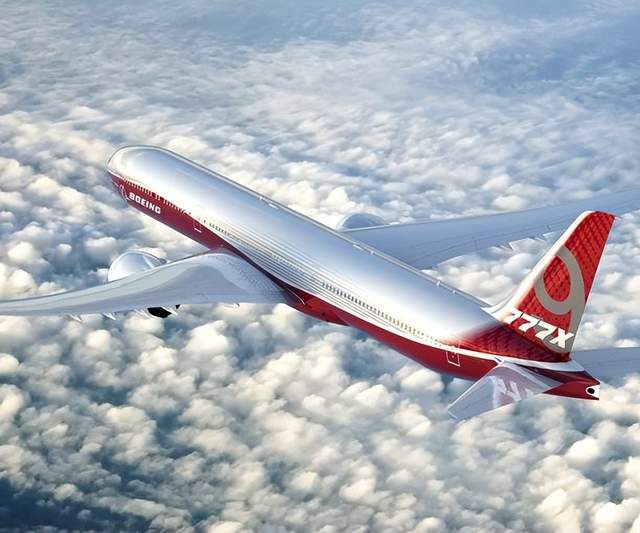
波音777X飞机采用全复合材料机翼,翼展71.75 米。具有自动检测能力的自动铺丝机(AFP)将用于制造机翼蒙皮和翼梁。
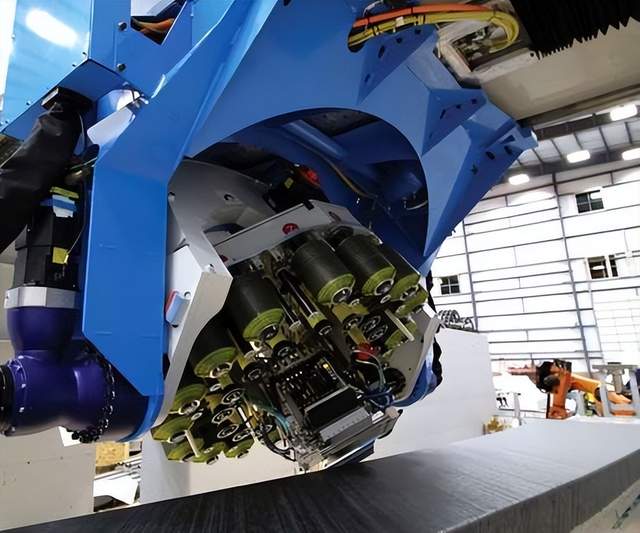
图为波音 777X 碳复合材料翼梁的生产试验
期间,Electroimpact 的自动铺丝机(AFP)头。在线检查有望帮助生产流程跟上当今的AFP/ATL 系统。
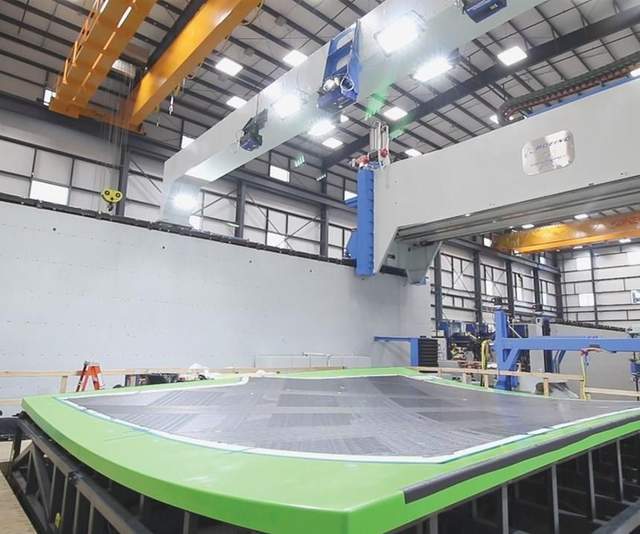
在ElectroImpact 的设施中展示了 777-X 机翼蒙皮段的试制试验。注意零件上方的第二个 龙门架(顶部、中心),其上安装了三台 Aligned Vision LASERVISION 投影仪,用于对机翼蒙皮叠层进行自动过程检查。
航空航天复合材料领域的任何人都不知道,由先进的铺层工艺(自动铺丝机-AFP)和(自动铺带机- ATL)固定的商用飞机装配线的生产率受到每次铺层后仔细目视检查和验证的必要性的限制。通常,返工也必须由经过培训的专家完成,以满足质量保证要求。对于需要数百层的机身筒或其他大型复合材料零件,检查和返工的影响是显著的。
在几年前由 Fives Cincinnati(美国肯塔基州希伯伦)的 Robert Harper 和波音公司(美国伊利诺伊州芝加哥)的 Allen Halbritter 发表的一篇论文中,根据使用优化AFP工艺铺设的通用机身机筒的数据,检查和返工占零件总生产时间的 60%以上。最近,Electroimpact股份有限公司(美国华盛顿州穆基尔特奥)的高级工程师 Todd Rudberg 表示,手动检查/维修活动通常占零件制造时间分布的 30%以上。
在过去的几年里,许多研究和开发都致力于找到一条使用数字方法进行自动检查的途径,以使整个飞机生产流程能够跟上当今 AFP 和 ATL 流程的效率。为此,航空航天复合材料零件现在由配备机载自动检测系统的 ATL 和 AFP 机器制造。ATL/AFP 机器供应商已经开发并继续完善能够检查铺放并向技术人员发出异常警报的系统。在关于这个主题的一系列文章的第一篇中,CW 介绍了为 Electroimpact 的 AFP 机器开发的自动化原位检测设备。
取消手动检查
Electroimpact 始于1986年,当时创始人Peter Zieve 将他的第一台用于铝飞机组装的低压电磁铆接机商业化,该机提供了比航空航天原始设备制造商使用的现有铆接机更安全、更便宜、噪音更小的技术。从那时起,该公司通过扩大业务重点,为金属和复合材料提供一系列自动化生产解决方案而蓬勃发展。客户不仅包括波音公司,还包括其他航空航天原始设备制造商,包括空中客车公司(法国图卢兹)、庞巴迪公司(加拿大蒙特利尔QC)、Spirit AeroSystems 公司(美国堪萨斯州威奇托)等。
Rudberg 是开发 Electroimpact 第一台 AFP 机器及其控制软件的团队成员,他说:“在过去三年里,我们一直在开发自动化的过程中检测。我们的检测系统是目前唯一一个获得 OEM 完全认证的复合材料零件生产自动检测系统。”。事实上,该公司的 AFP 机器正在为波音公司的第一架 777X 测试飞机生产首件机翼面板和翼梁,并对机翼面板零件进行了自动检查。这些是在美国华盛顿州埃弗雷特的波音新复合材料机翼中心(CWC)的两个 Electroimpact 设计的自动化工作室中制造的,专门用于处理世界上最大的 777X 复合材料机翼的制造和生产。值得注意的是,这架飞机 72 米的巨大翼展将在地面上通过每个 3.5 米长的折叠翼尖缩小,以使机组人员能够进入与今天的 777 相同的机场登机口。777X 翼尖和折叠硬件将在波音公司位于美国密苏里州圣路易斯的工厂制造。CWC 还安装了两个AFP 工作室,以生产一体式复合材料翼梁。
Electroimpact 的控制工程师 Josh Cemenska 解释 说,翼梁由两部分(上和下)通过 AFP 在低曲率中制成,阳模位于每个工作站的龙门工作包络内。安装了 Electroimpact AFP 头的主龙门架沿着 30 米翼梁工具的长度移动,和稍远一点,铺放头本身可在机架上移动7.5 米,以在其最宽点处接近工具的整个 9 米宽度;铺放头的 z 方向移动约 2m。该材料为 34mm/1.5 英寸宽的碳/环氧树脂预浸带,由 Toray Composite Materials America(Tacoma,WA,US)提供。
Rudberg 断言:“对于 777X 面板来说,自动化检查是必要的。”。“零件太大了,你真的无法进行手动检查。我们的自动检查系统真的是下一代机翼的一项关键技术,使用手持放大镜检查是否有丝束重叠或缺失。
取而代之的是,Electroimpact 翼板单元集成了三个20.5公斤的 LASERVISION 投影盒单元,每个单元都配备了除了激光投影仪之外,还配备了高分辨率相机。由 Aligned Vision(美国马萨诸塞州切姆斯福德)提供,每个单元都与安装在头部的激光轮廓仪协同工作,激光轮廓仪本质上是一种将线投射到工作表面上的小型激光器。所有三个元件(激光器、相机、轮廓仪)都将数据提供给计算机软件算法支持的用户界面。
Aligned Vision 投影盒单元成排安装在第二个龙门架光束上,该光束独立于头部龙门架工作,但通常在其后面。Rudberg 说,这种配置最大限度地缩短了激光器和零件之间的距离,并降低了入射角。Aligned Vision首席运营官 Matt Zmijewski 解释道,“777X 机翼面板和翼梁是 LASERVISION 的发射应用,它提供两个关键功能。从一个光圈投射激光,由一组两个可操纵的反射镜定位。从第二个光圈,一个带 300 毫米镜头的高分辨率数码相机也由两个反射镜操纵,以捕捉正在进行的材料沉积的照片。”
高清图像在三维中精确定位,因为相机和激光在同一坐标系内工作,“转换”或配准到空间中的工具和头部位置。每个相机像素的 3D 位置由用户界面识别。图像集被联合起来,以在整个零件上创建每个层的完整图像。图像分辨率足够高,可以根据该图像自动测量帘布层边界位置。Electroimpact 表示,在移动(即龙门架安装)设置中,帘布层边界的摄像头图像已被确认在真实位置的±0.060 英寸/±1.5 毫米范围内。
利用大数据
Cemenska 说,与此同时,激光轮廓仪在材料沉积过程中在零件表面投影一条线,其内置的探测器阵列测量沿着该激光线的 1000 多个离散位置的高度。因此,它检测表面的 2D 轮廓。当轮廓仪在材料沉积过程中与头部一起移动时,它实际上会创建 3D 表面轮廓。
正如 Cemenska、Rudberg及其同事Michael Henscheid、Andrew Lauletta 和 Bradley Davis 最近撰写的两篇白皮书中所解释的那样,轮廓仪的激光线横跨丝束之间的接缝,在上篮过程中测量任何重叠和间隙的宽度。这些轮廓仪数据与来自相机和零件程序的数据以及操作员输入集成在检查用户界面内;随着生产的进行,界面构建零件的逐层 3D 模型。
识别软件从大量的相机图像数据以及轮廓仪生成的原始数据阵列中测量特征的位置,以查看丝束末端(或帘布层边界)、丝束重叠和间隙,并识别褶皱和桥接等缺陷。然后在三维模型上显示这些。
Rudberg 说,处理收集到的数据所需的用户界面和算法是由Electroimpact 软件工程师在内部开发的。(据波音公司称,一种并非由 Electroimpact 开发的异物检测系统即将问世。)
Electroimpact 自动帘布层边界检查系统可以正确识别和测量标准帘布层上 92%的两端,平均误差小于±0.005 英寸,标准偏差为±0.020 英寸。Rudberg 说,用轮廓仪进行的重叠/间隙测量与材料放置同时进行,可以比手动检查更快地完成。如果出现关于拖尾或间隙/重叠的问题,则将选择的图像转发给检查员,以便在工作单元的计算机屏幕上进行评估。Cemenska 说:“我们几乎已经消除了任何手动检查。如果我们发现罕见的错误,比如丝束掉落,LASERVISION 的激光线会显示该区域,必要时会将坏丝束拔出。然后对机头进行重新编程以进行维修。”,因为随后会对零件边缘进行修剪,这样可以节省额外的时间。
检查速度取决于帘布层的复杂性,并且随着拖尾数量的增加而降低,这就是为什么蒙皮的检查系统比翼梁的检查系统具有更高的优先级,Rudberg 说:“由于零件的尺寸和扁平形状,以及波音公司不希望检查员在铺放时行走,因此优先考虑的是蒙皮零件的自动检查系统的启动和运行,因此我们将工作重点放在了那里。关于翼梁,铺放和层压是主要障碍,所以我们首先在这方面进行了工作。”
Cemenska 报告说,检查系统每秒可以测量 15 个尾端;在拥有多达 2000 个已检查尾端的蒙皮零件上,以下相机需要几分钟的时间来拍摄照片,软件需要几分钟来组装帘布层图像。Rudberg 说,总的来说,复杂的帘布层需要 3-5 分钟的时间来成像和处理:“目前,我们的目标是 100%的检查,所以我们没有识别的 8%的尾端目前是用肉眼‘半自动’定位的,所以这增加了大约 10 分钟。”他补充道,通过加快软件系统的速度,可以加快这一半自动步骤。最终,如果统计数据显示 92%的识别末端准确地代表了整个零件,则可以完全消除 8%的需求。“现在还处于早期阶段,仍有改进的空间——随着对系统信心的增强,未来人类的双重检查可以减少到几乎为零。”
Electroimpact 与波音公司合作,通过进行一系列严格的预验收测试,对该系统进行了验证:Rudberg 和Cemenska。这些结果使波音公司相信了该系统的可靠性,从而在777X的零件上采用了。波音公司表示,对一体式翼梁的过程检查计划于今年年初实施,这是有史以来最大的一次生产。
Rudberg 总结道:“这是对大数据的明智使用。我们正在测量每根丝束相对于帘布层边界的位置,并创建结果的数字记录。这些数据提高了零件质量,并使客户能够做出更明智的决定。因为我们可以用数字方式证明零件质量,所以最终将允许使用限制较少的设计容许值。”
现在肯定是开发一种急需的技术的时候了,这种技术可以让自动化复合材料制造机器以设计的速度运行。毫无疑问,它将应用于其他零件。
END
注:原文见《 Improving composites processing with automated inspection 》 2018.1.29
777X 机翼装配厂房:占地 150 万㎡(160 万平方英尺)。该建筑包括19 万㎡ (200,000 平方英尺)的高架空间制造场地,采用 107m (350 英尺)的净跨度结构和14 万㎡(150,000 平方英尺)的侧翼支撑和办公空间。该工厂拥有复杂的机器人工具、复杂的机械和特种管道系统,以及三台 37m 长 (120 英尺长)的热压罐,用于固化 777X 飞机的碳复合材料机翼的压力容器。
杨超凡 2023.11.14