虚拟测试等特点。
IAI航空集团研发总监兼OPTICOMS公司经理Arnold Nathan表示,“每当我们试图将复合材料制造纳入自动化讨论时,我们经常听到客户说,“自动化很好,但只有当你有大量生产时才用的上。” OPTICOMS 系统的设立是为了在没有大批量生产的情况下,找出自动化是否合理。复合材料制造自动化能否在低产量的情况下具有竞争力和成本效益?”
机翼设计
OPTICOMS诞生于意大利公务机制造商Piaggio Aerospace(热那亚)提出的“清洁天空 2”请求,该请求旨在为其P180Avanti 九座公务双涡轮螺旋桨飞机开发全复合材料替代机翼。翼盒长6.8米,根部宽0.71米,顶端宽0.28米。Nathan说,Piaggio急于评估全金属传统翼盒的替代品——一种尺寸相同但重量减轻(20%)的替代品。此外,与传统的复合材料翼盒制造相比,成本应降低20-30%。IAI 及其合作伙伴赢得了合同,并于2016年开始与Piaggio合作。
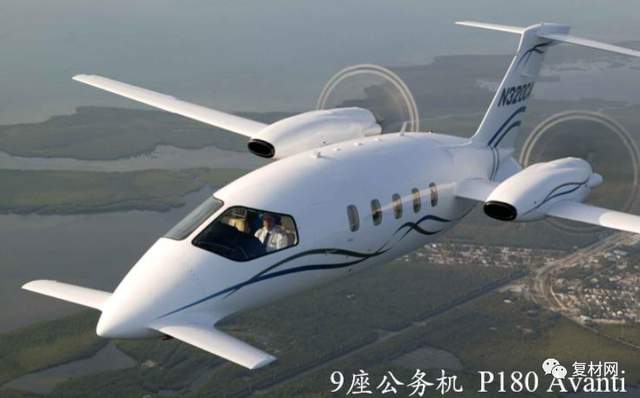
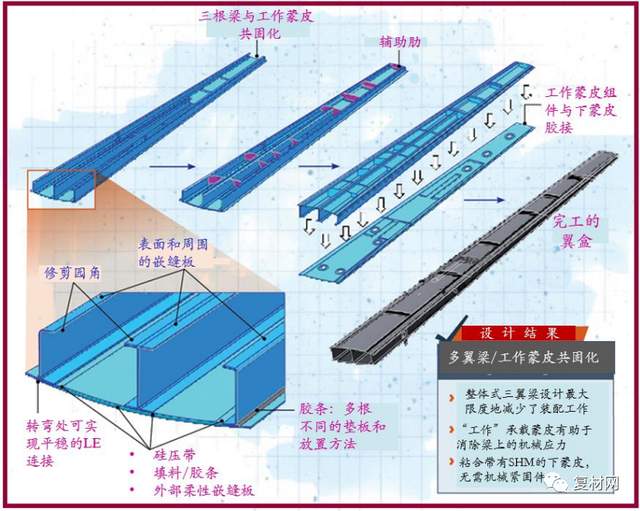
OPTICOMS 是一个由多部分组成的项目,旨在执行一系列高度详细和精心进行的权衡研究,以评估和确定最佳机翼设计、材料组合和非热压罐制造工艺,从而实现低体积全复合材料翼盒的自动化制造。
Nathan 说,IAI和OPTICOMS 很早就决定专注于并评估由三个合作伙伴提供的三种制造工艺的使用:
- 由Techni Modul Engineering(TME,Coudes,France)提供的干燥和预浸织物的自动机器人拾取和放置;
- 干丝束和预浸丝束的自动铺丝(AFP),由科里奥利复合材料公司(法国奎文)提供;
- 以及由 Danobat提供的自动干材料铺放技术。这些技术和合作伙伴的选择对于指导 IAI 进行多变体贸易研究至关重要。
设计成果
整体式多翼梁(三翼梁)设计最大限度地减少了装配工作。承载蒙皮有助于消除梁上的机械应力。SHM粘合下表皮,无需机械紧固件。
这项权衡研究的第一步是设计评估。这项工作是由先进技术的结构设计工程师Adam Sawday在IAI领导的。Sawday说,他和IAI对机翼的设计采取了一种干净的方法,研究了各种架构中的18个以上的概念。设计很快就分为两类。第一种采用“工作”蒙皮,其中翼盒蒙皮成为承载结构。第二种采用非工作蒙皮,带有加载的翼梁凸缘。在这些类别中,设计包括带肋、桁条和两个翼梁的传统概念,或者,使用三个翼梁(称为多翼梁),没有肋或桁条。一些概念还考虑了使用夹层板结构,以产生半工作蒙皮。
Sawday说:“我们的口号是减少制造工作量和组装工作量。”。“我们相信,如果你能开发出一种更高效、更完整的结构,那么你就会得到一种更便宜、更轻的结构。”
Sawday说,这些设计是根据一系列指标进行衡量的,以评估它们满足项目成本和重量目标的能力。这些指标包括:材料成本、设计复杂性、部件制造成本、装配成本、无损检测成本、工具和跳汰成本、重量、强度、技术准备水平、生态因素、风险状况、稳健性和可靠性。
其中,权重最大的标准是重量、制造和组装成本、设计复杂性、TRL和风险状况。
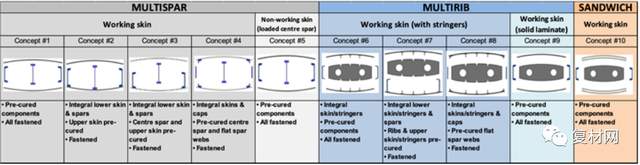
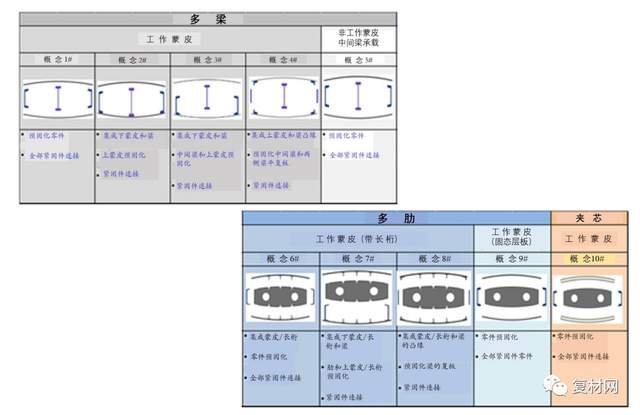
OPTICOMS向下选择的过程使其获得了10个翼盒的设计决赛,每个翼盒都采用了不同的结构和组装特征。选择过程寻求尽可能高效和具有成本效益的组装设计。
向下选择到最终设计
这次评估的数据帮助IAI将设计概念筛选到10个入围者。四个是多翼梁/工作蒙皮,一个是带载荷翼梁的多翼梁-非工作蒙皮,四个是带桁条的多肋/工作蒙皮、一个是没有桁条的多肋/工作表皮,以及一个是无桁条的夹层结构/工作蒙皮。每种设计都提供了预固化、共固化、粘合或机械紧固的各种组合。
最终设计涉及到另一轮权衡研究,使用了与第一次研究相同的许多标准。每个设计都会根据其符合标准的程度给出一个权衡价值。Sawday 说:“我们有一个很大的权衡表,每个设计选项都有价值,这有助于我们看到最强的选项。”
Sawday指出,有一种设计从一开始就在权衡研究中表现良好,似乎很可能名列前茅。确实如此。内部称为多翼梁/工作蒙皮#2,具有高度集成和共同固化的上部蒙皮和三个翼梁。然后将其粘合到具有检修面板的下表皮上。一系列“备用”肋选择性地位于翼梁之间,用于支撑承受大部分弯曲载荷的蒙皮。
“我们开发的最有利的结构,”Sawday说,“是那些具有多翼梁的翼梁,蒙皮可以承受载荷。然后,翼梁的结构会变得越来越简单,也不会像传统的复合材料机翼设计那样重。我们认为,如果我们能让这些翼梁变得非常简单,横截面不变,那将省去很多麻烦和废料。”
Sawday表示,粘结一体式多翼梁/工作蒙皮设计因其降低的组装成本、低重量、易于自动化和整体低零件数量而显示出特别的前景。然而,问题仍然存在:哪些材料和哪些制造工艺最适合将这种设计付诸实践?
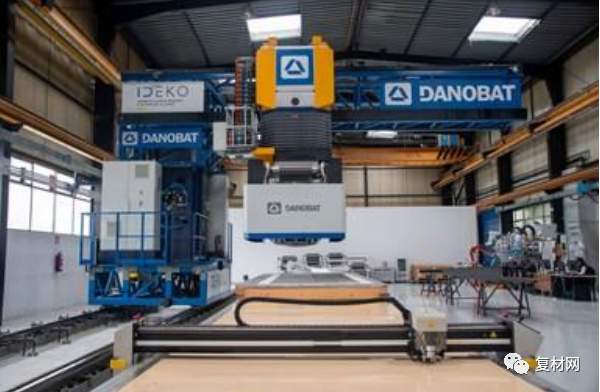
Danobat的自动干燥材料放置系统旨在快速放置大量干燥纤维。尽管该技术最初是为风力涡轮机叶片制造而开发的,但 OPTICOMS正在评估其对航空航天制造的适用性
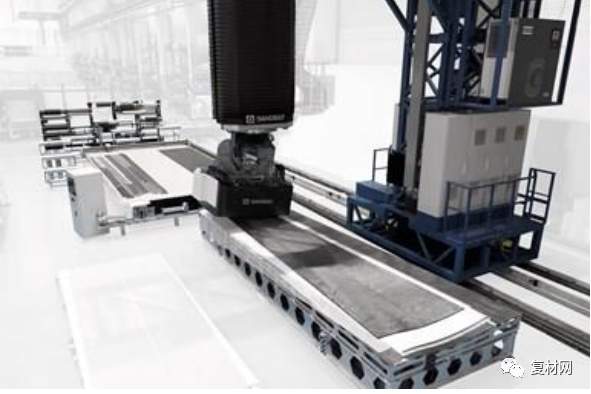
Danobat ADMP系统
M&P权衡分析;
首先是材料权衡研究。这些都是由复合材料工程师Yaniv Yurovitch在IAI进的。他说,OPTICOMS根据Piaggio、IAI和技术合作伙伴的建议,开始评估。
非热压罐碳纤维预浸料、干碳纤维(胶带和织物)和树脂。结果是列出了35种合格材料和新材料。
然后,根据OPTICOMS系统项目最关键的参数对第一组材料进行筛选:成本、玻璃化转变温度(Tg)、粘度(用于输液或注射)以及是否适用于自动叠层技术。这次评估将材料清单从35个预浸料、干纤维和树脂减少到20 个。
订购了这20种材料中每种材料的样品;Yurovitch随后制作了试样,并进行了机械测试,作为下一次向下选择的一部分。“这是一个非常大的一揽子工作,”Yurovitch说。“这使我们能够做出更多的决定,并选择最后三种材料。”这些纤维/树脂组合是:
- Toray Composites Materials America(美国华盛顿州塔科马市)2510 碳纤维/环氧树脂预浸料。
- Hexcel(美国康涅狄格州斯坦福德)的HiTape 碳纤维UD 胶带,与 Hexcel 的HexFlow RTM6 环氧树脂一起使用。
- SAERTEX(德国 Saerbeck)提供的碳纤维无卷曲织物(NCF-non-crimp fabric),通过注入索尔维复合材料公司(美国佐治亚州 Alparetta)的 PRISM EP2400 增韧环氧树脂进行组合。
这份清单显然倾向于使用干纤维,而干纤维反过来又倾向于将浸泡作为制造过程。Nathan说,这在一定程度上是由于在低产量环境中管理预浸料保质期的挑战。“当你低调说批量生产,你真的不想带很多预浸料,担心保质期,”他说。“干纤维没有这个问题。”
这三种材料还与一种或多种为OPTICOMS选择的制造工艺配对:Toray预浸料与拾取和放置和AFP匹配,Hexcel的HiTape/RT6与AFP匹配以及拾取和放置,SAERTEX NCF与拾取和放或ADMP匹配。
OPTICOMS 翼盒叠层
OPTICOMS正在评估预浸料和干纤维的热压罐外制造。干纤维的放置将使用Danobat ADMP系统或Coriolis AFP系统进行。对于翼盒设计中的备用肋,预计将使用TME的机器人拾取和放置系统。
围绕自动化制造工艺的权衡分析——最适合哪种类型的零件——仍由IAI 和OPTICOMS进行。然而,Nathan说,初步结果无疑为技术指明了方向。例如,Danobat 的ADMP技术,最初是为在风力涡轮机叶片制造中快速放置宽织物而开发的,在OPTICOMS方面也同样有效。该技术在OPTICOMS系统中已经成熟,其牢固性和可靠性也有所提高,但与AFP相比,它仍然是一种不太成熟的航空航天铺放技术。
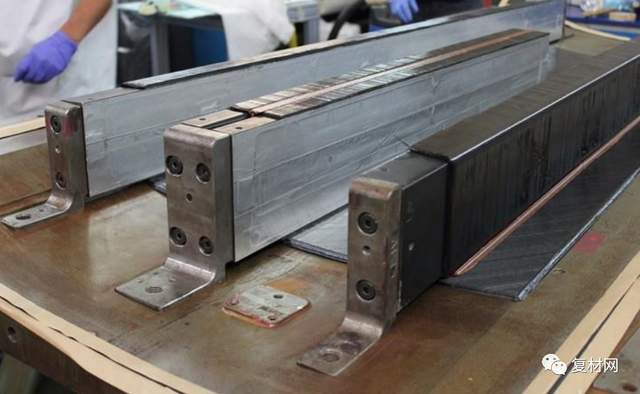
OPITOMS正在评估预浸料和干纤维的热压罐外制造。干纤维的放置将使用Danobat ADMP 系统或 Coriolis AFP系统进行。对于翼盒设计中的备用肋,预计将使用TME的机器人拾取和放置系统。
围绕自动化制造工艺的权衡分析——最适合哪种类型的零件——仍由IAI和OPTICOMS进行。然而,Nathan 说,初步结果无疑为技术指明了方向。例如,Danobat的ADMP技术,最初是为在风力涡轮机叶片制造中快速放置宽织物而开发的,在光学方面也同样有效。该技术在光学系统中已经成熟,其牢固性和可靠性也有所提高,但与AFP相比,它仍然是一种不太成熟的航空航天铺放技术。
相反,具有科里奥利系统的AFP凭借其丰富的航空航天经验,是一种成熟而准确的技术,但与ADMP 相比,其上篮时间更长,并且需要相对频繁的检查来检查异常情况。Nathan说,科里奥利在整个光学系统项目中取得了显著进展,开发了在线、实时的上篮检查,以应对这一挑战。最后,TME 的拾取和放置技术旨在自动将切割织物从切割台转移到模具,似乎对较小的离散零件最有效,如多翼梁/工作蒙皮设计中的支撑肋。
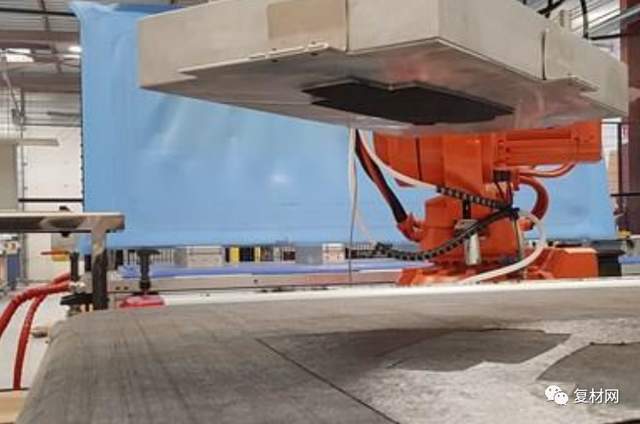
Techni Modul Engineering(TME)为OPTICOMS项目开发的拾取和放置系统已被证明最适合制造为多翼梁翼盒设计的支撑肋。在这里,TME系统正在从切割台上拾取一个帘布层,并在下图中准备将其放置在模具上。正在对光学系统的制造工艺进行向下选择。该项目也在评估自动纤维铺设(AFP)和自动干材料铺设(ADMP)的性能
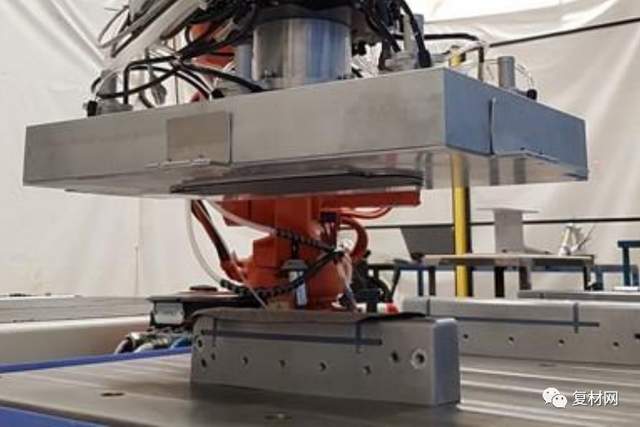
TME 系统在模具上放置一个帘布层
接下来的步骤
Nathan表示,尽管仍有几个月的工作要做,以评估制造工艺和组装解决方案,但 OPTIOMS 有望实现该项目提出的自动化、成本和重量节约目标。
“这是关于 OPTIOMS的一个重要观点,”他解释道。“我们对设计进行了严格的向下选择。我们对材料进行了向下选择。对工艺进行了向下的选择。所有这些都需要时间和精力。这是该项目的独特之处之一。”
OPTIOMS 发起了三次技术和硬件征求建议书
(CFP),以支持、确保和提高项目目标。成功的提案成为了“清洁天空 2”项目,与OPTIOMS “母亲”核心合作伙伴相关并作为其补充,所有这些项目都朝着共同的目标共同努力。
这项开发的第一项工作是 FITCoW,旨在开发一种新型的集成碳纤维工具系统,用于工作蒙皮和三根梁的共同固化。FITCoW 的目标清单雄心勃勃:制造零件成本降低 50%,工具成本降低30%(与金属替代品相比),与热压罐和非热压罐替代品相比制造时间减少20%,与因瓦工具相比CTE 失配减少40%,由于具有更好的尺寸控制能力,加热和冷却时间减少了20%,检查时间减少了40%。
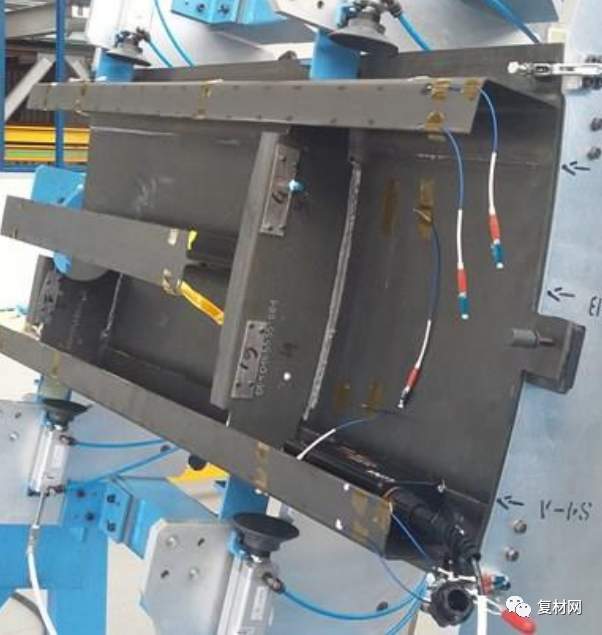
光学机翼箱上部结构包括共固化翼梁和工作机翼蒙皮。然后,通过光学系统附带的“清洁天空 2”项目开发的组装技术,将其粘合到下机翼蒙皮上。此处显示的是WIBOND装配夹具中的翼梁/蒙皮结构。注意集成到接合线中的传感器,以检查接合的完整性。
为了将翼梁/蒙皮结构粘合到下蒙皮,第二次CFP产生了另一个名为WIBOND的OPTIOMS项目,以开发一种粘合组装工具,该工具可以放置粘合剂,施加适当的压力,并在粘合线中加入光纤传感器,用于粘合的结构健康监测。
启动第三个CFP是为了应对残余应力这一关键挑战,残余应力会导致翼梁/蒙皮结构“回弹”。这些变形可能对粘合组装过程产生有害影响。ELADINE 项目加入了 OPTICOMS 的工作,开发软件,对整个结构的热各向异性、聚合收缩、工具部件相互作用、树脂流动和压实以及温度梯度进行建模和预测。
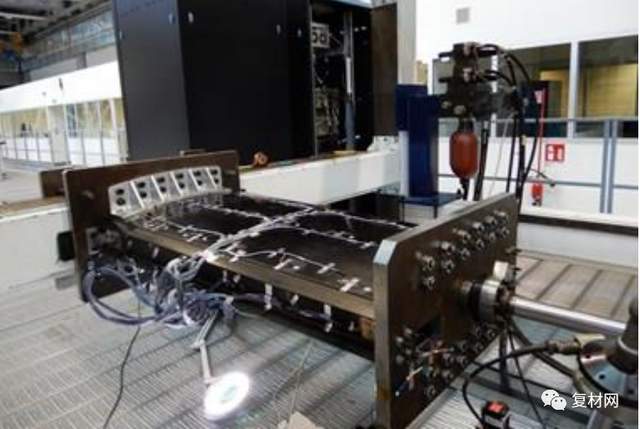
在Piaggio Aerospace的测试台上,完全组装好的OPTICOMS小型演示器。这架1.2 米长的演示机代表了全尺寸翼盒的中心,配备了结构健康监测系统,用于测量弯曲和压缩测试期间的粘合线性能。OPTICOMS 项目目前正在研制一个全尺寸的翼盒,Piaggio也将对其进行测试和评估。
IAI和OPTICOMS目前的主要重点是在2022年第二季度之前向Piaggio交付一个完整的6.8米演示机翼,用于静态和疲劳测试。随后将分析机翼的整体性能以及设计、材料和工艺满足项目标准的能力。接下来,Piaggio将提出下一步商业化的建议。
然而,除了Piaggio,国际航空公司希望OPTICOMS翼盒能在其他飞机上得到应用。“虽然这个项目是基于一种特定的飞机,”Sawday 说,“但我们试图使设计能够扩展到不同的厚度和尺寸。我们从未忽视这样一个事实,即这项技术可以而且应该具有高度的适应性。”