七年攻坚暗战
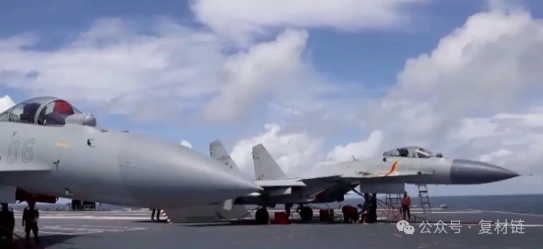
2017年的某个深夜,中国商飞复材总师陈萍在实验室摔碎了一块试验件。彼时国产复材合格率不足50%,而空客标准要求99.97%。团队面临三重封锁:日本东丽停止供应T800级碳纤维,美国赫氏拒绝出售树脂配方,德国设备商禁售自动铺丝机。
转机出现在陕西汉中。中航工业特飞所的工程师从渔船龙骨获得灵感,首创“双曲面共固化”技术——将128层碳纤维预浸料像制作千层蛋糕般精准堆叠,在高温高压罐中一次成型。这项突破使零件接缝减少80%,减重效益额外提升15%。
智能制造的决胜时刻
在镇江航发复材基地,AGV小车正运送三米宽的碳纤维织布。机械臂上的激光探头以0.02毫米精度扫描布面,人工智能系统实时比对十万张缺陷样本库。基地负责人展示了两组数据:2020年人工质检每小时查两平方米,如今AI系统每分钟检测二十平方米;产品不良率从万分之五降至百万分之一。
更关键的突破藏在车间的“黑灯仓库”里。这里存放着国产T1100碳纤维,其直径仅5微米(头发丝的1/14),强度却超日本同类产品12%。中科院团队独创的等离子表面处理技术,使纤维与树脂结合力提升三倍,达到军用直升机旋翼标准。
产业协同的乘法效应
C919复材机翼的成功,正催生民用产业链蝶变。山东德州的光伏支架厂里,航空级复材制造技术被移植到民用领域,生产出比钢材轻60%的太阳能骨架。湖南株洲的磁浮列车车间,碳纤维舱体使列车减重两吨,每公里节电30度。
中国商飞预测:到2030年,国产民机复材使用比例将从现在的12%增至50%,市场规模突破两千亿。此刻在南昌瑶湖机场,全球最大复材无人机“神鹰”已完成首飞,其三十米翼展的90%采用国产碳纤维——这架验证机的蒙皮,正与C919第100架机的机翼出自同一条生产线。