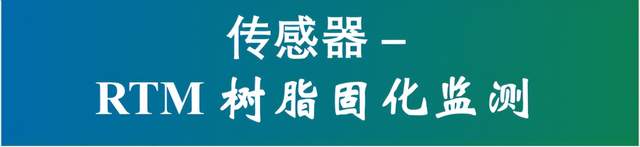
“清洁天空2”中的 INNOTOOL 4.0项目,推进了使用复合材料制造的更大、更便宜的轻型起落架的固化监测。
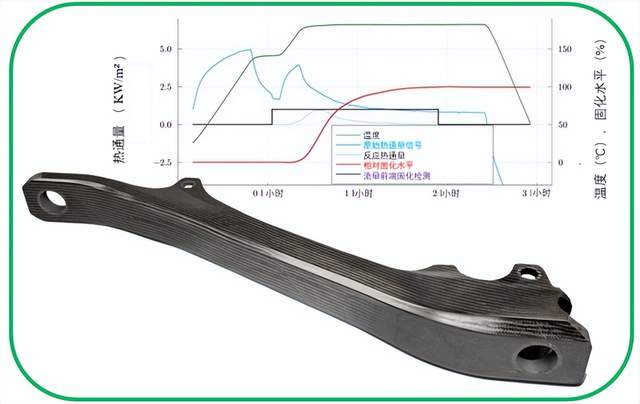
INNOTOOL 4.0演示器的固化监测
顶部的图表显示了TFX热通量传感器数据,该数据用于在INNOTOOL 4.0项目试验期间监测树脂流动和固化,该试验采用了图3中的模具(RTM6树脂,厚度为3.2mm)。该项目的目标是推进基于传感器的固化监测,以降低大型复合材料起落架零件的成本,如这里展示的HECOLAG项目演示器。
起落架占飞机重量的3-5%,长期以来一直是减轻重量以提高飞机效率的目标。随着即将转向节能减排的电力推进系统,这一点变得更加关键。
例如,赛峰起落架系统公司(法国韦利兹)将通过集成在飞机起落架轮中的电动机实现发动机关闭和电动滑行,分别将氮氧化物、二氧化碳、一氧化碳和未燃烧碳氢化合物的排放量减少51%、61%、73%和62%。这对更可持续的航空业来说是一个巨大的胜利,但电动机需要电力,而提供电力所需的电池很重。
因此,对轻型起落架结构的需求似乎非常适合应用复合材料,除了一个问题。GKN福克起落架(荷兰赫尔蒙德)的技术专家皮特·拉乌恩说:“由于起落架是一个单载荷路径结构,结构部件的故障可能会导致严重的紧急着陆情况。”。GKN Fokker起落架十多年来一直致力于证明复合材料起落架结构的技术可行性,包括为F-35闪电II开发碳纤维增强聚合物(CFRP)牵引撑杆。“由于其关键性,起落架结构是商用飞机中最保守的结构之一。”因此,它们大多由高强度金属制成。
然而,这一趋势正在开始转变。“清洁天空2”正在寻求减轻30%的重量,但通过HECOLAG(高效复合材料卷绕装置)项目中的CFRP组件,用于两种应用。在第一次应用中,为A350-1000前起落架的现有铝制上阻力撑杆开发了一种碳纤维增强塑料替代品,该起落架最初由利勃海尔航空航天公司(德国林登堡)开发和制造。HECOLAG的合作伙伴荷兰皇家航空航天中心和GKN Fokker起落架根据利勃海尔的要求设计了这种碳纤维增强塑料阻力撑杆。NLR使用内部开发的自动预成型技术,构建了碳纤维增强塑料阻力撑杆的功能原型,并由GKN福克起落架进行了测试。
在HECOLAG评估的第二个应用中,NLR和GKN福克起落架还与赛峰起落架系统公司合作,为电动主起落架开发了碳纤维增强塑料下侧撑杆。CW将在2021年晚些时候具体报告HECOLAG项目的整体结果,但在这里,重点是INNOTOOL 4.0子项目,由主题经理GKN Fokker起落架指导,利用树脂传递模塑(RTM)推进CFRP起落架结构的高度自动化生产。具体而言,INNOTOOL 4.0旨在展示传感器集成工具,该工具将引领更小的工具、更小的质量、更快的生产周期、更容易的处理和更低的能耗,以及更高的自动化水平,以实现更低的成本和复合材料4.0的智能过程控制。INNOTOOL 4.0项目由欧盟地平线研究和创新计划下的“清洁天空2”联合承诺资助,该计划符合GAP第821261号。
INNOTOOL 4.0目标
拉乌恩解释说,HECOLAG第二部分的演示器(见开篇图)更像是一个通用部分。“它用于演示零件设计、模拟和制造方法,以提供单通道飞机所需的性能、生产率和成本。”到2017年底,HECOLAG联盟已经确定了最初的CFRP演示器零件和生产工具,分析了工具的热行为并进行了性能试验。这个大型复杂的产品通过了初步设计审查,并在当年晚些时候达到了技术准备水平的4级。拉乌恩说:“根据第一台演示机的问题和经验教训,我们正在寻找合作伙伴来开发RTM模具技术,以优化和缩短固化周期。”。2018年发布了《清洁天空2》合作伙伴呼吁,并授予了INNOTOOL 4.0联盟,该联盟由设备和自动化供应商Techni Modul Engineering和树脂注射专家Isojet Equipments(Corbas,France)组成。他们于2019年4月开始工作,并于2021年3月完成了最初的里程碑。
GKN福克起落架的拉乌恩指出:“复合材料部件必须与锻钢和铝具有成本竞争力。”。“这只有在自动化的情况下才有可能实现,与目前的航空航天级热压罐固化CFRP相比,可以实现非常低的工时和更实惠的材料。”
因此,INNOTOOL 4.0试图将传感器集成到RTM模具中,以监测和管理注射和固化过程,包括树脂流动前沿检测。TME的商业总监斯特凡·贝松表示:“我们的目标是实现完全自动化——装载预成型体,按下按钮,成型设备将管理温度、压力、真空和固化。”。然而,这是GKN Fokker起落架和TME首次使用固化监测。“我们以前用过温度和压力传感器,” 贝松说,“但没有用过树脂流动和聚合传感器。”
为什么要使用传感器?
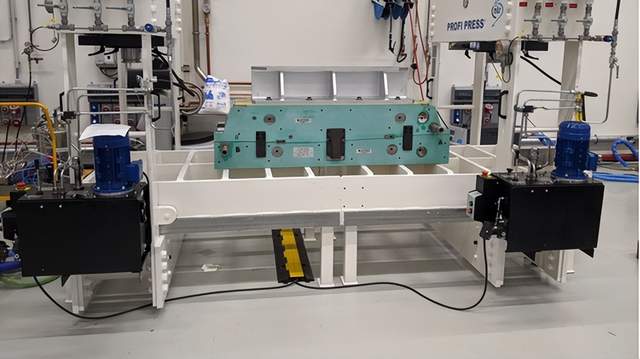
图1. HECOLAG演示生产模具
NLR在2021年3月和4月的零件试验中使用了这个由Techni Modul Engineering制造并配备TFX热通量传感器的生产模具来生产起落架部件演示器(打开图像)。
INNOTOOL 4.0项目的初始里程碑要求TME和Isojet向NLR交付一个配备传感器的成型工具和注射系统,该系统将用于在2021年3月和4月生产演示部件。与此同时,TME将使用现有的工具生产CFRP板,尺寸为600 x 600毫米,厚度为1-8毫米,并使用相同的传感器进行修改,以便在其工厂进行过程控制试验。拉乌恩说:“这是你宁愿第一次在小规模上做的事情,而不是直接在一个高成本的大型工具上做。”。因此,TME使用了不同的工具,但使用了相同的传感器来显示它们的能力和深度。完成此测试后,NLR将重新使用主要的HECOLAG工具来生产新一轮的CFRP演示器,以进一步优化实际零件的过程控制。
RTM生产工具设计
TME开始使用达索系统的CATIA V5软件进行机械和电气设计,并使用ANSYS(美国宾夕法尼亚州卡农斯堡)进行热和机械模拟,从而生产RTM工具设计。该工具将与Isojet的基于活塞的1K-2K(用于单组分和双组分树脂)系统配对,以高达20巴的注射压力注射赫氏(Hexcel-美国康涅狄格州斯坦福德)HexFlow 2K RTM 6和索尔维(Solvay-美国佐治亚州阿尔法利塔)1K PRISM EP 2400单组分航空航天级环氧树脂。
贝松(Besson)指出:“这种成型工具的形状非常复杂,将3D干式预成型件中的不同厚度与封闭的管状形状相结合。这会产生复杂的厚度过渡,涉及预成型件组装、层端精度、内部温度梯度和树脂收缩等问题,以及如何优化内部心轴的加热方法和加热能力以实现较短的循环时间。为了缩短循环时间,工具的所有元件必须易于使用、坚固耐用,并允许快速加热和冷却。”尽管INNOTOOL 4.0项目简要要求非金属模具解决方案,但由于在成型过程中减少皱纹和确保纤维对齐所需的压力,设计了一套典型的上下钢模具。
对匹配的上下模具和心轴进行加热和冷却。贝松(Besson)解释说:“匹配的模具使用一个集成的水回路,同时心轴被电加热。”。“水循环提供快速加热和冷却,以减少零件循环时间,电加热在空间有限的心轴中也实现了同样的效果。”
“另一个挑战是心轴中的零件数量,” 贝松说。“由于形状复杂,需要在成型后拆除心轴,它由六个自加热部件和两个支撑元件组成,传感器穿过这些元件来控制心轴件的内部温度。在使用中,这些元件是在引导操作员的基础支撑的帮助下手工组装的。”使用可充气心轴作为解决方案的工作将在更大的HECOLAG项目中完成,但不包括在INNOTOOL 4.0子项目中。
热通量传感器
TME最初计划使用介电传感器来监测树脂流动和固化(见“结合交流和直流介电测量来监测复合材料的固化”),但改用TFX(瑞士邦科特)的热通量传感器。TME项目经理豪尔赫·洛佩斯-托雷斯解释说:“随着开发的进展,我们希望传感器能够在不直接接触聚合物和复合材料的情况下进行测量。”。“TFX传感器之所以能够实现这一点,是因为它们测量了通过材料传播的热通量。”他指出,这基本上与差示扫描量热法中使用的测量方法相同,DSC是一种分析聚合物或复合材料固化状态的实验室技术。值得注意的是,TFX传感器和DSC测试都测量聚合/固化过程中释放的热量,并得出热通量与温度和时间的关系曲线。
对于TFX传感器,温度数据来自热通量传感器内的内部温度传感器。虽然介电传感器同样配备了内部温度传感器,但这两个传感器非常不同。TFX经理法比安·卡拉(Fabien Cara)博士解释说:“介电传感器直接测量固化过程中的聚合物性能。”。“热通量传感器不会给出材料在给定时刻的状态。然而,测量树脂流动和聚合过程中产生的热量可以很好地了解过程的行为以及每个生产零件的固化周期的可重复性。与DSC一样,我们需要看到固化过程的整个曲线,但我们监测固化的能力非常可靠。
数十年的经验
TFX传感器成立于2000年,原名Thermoflux,已被全球100多家客户用于研发中心的试验和工业应用。卡拉说:“我们15年前就开始使用RTM,首先是与宝马合作生产汽车零件,然后是现在被称为Soudure研究所(法国圣阿瓦尔德)的技术中心。2006年和2012年,我们启动了两个大型项目,用于监测使用RTM和3D编织预成型件制造的飞机发动机风扇叶片的固化情况。赛峰集团在巴黎附近的复合材料实验室为他们开发了一个数据采集系统。他们可以同时记录多达100个信号(热通量、温度和压力),并分析这些信号以进行固化和监测工艺周期。”TFX还与法国Les Avenières的Hexcel实验室合作,监测质量和加工过程。将热固性树脂注入干燥的预成型件中。TFX传感器还用于与IRT-M2P(法国Porcelote)合作的一个项目,以演示Compression RTM。卡拉指出:“我们的传感器对于压缩成型等快速工艺非常有效,包括SMC和BMC模塑料。”。“2016年,我们还获得了亨斯迈先进材料公司(瑞士巴塞尔)颁发的JEC创新奖,该公司开发了一项名为“在不到1分钟内达到热压罐质量的结构环氧零件”的产品。”
TFX为每种类型的复合材料成型过程都配备了传感器,基于传感器的传热方法:传导(RTM、压缩和注塑)、对流(热压罐、烤箱)和辐射(纤维缠绕、AFP)。INNOTOOL 4.0项目中使用的传感器是导电的,设计用于嵌入金属RTM模具中。卡拉指出:“它们在距离工具表面和复合材料高达1毫米的地方提供了一种异常可重复的信号。”。
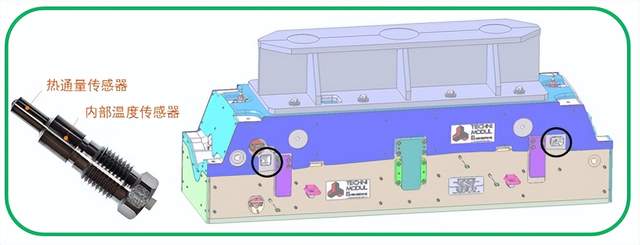
图2. RTM生产工具传感器
两个TFX-191传感器被集成到交付给NLR的RTM生产工具集的上模中。
TME在匹配的生产工具集的上模中安装了两个TFX-191传感器,一个位于树脂入口,一个在树脂出口,然后将其发送到NLR(图1,2)。NLR在2021年3月和4月使用该生产工具制造了HECOLAG演示器零件。TFX-191传感器适用于厚金属工具。
同时,TME采用了一种较小的内部工具来制作CFRP板样品,并用两个TFX-224传感器对其进行了修改,这两个传感器更短,适用于更薄的工具(图3)。然后,根据上述INNOTOOL 4.0目标,使用该RTM板工具集进行传感器演示试验。卡拉说:“这些传感器与我们用于赛峰集团的传感器相似,但现在经过改进,变得更加紧凑和灵敏。”传感器被放置在零件中心和树脂出口附近。除了热通量传感器外,TFX还开发并提供了两个数据采集系统,一个交付给Isojet,另一个由TME用于CFRP板试验。
这两个传感器更短,适用于更薄的工具(图3)。然后,根据上述INNOTOOL 4.0目标,使用该RTM板工具集进行传感器演示试验。卡拉说:“这些传感器与我们用于赛峰集团的传感器相似,但现在经过改进,变得更加紧凑和灵敏。”传感器被放置在零件中心和树脂出口附近。除了热通量传感器外,TFX还开发并提供了两个数据采集系统,一个交付给Isojet,另一个由TME用于CFRP板试验。
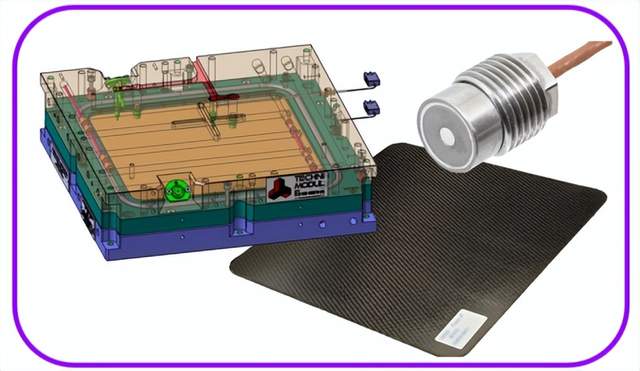
图3. 板材工具试验
两个TFX-224传感器(右上)被集成到TME匹配的金属RTM工具集(左上)的上模中,以评估在不同树脂、固化时间和零件厚度的CFRP板(右下)试验期间的传感器性能。
INNOTOOL 4.0测试结果
TME使用其用TFX传感器改装的板材工具进行的试验测试了两种不同的基材树脂—HexFlow RTM 6和PRISM EP 2400—以及零件厚度和整体固化时间的影响。卡拉说:“传感器提供了很好的信号来监测固化周期。”。“然后,研究小组分析了固化曲线,并表明RTM 6的固化时间可以比规定的两小时固化时间缩短至少30分钟。”
这可以在下面的曲线中看到,其中t=0小时是注射的开始时间。注意,固化时间从温度达到180°C开始,固化结束对应于相对固化水平的99%(见右侧的垂直轴)。固化结束也与原始热通量稳定相吻合。
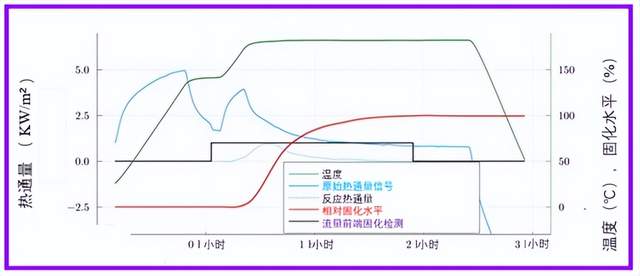
热通量传感器数据,缩短固化时间
这条曲线(也显示在开头的图像中)显示了TME使用图3中的模具生产CFRP板的一次试验中的TFX热通量传感器数据,该试验使用RTM 6树脂生产3.2mm厚的CFRP板。参考时间t=0小时对应于注射序列的开始(将树脂进料管线填充到模具中)。固化时间是在温度达到180°C时计算的,而固化结束对应于相对固化水平的99%(见右侧的垂直轴)。对于这项试验,固化结束发生在规定的2小时固化周期前30分钟。这也与原始热通量稳定相吻合。
这通过使用动态力学分析(DMA- dynamic mechanical analysis)对脱模零件的固化状态进行测量得到了验证,DMA是DSC-differential scanning calorimetry(差示扫描量热法)的一种替代实验室技术,用于测量复合材料的玻璃化转变温度(Tg)。他补充道:“DMA结果证实,对于RTM 6树脂,在180°C下固化90分钟后,Tg保持不变。”。
还研究了厚度的影响。卡拉指出:“TME在传感器演示试验中测试的第一块CFRP板厚度不到2毫米。”。“这些板材还具有高纤维体积(50-60%)和缓慢的固化周期,以防止放热和热应力和零件质量的潜在问题。所有这些对于航空航天零件来说都是非常正常的,但这意味着树脂很少,因此树脂反应释放的热通量很小。因此,我们实际上是在加热工具和零件的海洋中寻找树脂固化产生的热通量。”
换句话说,正如卡拉所解释的那样,“大多数航空航天RTM固化周期都涉及在一个温度下注入树脂,然后在第二个更高的温度下逐渐固化。因此,当你完成注射时,你会将工具加热到固化温度,这会在整个系统中产生很大的热通量。”然而,与DSC测试一样,用热通量传感器监测固化的关键是测量聚合/固化过程中释放的热量,并在热通量与成型系统和时间的温度曲线中显示这些测量值。“因此,我们发明了一种方法,可以帮助我们减去加热模具的基线,以及热量向零件的传导,从而可以确定树脂反应的热通量。”
因此,卡拉说,尽管初始薄板中的工艺条件非常具有挑战性,“我们仍然可以看到树脂反应的热通量。然而,通过制造更厚的零件,我们能够根据零件厚度准确地看到热通量水平的差异,这验证了我们在薄零件中的固化监测。”注意,上述曲线(也显示在开幕照片中)是在3.2毫米厚的板中使用RTM 6树脂获得的。
然而,树脂流动前沿检测的结果存在更多问题。卡拉说:“对于出口附近的传感器,我们可以很好地看到流动,但对于中心附近的传感器则不然,因为树脂到达得很晚。”。“使用热通量传感器进行流前检测需要树脂流在局部热场中产生变化。当树脂与预成型件的温度不同时,就会发生这种情况。”他指出,ΔT大于0.1°C就足以进行检测。“然而,在薄CFRP板试验中,模具中的温度非常均匀,树脂到达的速度非常慢。因此,热对比不足以检测树脂到达与整个系统中的热噪声。然而,由于流道有助于产生更大的热对比,更容易检测和监测,树脂到达出口的速度更快。”。
卡拉建议,TFX开发的新型有源传感器可以改善这种树脂流动前沿监测,该传感器在传感器内使用集成加热功能。他解释说:“这使得传感器能够帮助在固有困难的零件和工艺中提供必要的热对比。”。
扩展复合过程控制能力
托瑞斯说:“我们对迄今为止完成的工作感到满意,但这只是第一步。我们的目标是使用这些热通量传感器来管理生产环境中的复合材料加工。”卡拉说,这是可能的,因为传感器系统会根据树脂的到达自动向注射设备发送信号,并根据固化曲线的零斜率自动向压机发送信号。托瑞斯补充说,TME为注塑机和RTM压机配备了过程控制系统,可以管理温度和压力。“下一步,”他说,“是将TFX传感器集成到这些控制系统中,并从笔记本电脑管理整个过程。”卡拉指出,TFX传感器和数据采集也与压力传感器(例如瑞士温特图尔的Kistler)配合使用,以帮助实现这一整体过程控制,他的公司正在开发一种传感器,可以在单个集成设备中测量热通量、温度和压力。
但是,这种过程控制负担得起吗?卡拉表示,监控系统的初始投资10-3万美元通常会在开发阶段获得回报,通过改进流程和零件理解来减少试错。“然后,该系统继续在生产过程中节省成本,缩短周期时间,确保可重复性,并提供对漂移或不合格的早期检测。”
在GKN Fokker,拉乌恩认为,一旦减少周期时间和提高成本的能力得到证实,“那么就有可能想象复合材料不仅可以用于INNOTOOL 4.0和HECOLAG项目中展示的起落架部件类型,还可以用于所有类型的零件。这将开辟我们的设计空间,使我们能够进一步突破轻型起落架的界限。” 贝松看到了更广泛的应用:“这种过程控制可以为各种模具和复合材料零件开发。”
编后语
最近发出的《传感器-AFP的感知固结辊》、《传感器-用于下一代复材制造》和《传感器-RTM树脂固化监测》的三篇短文,其中后两篇的原文是由同仁—香港科技大学的庆浩,复制发给我的。
在此特别说明并表示感谢!
原文,《Speeding RTM with heat-flux sensors》 2021.6.28
杨超凡 2025.7.19