为满足材料轻量化、高性能、可设计等需求,研究者将延展性和成形性优异的金属基体与比强度高的增强体相结合制备金属基复合材料。碳纤维具有较好的力学性能和化学稳定性,是最值得关注的增强体之一。碳纤维增强金属基复合材料具有比强度高及耐蚀、耐热性好等特点,在军工、航空航天、高端装备制造等领域具有广阔的应用前景。
为解决碳纤维增强金属基复合材料界面结合强度差的难题,有人在探索采取碳纤维表面改性、金属基体合金化等措施来优化复合材料的界面特性。考虑到制备方法对复合材料的综合性能具有决定性作用,本文综述了碳纤维增强金属基复合材料的界面调控和制备方法的研究进展。此外,增材制造技术也是制备碳纤维增强金属基复合材料的新方法,笔者在总结增材制造技术在该领域应用的基础上,结合传统的平面流动铸造法,提出了制备金属基复合材料的流铸印刷新技术,并介绍了采用该方法制备碳纤维增强锡基复合材料的部分探索性试验结果。
1 碳纤维增强金属基复合材料的界面调控研究
现有研究中,Al、Mg、Ni、Cu、Ti等多种金属基体都被尝试用于碳纤维增强金属基复合材料的制备。复合材料的性能取决于金属基体、碳纤维增强体及两者界面的结合强度。界面结合强度直接影响其内部应力传递与分散,良好的界面结合是复合材料获得优良性能的先决条件。界面结合强度与金属基体与碳纤维的润湿性、两者界面间的化学反应密切相关,复合材料制备既要保证两者之间具有良好的润湿性,又要有效控制反应程度以形成稳定的界面。
1.1 碳纤维表面改性
碳纤维在金属基体中有利于应力的转移,提高复合结构的综合力学性能。然而,碳纤维表面能低、反应活性差,显著影响与金属基体之间的结合力。碳纤维与金属基体之间的结合力较差,导致层间剪切强度降低,复合结构中较易产生分层或脱粘。为提高碳纤维与金属基体之间的结合能,研究者通过碳纤维表面改性来提升粗糙度、增加碳纤维表面化学官能团的数量,以增强碳纤维与金属基体之间的化学键合力,将两者之间的机械结合转化为结合强度更高的冶金结合。常用的表面改性方法有碳纤维表面涂覆、表面氧化或等离子表面改性等。
Urea 等发现,在碳纤维表面涂覆 Cu 膜能改善其与 Al 基体的润湿性,并认为这是原有界面被由熔融 Al 和 Al2Cu 组成的低能量界面替代所致。张昊明等对碳纤维表面进行了化学气相沉积 Cr,并在随后的热压烧结过程中发现,大部分 Cr 与碳纤维表层的 C 反应形成了连续均匀的 Cr7C3 界面,少量 Cr 则扩散进入 Cu 基体,使碳纤维与铜之间的界面由弱机械结合转化为强冶金结合,进而改善复合材料的热稳定性。碳纤维体积分数为 40%~55%时,Cf/Cu 复合材料的致密度高于 97.5%,平面方向的热导率达到了 393~419 W/(m·K)。Zhong等采用表面镀 Ni 的碳纤维制备了 Cf/Al 复合材料,发现镀镍层能改变热膨胀系数,从而减少碳化物引起的应力集中,阻止裂纹直接扩展至纤维表面,有效延迟损伤的发生,如图 1所示。
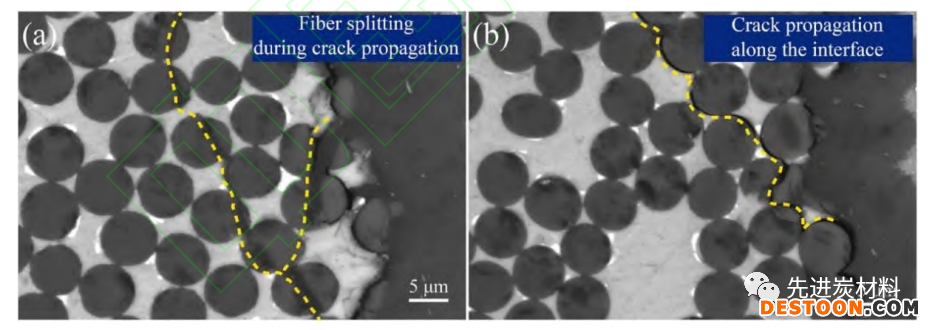
图1 Cf/Al复合材料(a)及Ni-Cf/Al复合材料(b)层间剪切裂纹的扩展路径
1.2 金属基体合金化
通过向金属基体中添加特定合金元素来改变基体的化学组成,减小基体的界面张力,使碳纤维与金属基体之间产生化合物界面层或扩散界面层,均能提高碳纤维与金属基体之间的界面结合强度。Zhang 等发现,在镁基体中加入稀土元素 Y,碳纤维与基体之间形成了清晰可见的界面层;含 3.2%(质量分数,下同)和 5.7%Y 的复合材料中形成了大量纳米尺度的粒状 Mg2Y 相,含 8.5%Y 的复合材料中还形成了 Mg24Y5 相。相比于 Cf/Mg 复合材料,Cf/Mg-5.7Y 复合材料的层间剪切强度从 46.3 MPa 提高到了 102.3 MPa,如图 2 所示。Zhang等发现,稀土元素 Gd 也能在镁基体界面附近富集并形成纳米级 Gd2O3 夹层界面及粒状Mg7Gd 相,Cf/Mg-3.2Gd 复合材料的纵向弯曲强度和层间抗剪切强度比 Cf/Mg 复合材料分别提高了 60.4%和 25.3%。
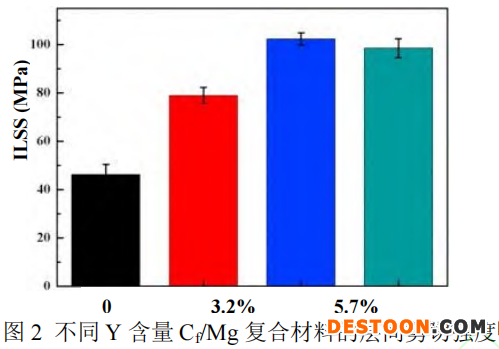
2 碳纤维增强金属基复合材料的制备方法
采用不同方法制备的金属基复合材料的界面结合方式和结合强度均有较大差异。常用的复合材料制备方法有固相法(粉末冶金、扩散粘结)和液相法(搅拌铸造、挤压铸造、真空压力浸渗)两大类,前者是固态金属与碳纤维扩散形成复合材料,后者是液态金属与碳纤维浸渗粘结,但高温金属熔体与碳纤维直接接触易发生强烈的界面反应。
2.1 粉末冶金法
粉末冶金法是首先将碳纤维与金属粉末机械混合,均匀分散后在模具中压制成型,随后在一定温度下烧结成复合材料。粉末冶金法的优点是能灵活调控增强相的种类和比例,实现零件的近终成形及规模化生产。但粉末冶金法仅适用于颗粒、晶须或短纤维,受烧结温度的限制,界面结合强度偏低。采用高温高压的热等静压法制备的产品致密度高、性能优异,但设备昂贵,多用于特需产品。
Silvain 等采用粉末冶金法制备了 Cf/Al 复合材料,碳纤维含量达 50%(体积分数)的Cf-Al 复合材料界面及碳纤维尖端处形成了大量 Al4C3 颗粒(图 3),这些碳化物(Al-C 化学键)有效改善了 Cf/Al 复合材料的热传导性能,其热导率为 258 W/(m·K),热膨胀系数降低到了 7×10−6 /K,基本能满足计算机组件对散热器材料的要求。任澍忻等采用粉末冶金法研究了碳纤维含量对铁铜基复合材料耐磨性的影响并发现,碳纤维质量分数为 2%的铁铜基复合材料组织均匀致密,致密度约为 92.6%,平均摩擦因数为 0.6,磨损失重最小;碳纤维质量分数为 6%的铁铜基复合材料孔隙较多。
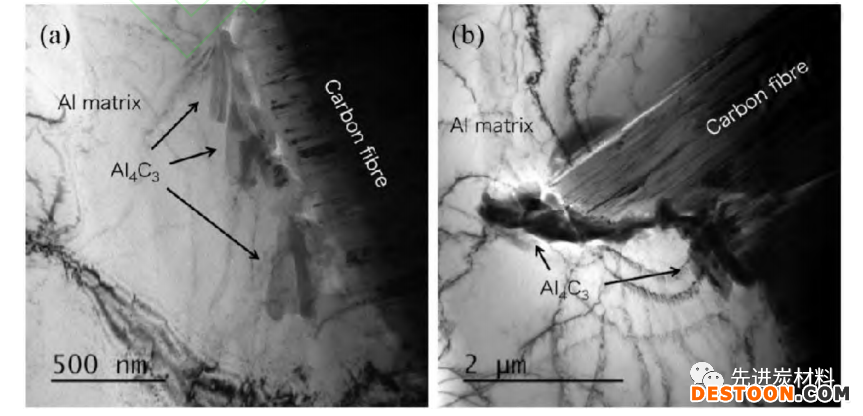
图3 含50%(体积分数)碳纤维的Cf/Al复合材料的Cf-Al界面(a)及碳纤维尖端(b)的透射电子显微图
2.2 扩散粘结法
扩散粘结法是将碳纤维预制体与片层状金属叠放并施加压力,通过长时间的扩散粘结制成复合材料。必须对金属表面进行净化处理,去除金属表面的氧化膜,有助于提高界面的结合强度。扩散粘结法通常在较低温度(主要相熔点的 50%~70%)进行,能减少有害界面反应的发生。但该方法的生产成本较高周期较长,还可能造成碳纤维损伤。
扩散粘结法的优点是工艺简单,产品的成形质量主要通过温度、压力和粘结时间控制。为获得良好的粘接界面,一般是控制压力使金属变形填补界面空隙,进而优化粘结时间,确保扩散能顺利进行。帅甜田等[38]发现,热压温度对 Cf/Al 复合材料的致密度有显著影响,在热压温度为 640 ℃、热压时间为 50 min、压力为 15 MPa 的条件下,Cf/Al 复合材料的致密度可达 98.5%,界面反应产物 Al4C3 质量分数约为 3.6%,碳纤维与铝基体结合良好。李小红等研究了压力、粘结温度、粘结时间等工艺参数对 Cf/Cu 复合材料致密度、强度及摩擦性能的影响并发现:施加 238~286 MPa 压力制备的 Cf/Cu 复合材料致密度较高;粘结温度高于750 ℃时干摩擦磨损量和湿摩擦的增重量基本不变;粘结时间增长,Cf/Cu 复合材料的致密度、强度和耐摩擦磨损性能更好。
2.3 搅拌铸造法
搅拌铸造法是采用机械或电磁搅拌装置混合碳纤维和液态金属,再采用铸造、模锻或挤压等方法制成复合材料。搅拌铸造法采用常规熔炼设备,工艺成本低、生产效率高。但由于搅拌过程中产生的压力差及碳纤维的持续加入,空气可能进入基体形成微孔缺陷。此外,搅拌铸造过程中金属熔体与碳纤维增强体长时间接触会发生强烈的界面反应
常海等采用搅拌铸造法制备了不同体积分数的 Cf/AZ91 复合材料,发现随着碳纤维体积分数的增加,Cf/AZ91 复合材料的气孔率增大;提高挤压比和变形温度有利于提升材料流动性,进而降低 Cf/AZ91 复合材料的气孔率。Rajesh 等采用搅拌铸造法制备了不同碳纤维含量的 Cf/Al7075 复合材料,发现当碳纤维的质量分数达到 3%时,复合材料的抗拉强度和硬度分别提高了 35%和 16%。Naji 等发现,随着碳纤维体积分数和长径比的增加,Cf/Al-8.5%Si-5%Mg 复合材料的断裂韧性增大,并认为断裂能量是基体变形(如剪切脱粘)和其他机制(如纤维被拉出、纤维断裂)共同消耗的,碳纤维能起屏障作用,导致复合材料的断裂能量增大,如图 4 所示。
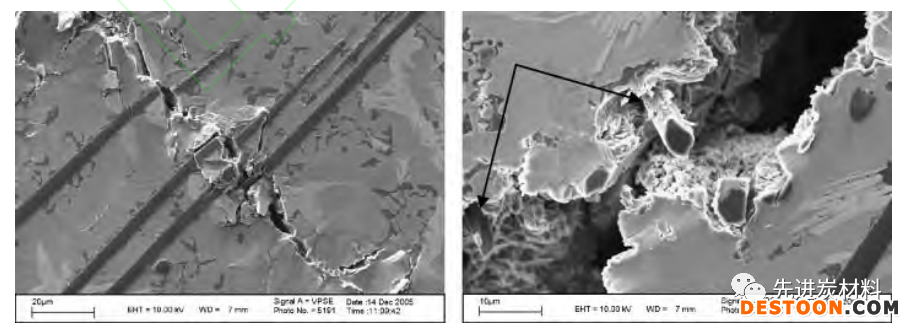
图4 Cf/Al复合材料中断裂纤维的扫描电子显微图
2.4 挤压铸造法
挤压铸造法是金属熔体在机械压力作用下快速成型凝固的方法。如图 5 所示,该工艺过程是将碳纤维制成预制体并置于模具中,然后将金属熔体浇注在模具中并施加数百 MPa级的机械压力,在高压下金属熔体与碳纤维预制体浸渗熔合随后快速凝固。挤压铸造工艺过程中碳纤维增强体与金属熔体的接触时间比搅拌铸造法的短,因此界面反应显著减少。施加高压能改善碳纤维增强体在熔融金属中的润湿性,提高界面的结合强度。然而,该方法成本较高,对碳纤维预制体的强度要求较高,实际生产中碳纤维预制体骨架不可避免会发生变形。
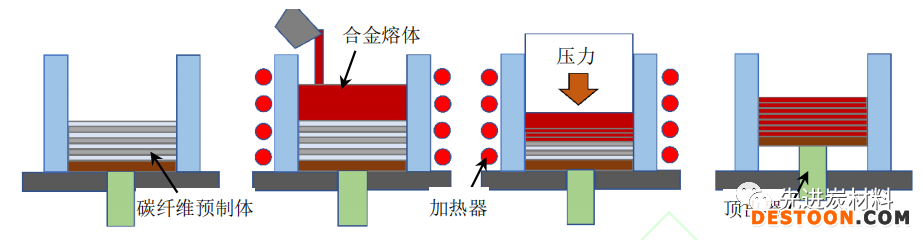
图 5 制备碳纤维增强金属基复合材料的挤压铸造工艺流程
挤压铸造法对压力控制的要求较严格。Hajjari 等研究了压力对挤压铸造法制备的
Cf/Al 复合材料的影响,发现表面预先镀 Ni 的碳纤维与基体之间的润湿性显著改善,制备复合材料所需的压力显著降低。施加过大的压力可能导致碳纤维发生严重滑移,使铝熔体不能有效渗入碳纤维间隙。碳纤维表面无涂层和无镀镍层时,采用挤压铸造工艺制备碳纤维增强铝基复合材料的最佳压力分别为 50 和 30 MPa。此外,Alten 等采用挤压铸造制备碳纤维质量分数为 2%的 Cf/Al 复合材料时发现,采用表面有 0.9 mm 厚涂 Ni 层的碳纤维制备的复合材料抗弯强度为 258 MPa,而采用涂 Ni 层厚度为 4 mm 的碳纤维制备的 Cf/Al 复合材料的抗弯强度降低到了 200 MPa。
2.5 真空压力浸渗法
真空压力浸渗法是在真空环境中,通过返冲惰性气体使金属熔体浸渗入碳纤维预制体制备复合材料的方法。毛细管引力有利于金属熔体浸渗入碳纤维预制体间隙。该方法能实现复杂构件的近终成型,负压浸渗环境有利于减少材料的铸造缺陷,但设备及工艺较复杂、产品制造周期长,目前尚未得到工业应用。
Qi 等研究了采用真空浸渗技术制备 Cf/Mg 复合材料的机制,发现界面有细小均匀的Mg17Al12 析出相形成,还有大量 100 nm 左右的晶相弥散分布于基体中。Cf/Mg 复合材料界面形成的粒状 Mg17Al12相的大小和形貌差异是 AZ31 和 AZ91 基体中 Al 含量不同所致,如图 6 所示。杨程等[51]发现,Cf/Mg 复合材料致密度随着预制体预热温度和浸渗压力的增加而提高,浸渗工艺参数中预热温度对复合材料致密度的影响更大。Wang 等采用溶胶凝胶法和钇稳定氧化锆(yttria stabilized zirconia, YSZ)对碳纤维进行表面改性,然后采用真空浸渗工艺制备了 Cf/Mg 复合材料并发现,镁基体与 YSZ 涂层反应能形成厚度约为 20 nm 的 MgO颗粒界面层;由于界面引起的体积膨胀,界面层内产生了较大的压应力,在复合材料从浸渗温度冷却的过程中,界面层应力从压缩转变为拉伸,拉应力状态会导致 ZrO2 相从四方结构向单斜结构转变,进而使界面层应力得以松弛,减少界面层的纳米结构缺陷,有利于提高Cf/Mg 复合材料的抗拉强度。
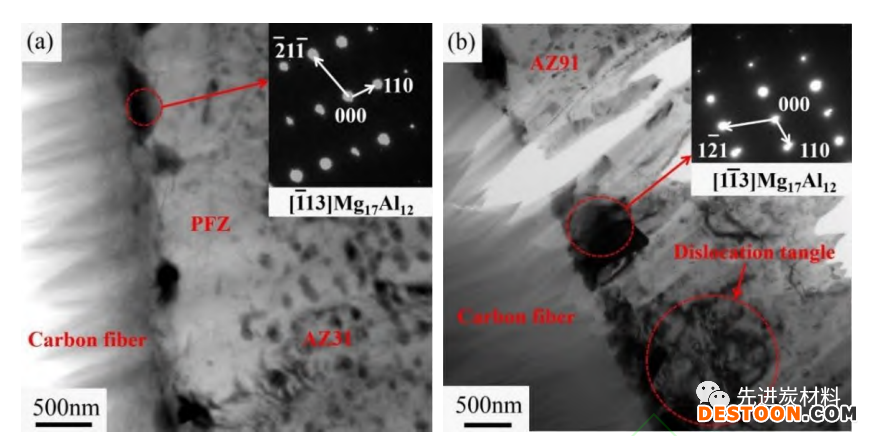
图6 Cf/AZ31(a)和Cf/AZ91(b)复合材料界面的透射电子显微图及选区电子衍射花样
3 增材制造技术在制备碳纤维增强金属基复合材料中的应用
传统的复合材料制备方法通常都包含碳纤维表面改性、纤维预制体加工、铸造或挤压等较繁琐的工序,工艺流程长、产品质量难以控制,严重制约了碳纤维增强复合材料的规模化生产。有人曾尝试采用增材制造技术制备碳纤维增强复合材料。该方法的优点是能制备形状复杂的构件,但目前多以热固性、热塑性树脂为基体。Tian 等采用工艺参数不同的增材制造技术制备了热塑性复合材料,研究了复合材料的界面特征和力学性能,结果碳纤维体积分数为 27%的复合材料弯曲强度为 335 MPa,模量为 30 GPa。
Wang 等采用增材制造技术制备了 Cf/Sn-Pb 复合材料,是利用喷嘴的压力将基体与碳纤维结合以形成紧密的内部结构和适当的碳纤维基体界面。采用优化的打印温度和速度能明显消除复合材料中的空隙等缺陷,所制备的3.0Cu-Cf/Sn-Pb复合材料抗拉强度达到了235.2MPa,远高于 Sn-Pb 合金的 33.3 MPa,与挤压铸造法制备的 Cf/Sn-Pb 复合材料接近(240 MPa)。杨立宁等研究了路径搭接率、基板温度和打印速度等工艺参数对 Cf/Sn-Bi 复合材料抗拉强度的影响,发现适当增大路径搭接率(35%~55%),提高打印喷头温度、基板温度及打印速度,能减小熔融金属的表面张力,提高流动性,使沉积层间实现良好重熔,有效避免在已沉积层表面裂纹处和路径搭接区凹坑处形成气孔,提高复合材料的抗拉强度。
总体上,有关采用增材制造技术制备碳纤维增强金属基复合材料的研究较少,现有的研究均为采用碳纤维与金属基体同步熔融浸渍、复合、挤出的方式制备复合材料(图 7),所采用的金属基体种类有限,目前仍局限于 Sn、Sn-Bi、Sn-Pb 等熔点较低的金属或合金。
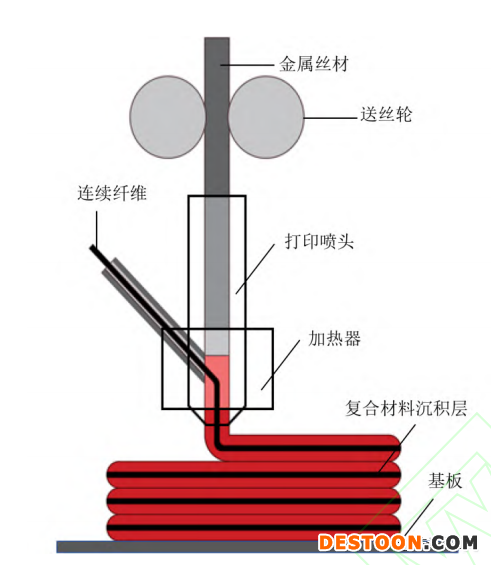
图7 制备碳纤维增强金属基复合材料的增材制造工艺的原理图
4 制备金属基复合材料的流铸印刷法
在传统的平面流动铸造法的基础上,张云虎等提出了制备复合材料的流铸印刷法新技术。其基本原理是,合金熔体在重力或其他压力的作用下,从一字型石墨狭缝喷嘴中约束流出形成帘状熔体,通过喷嘴正下方基板沿 X 轴以 m/s 数量级的速率移动,将帘状熔体以平面流动铸造的方式沿基板铺展,并通过平行于基板表面的变向辊实现碳纤维在金属熔体薄层表面同步印刷式复合,调整基板 Z 轴高度连续制备出三明治结构的复合材料块体,如图 8所示。
笔者据此研制出了流铸印刷原型机,采用商业 3K 网格状碳纤维在基板移动速度为 0.50m/s、基板与喷嘴出口间距为 10 mm、锡熔体流铸温度约为 280 ℃的条件下制备出单层 Sn金属板和 Cf/Sn 复合材料,其宏观形貌如图 9 所示。单层 Sn 金属基体板的厚度约为 1 mm,Cf/Sn 复合材料由 4 层锡金属夹 3 层碳纤维构成,外形尺寸为~200 mm 80 mm5 mm。从复合材料厚度方向的截面宏观形貌可以看出,碳纤维束在金属基体内的空间排布较均匀,金属基体无明显缩孔(图 10(a))。图 10(b,c)表明,Sn 金属基体与碳纤维束之间的界面结合紧密。这些结果表明,流铸印刷法中同步印刷式碳纤维复合能使碳纤维和高温合金基体薄层在较短时间内完成冶金熔合,避免碳纤维的团聚偏析并有效抑制界面的强烈反应。相比增材制造技术,流铸印刷法可用于制备 Al、Cu、Ni 等高熔点合金,碳纤维规格多样(疏密度、结构花样等)也使复合材料的结构特征可以调控,该方法具有高效低成本、易规模化推广等特点。
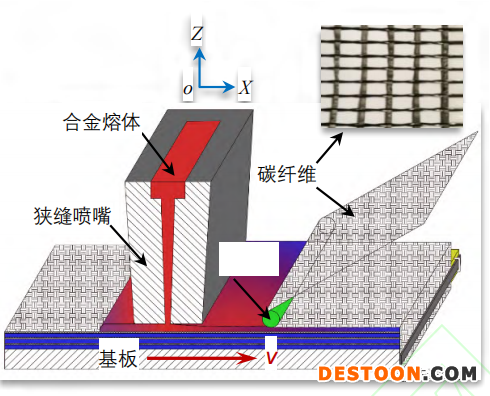
图 8 制备碳纤维增强金属基复合材料的流铸印刷法原理图
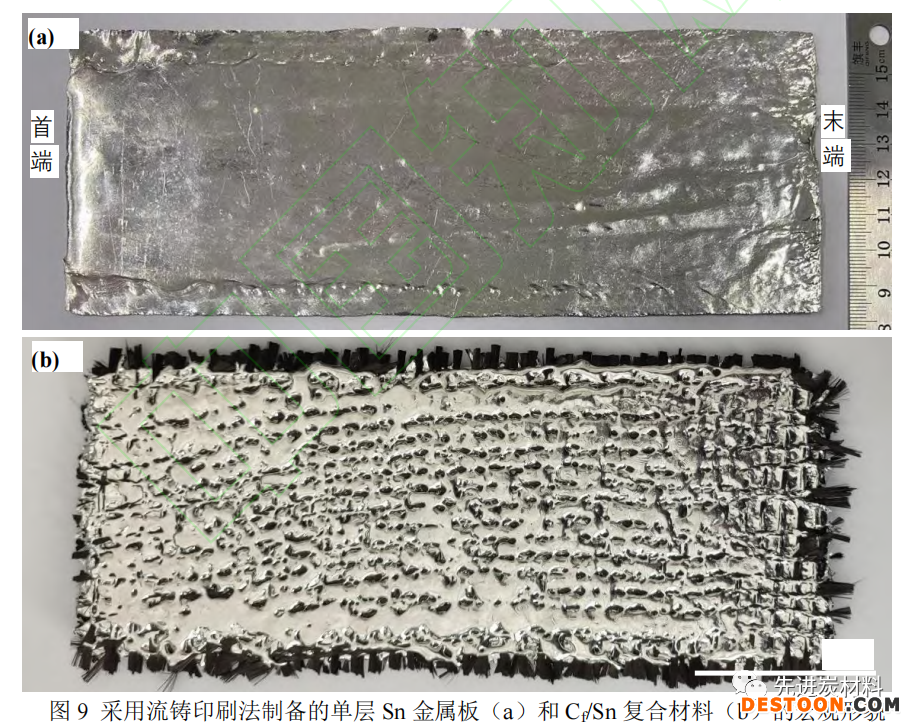
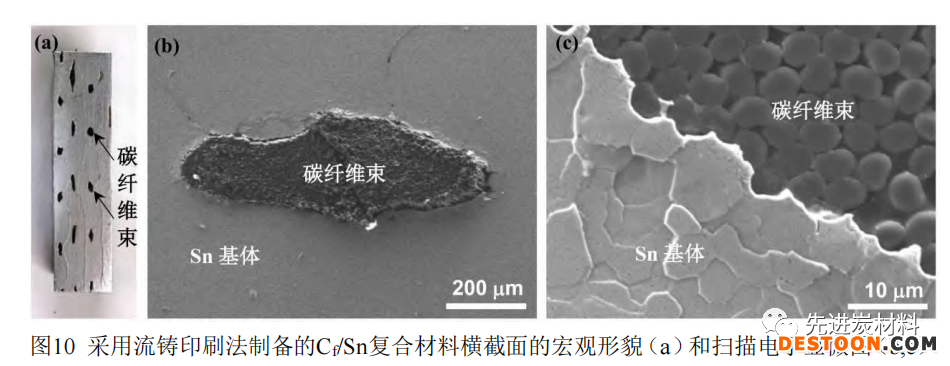
5 结束语
碳纤维增强金属基复合材料是国民经济发展和尖端科技创新不可或缺的基础材料,未来应进一步开展以下方面的研究工作。
首先,研究金属基复合材料的界面调控。传统的制备金属基复合材料的方法存在碳纤维团聚偏析和界面强烈反应的问题。流铸印刷法有望成为未来制备金属基复合材料的新方法,但有关界面结合与反应机制等关键问题仍需结合具体的制备方法从材料学层面深入研究。
其次,增材制造技术用于碳纤维增强金属基复合材料的规模化制备前景广阔,但目前存在金属基体种类有限、制造效率亟待提高等问题。突破现有技术思路、探索新技术新工艺对于推动碳纤维增强金属基复合材料的发展具有重要的科学和现实意义。
此外,从产品质量监测和高效制造出发,研发出针对碳纤维增强金属基复合材料的无损检测或空间物相结构在线实时解析技术,融合人工智能方法,贯穿全流程构建多模态数据驱动的工艺决策优化与产品质量管控系统,今后也应得到更多的关注。
来源:上海金属
作者:征立志,周玉兰,张云虎,郑红星
转载:先进炭材料