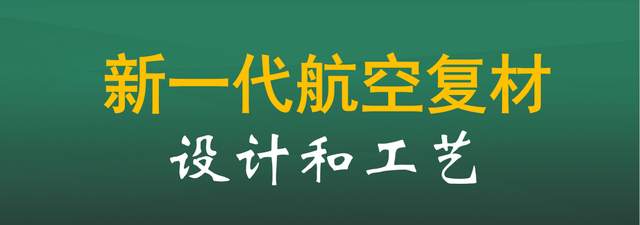
Spintech在制造机翼和进气道演示上使用其智能工具、干纤维预成型件和RTM/VARTM技术,显著节省了成本和劳动力。
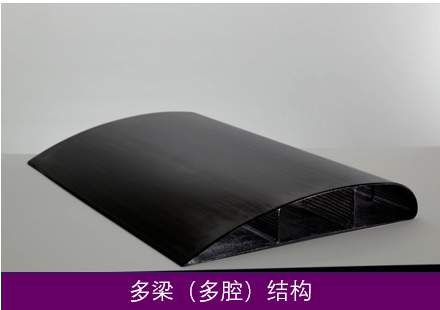
树脂传递模塑碳纤维复合材料战术飞机演示机翼Spintech Holdings股份有限公司及其制造部门霍索恩复合材料公司(Hawthorn Composites)正在使用这种小型战术无人机机翼等演示部件,以测试和验证注入和预成型技术在更具成本效益的航空航天和国防部件中的应用。
多年来,预浸料和热压罐固化一直是航空航天和国防复合材料部件的常用技术。Spintech Holdings股份有限公司(Xenia,Ohio,U.S.)及其制造部门霍索恩复合材料(Hawthorn Composites,Xenia)正在努力证明,通过使用现有技术(如树脂注入和编织干纤维预制件),可以以新的方式制造更具成本效益、劳动密集度更低的航空复合材料零件。
Spintech最初是从Cornerstone Research Group(美国俄亥俄州迈阿密斯堡)分拆出来的,专注于开发其创新的智能模具形状记忆聚合物(SMP- shape memory polymer )模具技术,该技术由可再成型的囊、茎或芯模组成,可重复使用多达100个生产周期。2010年公司成立后的头几年,Spintech主要由Spirit AeroSystems(美国堪萨斯州威奇托)资助,这使该公司能够扩大其技术规模,以生产具有共固化框、长桁和蒙皮的单通道商用飞机机身。
2015年,Spintech扩展到更广泛的航空航天市场,并于2016年调整了其智能工具技术的制造流程。Spintech Holdings股份有限公司总裁兼首席执行官克雷格·詹宁斯(Craig Jennings)表示:“我们从需要一套专用金属模具来制造智能工具的RTM(树脂转移成型)工艺,到能够使用真空辅助树脂转移模塑(VARTM- vacuum-assisted resin transfer molding)制造智能工具,并在循环之间使用同一套模具来改造智能工具。这减少了部署智能工具约40%的资本成本,因此从成本承受能力的角度来看,它确实为我们打开了一个更广阔的市场。从那以后,我们一直在增长。”
除了智能工具,Spintech还扩展到最终用途组件的制造,最近成立的制造部门Hawthorn Composites以及与A&P Technology(美国俄亥俄州辛辛那提市)合作供应编织产品,与代顿大学研究所(美国奥州代顿市UDRI)合作开发和供应使用定制纤维放置或技术刺绣工艺制造的纤维预制件,进一步巩固了这一举措。
“树脂注入并不是什么新鲜事,但这是航空航天工业现在以一种新的方式采用的技术,因为它们能够在具有相同甚至更好性能的复合材料部件上实现大幅降价。”
在过去的几年里,Spintech已经证明RTM和VARTM工艺,结合智能工具和使用自动化技术制造的干纤维预成型件,可用于航空航天、国防和其他市场中更具成本竞争力的最终用途组件。
詹宁斯说:“使用干式碳纤维包覆或定制纤维预成型件和树脂注入,我们可以显著降低材料成本和劳动力要求,并且与预浸料、热压罐固化部件相比,能够以相同的重量提供相同的质量,在某些情况下甚至更低。我们认为这是未来十年市场的发展方向。”。“我们正在倾听客户的声音,我们正在定位这个部门,以利用市场的发展方向和客户的发展方向。”
迄今为止,Spintech已经证明了RTM和VARTM在各种部件上的成本效益,包括最近的飞机机翼和进气道。
战术无人机机翼:展示正压RTM
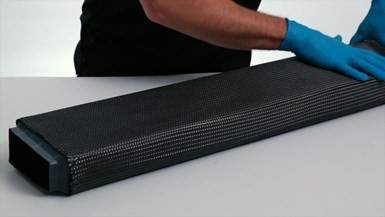
步骤1. 智能工具用干燥的碳纤维套筒包裹。
多年来,Spintech一直为小型飞机和无人机(UAV)的预浸料、热压罐固化机翼和控制面提供智能工具解决方案。鉴于预浸料和热压罐固化的高成本,该公司认识到,这是一种可以将RTM与智能工具和编织预成型件相结合的应用。为了证明这项技术和工艺,Spintech最近根据用于全面客户项目的设计建造了一个小型战术无人机机翼演示器。该演示器也是大型飞机控制面的适当规模和复杂性。
机翼演示器的复合材料叠层
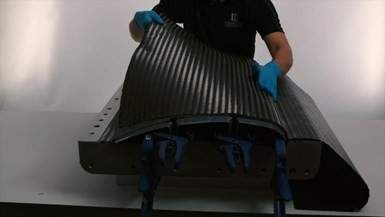
步骤2. 在RTM工具的下半部分,QISO织物层和包裹的智能工具被放置成对齐状态。
为了制作机翼,首先,将两层A&P的QISO准各向同性编织三轴织物铺设在RTM工具的下半部分,形成下机翼蒙皮。三个智能工具包裹在A&P Technology提供的编织干碳纤维套管中,并固定在QISO织物层的顶部。为了制作机翼的后缘,将A&P供应的网状面条预制棒(一种横截面为三角形的编织绳)放入工具中。“下蒙皮和上蒙皮在网状面条几何形状上结合在一起,
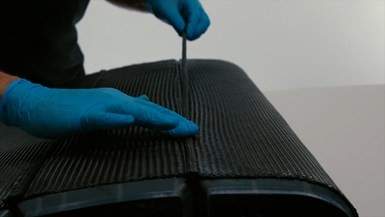
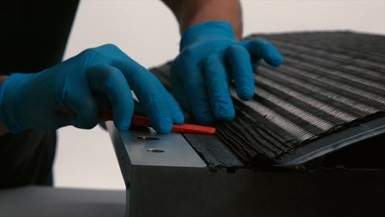
步骤3. 定制的“面条”预成型件被放置在智能工具之间的间隙内,并沿着零件的后缘。
Spintech Holdings股份有限公司总裁汤姆·马格拉夫(Tom Margraf)表示:“我们有一个连续的产品,我们只需按长度切割并放入。”工具下半部分的QISO织物切割得足够长,多余的部分可以折叠在面条区域,然后将两层最上面的皮层蒙皮放在对齐的智能工具和后缘上完成上铺。然后将上半模盖在下半模上,密封并栓接在一起。接下来是中间密封板,其中包含孔,以便空腔贯穿三个智能工具。真空袋通过智能工具腔插入并密封到中间密封板上。随后,添加压板以密封模具。
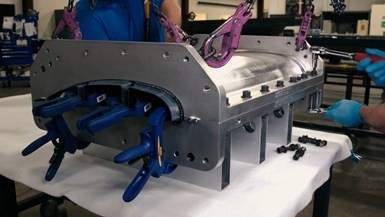
步骤4. RTM工具已关闭并密封。
一旦RTM工具关闭并密封,就会抽真空,马格拉夫说,“这为我们提供了一个密封的腔体,现在可以容纳干燥的纤维预制棒。通过创造密封的环境,我们还可以在智能工具的内部施加正压。这是市场上其他解决方案无法做到的一件非常独特的事情。”
对于机翼演示器,智能工具内部施加了75 psi的压力。在RTM过程中,智能工具处于热弹性状态,内腔压力形成半刚性壁,以注入树脂。马格拉夫说:“只要我们保持20psi的压差,使智能工具的内部始终比RTM压力高20psi,我们就可以保证智能工具处于适当的位置,并且我们在层压板上得到了良好的压实。”。
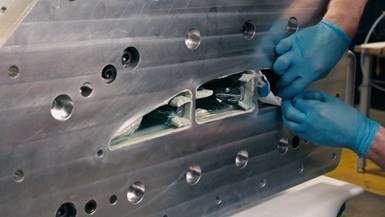
步骤5. 真空袋被拉过智能工具并加压。
他补充道:“智能工具的设计尺寸小于复合材料层压板的体积系数,因此它们略小于实际的最终内模线零件定义。我们这样做是为了降低RTM的力要求。”
注入过程在炉内进行,注入容器内的树脂温度升高到125°F,零件温度加热到176°F。注入后,温度升至250°F进行零件固化(据说Smart Tools与高达375°F的固化温度兼容),一旦干燥的纤维预制棒完全润湿,工具内的树脂入口就会关闭,使75 psi的内腔压力能够完全固化层压板并排出多余的树脂。
马格拉夫说:“我们可以用热压罐式纤维体积创建低压RTM工艺。”。“由于层压板最初没有变松,树脂将比使用匹配金属模具的传统RTM工艺更容易流动和渗透到干燥的纤维预制棒中。”Spintech团队在内部称之为“反向热压罐效应”
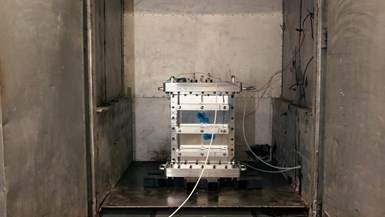
步骤6. 该零件在霍索恩的工业规模烤箱内高温注入。
系统成本节约来自使用烤箱而不是热压罐按,以及使用低压RTM系统。马格拉夫说:“我们不需要在RTM系统上达到200或400 psi;我们的大多数零件都是在50 psi或更低的正压下注入的。我们不仅不使用热压罐,而且还使用了低压RTM系统,从而大大降低了成本。”。
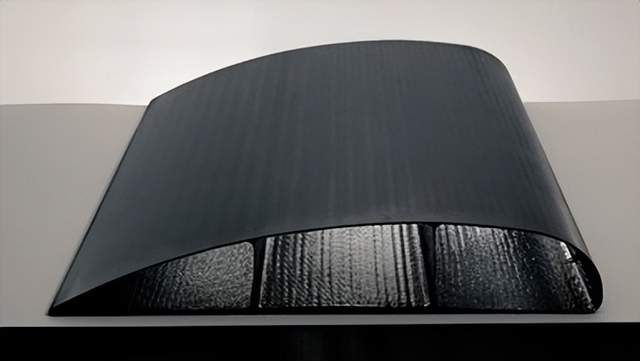
步骤7. 最后一部分从工具中提取出来。
詹宁斯(Jennings)补充道:“我们发现,仅材料节约就可能是购买预浸料制造相同零件的三分之一,而且还可以节省大量劳动力。”。“总的来说,这样的节省很容易在零件总成本的20-50%范围内。
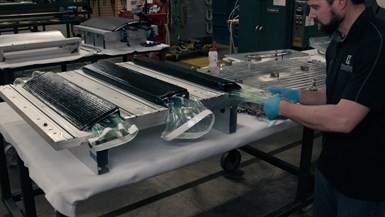
步骤8. 然后可以对智能工具进行改造以供进一步使用。
这项技术也可用于其他通用航空部件。在2020年底和2021年初,Spintech使用RTM展示了一种制造多腔通用航空油箱的低成本方法。根据马格拉夫的说法,用预浸料制造储罐的成本约为每罐30000美元。通过使用智能工具和编织预成型件转换为RTM,每罐的成本降低到约10000美元。他说:“与预浸料方法相比,我们采用这种方法的成本大约是三分之一,而且它是一个结构上等效的部件,实际上比预浸料部件轻约15%,因为我们能够使用连续的编织物,而不是层压和连接在一起的不连续的预浸料层。”。这种方法还将生产时间从大约一周缩短到不到一天。
VARTM用于商业化更具成本效益的进气导管
Spintech还展示了VARTM用于内部成型线最重要的组件,从战术无人机入口导管开始,该导管与机翼演示器一样,基于该公司已经制造的预浸料/热压罐设计。据马格拉夫介绍,霍索恩公司首先为其客户制造了五个进气管零件,使用碳纤维预浸料在Smart Tool上铺设,并在热压罐中固化。然而,Spintech知道,改用树脂注入的编织预成型件可以节省劳动力和材料成本,并想确切地知道节省了多少。“然后,我们自费使用VARTM进行了结构等效的编织部件的制造,然后分析了从预浸料到编织注入的转换所节省的成本,”他说。
马格拉夫解释说,管道的预成型件是在A&P Technology辛辛那提工厂的编织机上预先制造成适当几何形状的。一旦交付给霍索恩公司,预成型件就会手工施加到芯模上。他说:“这是手工叠层,但它仍然可以节省大量时间,因为我们在一个预成型套筒中应用了一个覆盖整个湿润区域的完整编织层。我们在大约五分钟内拉动并定位了一层,而用预浸料层压板做同样的工作需要两个多小时,因为你可能有几十块单独的预浸料来获得与12k编织层相同的结构等效性。”
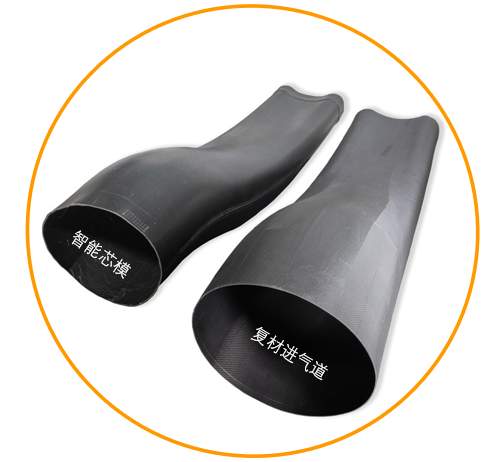
一个完成的进气导管演示器(右)坐在其相应的智能芯模(左)旁边。
客户考虑了使用多件式铝心模与智能工具解决方案,但仅在工具上节省的资金就减少了46%,从75000美元减少到40000美元。通过从预浸料到干纤维编织和浸渍的转换,生产零件的接触时间也减少了67%。马格拉夫说,总体而言,每个零件的客户成本将降低近50%。
2月1日,Spintech宣布,霍索恩公司已获得Kratos Defense&Security Solutions股份有限公司(美国加州圣地亚哥)的制造合同,为XQ-58A Valkyrie无人机提供12个进气道,使用智能工具、VARTM和编织预制件。
“最终,这项技术正在向多个不同的客户和多个不同市场过渡,” 马格拉夫说。“从通用航空油箱到大型战术无人机零件,再到最终的商用飞机零件。”
航空复合材料的未来
Spintech团队认为,这项技术是许多航空航天和国防部件的发展方向。现有客户已经报告称,与传统流程相比,成本降低了20-50%,因此大规模接受的目标似乎触手可及。
詹宁斯(Jnenings)说:“当你考虑航空航天制造业的前沿技术时,树脂注入并不是什么新鲜事,但这是航空航天业现在以一种新的方式采用的技术,因为他们能够在具有相同甚至更好性能的复合材料零件上实现大幅降价。”。“最前沿的部分是自动化。我们现在有能力用编织预成型件和定制纤维放置等尚未被广泛采用的自动化方法来实现这一点。自动化与低成本的干纤维和树脂相结合,使一切变得不同。”
原文见,《 Braided preforms and resin infusion for next-generation aerocomposites 》 2021.5.18

美国空军和俄亥俄州的复合材料团队开发了S形飞机结构的新工艺。
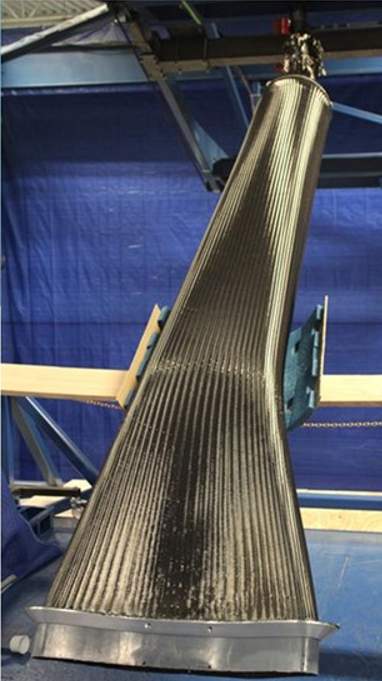
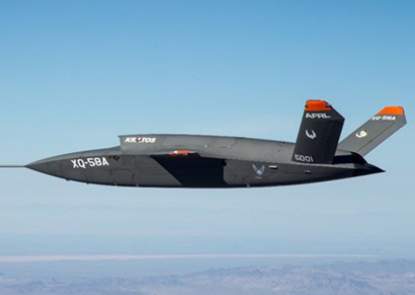
在树脂注入之前,显示了一个11英尺长的进气管预成型件,这是美国空军研究实验室(AFRL)计划的一部分,该计划旨在降低无人机系统的成本,如奎托斯防御与安全解决方案公司为美国空军低成本可磨损打击演示器计划设计和制造的奎托斯XQ-58 Valkyrie(如图所示),该计划是AFRL低成本易损坏飞机技术项目组合下的一部分。
美国空军2030年科技战略的一部分包括大规模部署低成本无人机系统,以协助未来的作战。为了实现这一愿景,必须确定新的制造策略,以支持以比目前使用传统工艺更低的成本快速制造高质量的航空航天零件。
空军研究实验室(AFRL,美国俄亥俄州代顿)制造和工业技术部以及美国俄亥俄州Cornerstone研究集团(代顿)、A&P Technology(辛辛那提)和Spintech LLC(Xenia)的承包商团队进行了研究,以量化用干纤维编织预制件和真空辅助树脂传递模塑(VARTM)代替传统预浸料手工铺层制造11英尺长的s形复合材料发动机进气道的好处。
飞机发动机进气管道提供恒定的空气供应,以防止发动机压缩机失速。进气口必须产生尽可能小的阻力。气流供应中的最小间隙可能会导致严重的发动机问题以及显著的效率损失。如果进气管要提供足够的空气和最小的湍流,它必须清洁无瑕。
S形进气道的新型制造方法取代了在多件式钢芯模上手工铺叠预浸料,然后用自动包覆工艺进行热压罐固化,该工艺采用干纤维。非常重的多件式钢芯模被轻质的单件式形状记忆聚合物(SMP-shape-memory polymer)芯模所取代。干编织碳纤维使用VARTM与低成本环氧树脂和烘箱固化加工成复合材料结构。
该团队完成了对过冲结构的分析,以及SMP成型工具和SMP芯模的制造,SMP芯模在预成型件过冲过程中用作工具。由于S形进气道的复杂几何形状,需要多次迭代来优化过冲机设置并最大限度地减少复合材料起皱。将制造总共四个进气管道,并将传统零件成本和生产时间与新设计进行比较。
AFRL制造和工业技术部低成本易磨损飞机技术倡议的制造负责人雷格·内斯伦克(Craig Neslen)表示:“我们认为,引入可重复使用的形状记忆聚合物芯模以及自动过冲工艺和基于烤箱的VARTM复合材料固化将显著降低成本和周期时间。量化制造效益和验证结构完整性对于建立积极的商业案例以及说服设计师和制造商将新材料和工艺纳入未来的低成本发动机进气道设计至关重要。”
最终的进气道将交付给美国空军,以进一步整合到美国空军研究实验室航空航天系统局的补充机身设计和制造计划中。航空航天飞行器部门将对集成编织机身和进气道结构进行静态地面测试。
“虽然我们还没有确定磨损公差对设计标准以及由此使用的制造材料和工艺的所有影响,但我们确实有一个强度和刚度阈值要求的基线,我们将通过全尺寸机身地面测试进行评估,”航空航天部的航空航天工程师雷·费舍尔(Ray Fisher)说。
AFRL是美国空军的主要科学研究和开发中心。它在为我们的空中、太空和网络空间部队发现、开发和整合负担得起的作战技术方面发挥着不可或缺的作用。AFRL在全球9个技术领域和40个其他业务部门拥有11000多名员工,提供从基础到高级研究和技术开发的多样化科学技术组合。
原文见,《 AFRL evaluates braiding, SMP tooling and VARTM for lower-cost future engine inlet ducts 》 2020.4.3

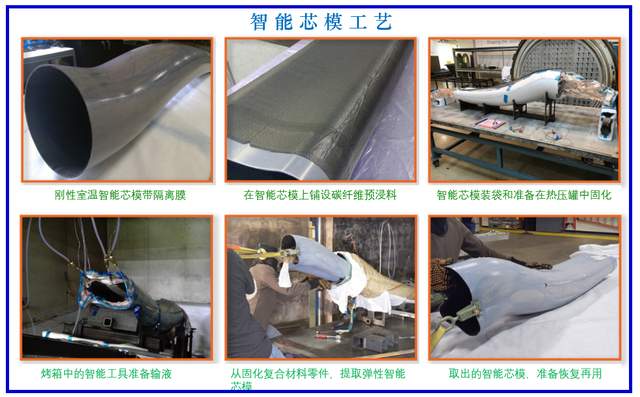
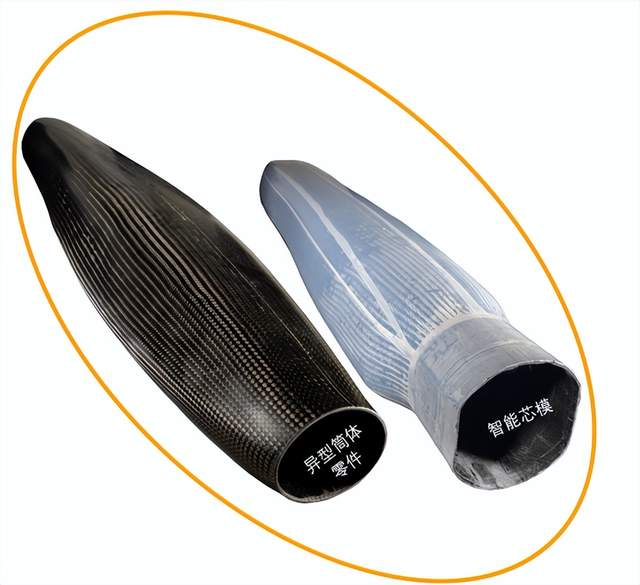
注:导弹壳体
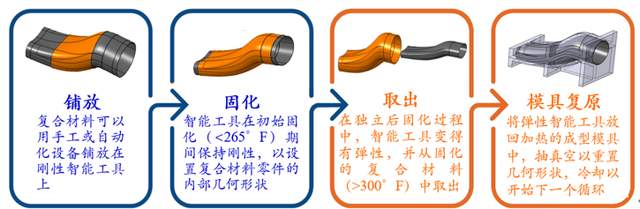
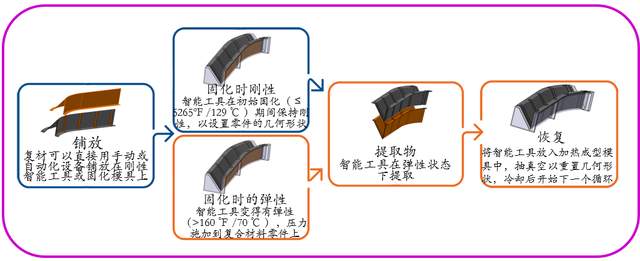
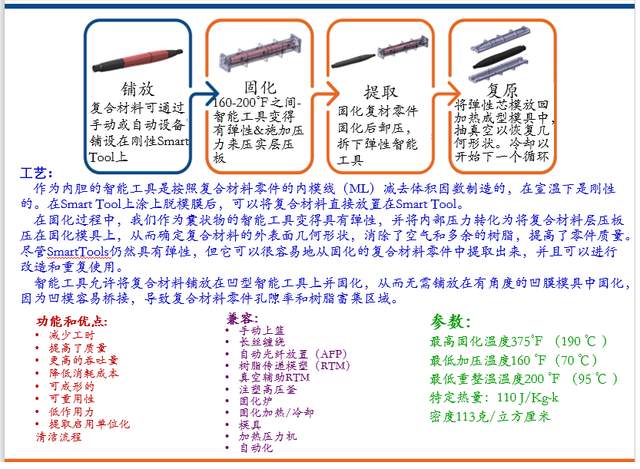

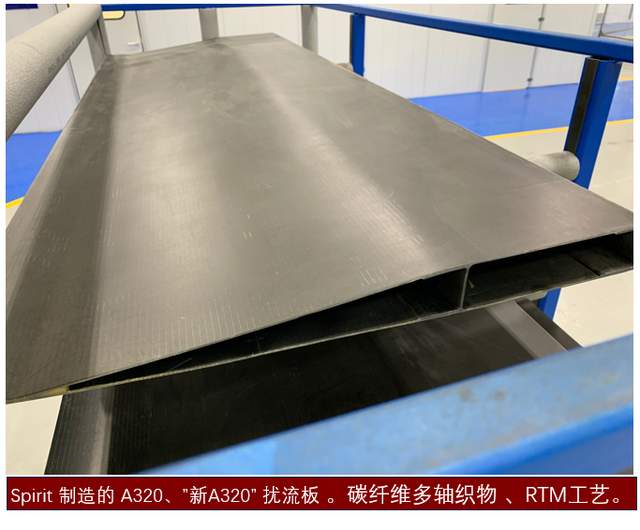
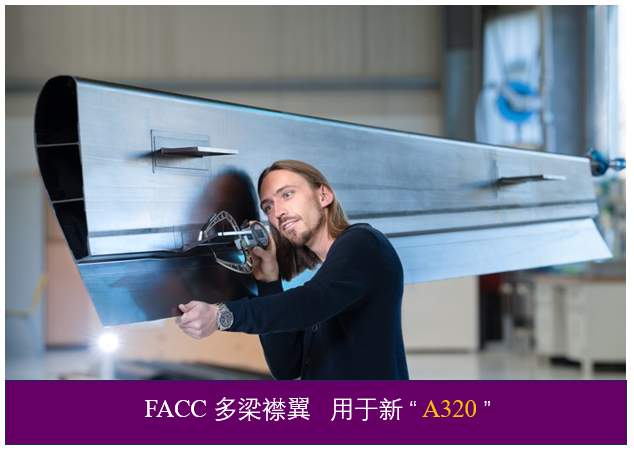
编译者寄语
形状记忆聚合物(SMP-shape-memory polymer)芯模是近十多年来,研发较成功的一种特殊工艺。目前还处于专利、商业保密阶段。对我们复材制造企业的应用,还需要进一步开发研究。但是,对翼面类组件,如襟翼、副翼、扰流板,可以用金属芯模制造多梁(多腔)结构。多梁(多腔)结构显然易见,零件数量少、连接件少、重量轻。由此联想到C929。如果C929的襟翼、副翼、扰流板也用多梁(多腔)结构,无疑C929在这一点上超过空客A350了。