在探讨氢能产业的时候,我们的反应是燃料电池,第二反应是氢气,连接这两者之间重要的就是储运装置,其中通用的装置就是压力容器(包括车载储氢瓶和高压管束),其在氢能中发挥着非常重要的作用,而高强度、轻量化的碳纤维则是氢气储运的关键材料。
微米级的有机纤维在惰性气体中进行高温碳化,分离掉碳以外的元素就变成了碳纤维。碳纤维只有铁1/4的重量,却有铁9倍的强度,具有低密度、高强度、耐高温、高化学稳定性、抗疲劳、耐磨擦等优异的基本物理及化学性能。这些性能对于要求抗高压和减重的氢气瓶来说具有非常高的匹配度,碳纤维的应用也是燃料电池汽车得以实现高续航里程和较高能效比的一个条件。
本期文章就从碳纤维的发展历史来看看氢能产业链上这个细分业务的情况。
01远久的访客正在变成时代的主人
有一种”时代“是用材料来定义的,比如”石器时代“、”青铜器时代“、”铁器时代“……,我们是不是会走向一个叫“碳纤维”或“复合材料”的时代?不过,材料时代的更迭是如此漫长……,这个上,很早就有碳纤维,只是很久以来,它像一个“客人”,直到60年前,在材料的家族里才开始有了它的位置,不过过去的60年它一直是一个“贵族”,不那么亲民,现在它正在慢慢走近更多的人,覆盖更大的市场……
我们先用数字来简单定义一下碳纤维产业的发展阶段吧:
从0到1:从没有到有的过程,即从理论上的论证到实物的形成。
从1到10:从实验室到商业化产品的过程,产品形成并能够在局部领域的应用。这一阶段解决的是产品的功能问题。
从10到100:从局部应用到广泛应用的过程,这一阶段解决的是产品的成本问题。
和很多研项目的发展历程一样,碳纤维也是率先在军用航空领域应用,然后进入大规模生产降低成本向民用工业领域渗透。
(1) 从0到1,经历了近百年
碳纤维的起源可追溯到19世纪60年代,1860年,英国化学家、物理学家约瑟夫·威尔森·斯万爵士(Sir Joseph Wilson Swan,1828–1914)发明了一盏以碳纸条为发光体的半真空电灯,也就是碳纤维白炽灯的原型,比爱迪生还要早,但碳纤维灯泡并没有使用很久,就被钨丝取代了。19世纪70年代末,真空技术已渐成熟,斯万发明了更实用的白炽灯,并于1878年获得了权。
1879年,爱迪生(Thomas Alva Edison,1847-1931)发明了以碳纤维为发光体的白炽灯。1892年,爱迪生发明的“白炽灯泡碳纤维长灯丝制造技术(Manufacturing of Filamentsfor Incandescent Electric Lamp)”获得了美国。可以说,爱迪生发明了早商业化的碳纤维。
由于当时碳纤维的原料源于天然纤维,几乎没有结构强力,使用中很容易碎裂、折断,即便只是作为白炽灯的灯丝,其耐用性也不够。到1910年左右,钨丝替代了早期的碳纤维灯丝。
尽管如此,在爱迪生发明碳纤维后的30多年里,对改进碳纤维性能的研究从未停止过。然而,这些努力都未能把碳纤维性能提高到令人满意的程度。此后,在相当长的时间里,碳纤维的性能几乎停滞不前,研究处于休眠期。
直到上世纪50年代中期,因为人造纤维化学纤维的出现,特别是聚丙烯腈的发明,才使得碳纤维的性能得以提高。杜邦公司1942年发明了聚丙烯腈(PAN)纤维技术,1950年开始生产销售奥伦品牌的PAN纤维。
也就是说,从1960年到约瑟夫·威尔森·斯万发明碳纤维灯丝到杜邦公司生产PAN纤维,这个过程经历了近百年。
(2)从1到10,体育休闲和航空航天是大的驱动力
PAN基碳纤维突出的性能是力学强度(mechanical strength)和弹性模量(tensile modulus),目前,PAN基碳纤维占据主导地位,在市场上占据90%的市场份额。
1962年,威廉姆?F?阿博特(WilliamF. Abbott)发明的碳化人造纤维提高碳纤维性能的方法被美国授权。该是阿博特作为委托人替位于美国加利福尼亚州奥海镇的卡本乌尔公司申请的,后来被转让给了美国巴尼比-切尼公司(Barnebey-Cheney Company)。
巴尼比-切尼公司1957年便开始了商业化生产棉基或人造丝基碳纤维复丝,但其只能用来生产绳、垫和絮等产品,用于耐高温、耐腐蚀等用途;其可独立用作吸附用活性炭纤维。自获得阿博特的碳纤维后,高性能碳纤维基础科学研究和工业化技术研发进入了高峰期。
上世纪50年代-70年代,美国深陷朝鲜和越南战争泥潭,而彼时的日本政府则正改邪归正,积极营造和平、奋进的发展环境,实施“产学官”等创新政策,引导全社会为经济复苏做贡献,进入科研产业化的发展时代。
表 碳纤科学家主要贡献
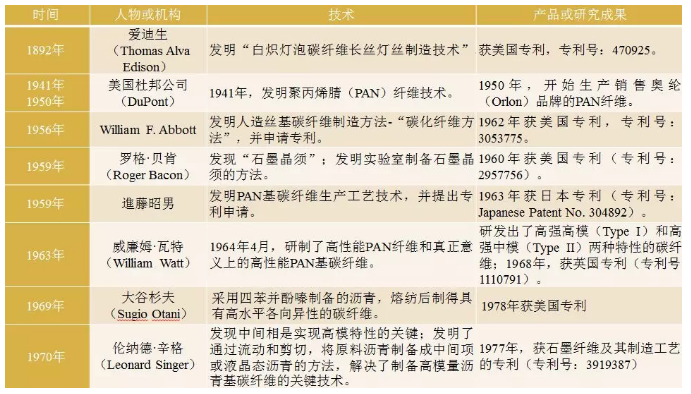
成立于1918 年的日本政府大阪工业技术试验所(Government Industrial Research Institute,GIRIO)率先开启碳纤维的研究,1959年,大阪工业技术试验所的青年科学家進藤昭男(Akio Shindo)开始了碳纤维研究。
大阪工业技术试验所与企业交流频密,知识和技术转移迅速,1959年、1970年,东海碳素公司(Tokai Electrode Mfg. Co.,Ltd.)、日本碳素公司(Nippon Carbon Co., Ltd.)和东丽公司(Toray Industries,Inc.)分别获得了该所PAN基碳纤维技术的授权。
不过,东海碳素公司和碳素公司未能在短时间内生产出合格的PAN 基碳纤维,直到1968年,东海碳素公司才开始商业化生产“Thermolon S”品牌的碳纤维。1969年日本碳素公司月产500kg碳纤维的中试装置才开始运转。日本东邦人造丝公司(Toho Rayon Co., Ltd.)和三菱人造丝公司(Mitsubishi Rayon Co.Ltd.)也分别于1975年、1983年开始生产碳纤维。
1970年6月,东丽公司[Toray Industries(Toray)]获得了大阪工业技术试验所的授权,并收购了东海碳素公司和日本碳素公司的相关生产技术;同年,还与美国联合碳化物公司(Union Carbide Corporation)签署了前驱体PAN纤维技术与碳化技术的互换协议。1971年2月,东丽公司月产1 t级的PAN基碳纤维中试生产线开始运转;同年7月,Torayca?品牌的碳纤维上市销售。
20世纪60年代中期,英国皇家飞机研究中心(RAE)的威廉姆·瓦特(William Watt)早解决了前驱体PAN纤维共聚单体的内部结构缺陷和除杂纺丝等问题,发明了真正意义上的高强高模PAN 基碳纤维。瓦特曾向美、日转让了前驱体PAN 纤维技术,东丽公司在進藤昭男和瓦特的研究基础上,经过持续的技术创新和工程实践探索终取得成功。
一开始,碳纤维企业都将目标锁定在美国的军用市场,但东丽公司是在体育市场实现突破的。成立于1972年的美国阿尔笛拉公司是上个开发生产商业化碳纤维高尔夫球杆的公司。东丽得知碳纤维可以应用在高尔夫球杆中,转而将目光瞄准体育休闲领域,于是他们个批量化碳纤维产品就是鱼竿。
这个的很多事情似乎都与能源有关,在20世纪70年代后半期,随着1973年、1974年石油危机的爆发,民用飞机制造商波音和空客开始寻找重量轻的增强材料来减少油耗,美国政府赞助航空公司(波音、道格拉斯(后为麦道)和洛克希德)启动了持续数十年民机使用碳纤维复合材料应用的计划,1975年实现碳纤维在波音737次承力结构的应用则推动了东丽千吨级的量产。
与此同时,美国联合碳化物公司放弃了自己生产原丝,成为东丽的碳纤维美国市场的代理商,T300得以在航空领域应用。1987年波音与联合碳化物公司合作到期,东丽公司可以越过中间商在美国直销碳纤维。1987年,东丽的T300获准在空客A320主承力部件中应用。1990年,一种新的高强高模碳纤维预浸料在波音777飞机的主承力部件上获得应用。
从20世纪90年代中期,碳纤维的消费量以每年15%的速率增长。民用航空仍然是主要的市场,尤其是高等级的碳纤维。波音和空客相继推出787和A350,新机型均采用碳纤维复合材料作为主承力部件,碳纤维复合材料用量达到50%。
东丽的产业化之路始终与波音公司紧密捆绑在一起,碳纤维的发展离不开波音飞机复合材料结构的批量化生产。现在,东丽有几百名工程师长期在波音,与他们联合开发碳纤维材料的应用,依然占据着波音材料供应商的主导地位。
东丽的碳纤维之路起步于1970年,东丽实现碳纤维量产(十吨级)起步于开发出了钓鱼竿和高尔夫球杆的批量生产;2009年起波音787机体结构50%重量使用碳纤维则推动东丽万吨级的量产,这是碳纤维批量应用的一个转折点,也使得东丽发展了30多年的碳纤维业务实现稳定的盈利。日本东丽公司碳纤维业务重要的时间节点:
1961年:开始关注无机纤维树脂增强体的研究发展;
1970年:PAN基碳纤维产业化技术研发成功;
1971年:1吨/月试验线建成,Torayca品牌产品销售;
1973年:5吨/月生产线建成投产;
1990年:预浸料次被认证为波音777飞机机尾主承力结构部件的原材料;
1992年:在美国建立预浸料工厂;
1997年:在美国建立原丝工厂;
2011年:被用于包括主翼在内的波音787飞机主承力结构的制造。
(3)从10到100,“低成本技术”+“新能源市场”成为碳纤维工业应用的驱动力
直到本世纪的头10年,碳纤维大的应用市场还是航空航天和体育用品,其良好的性能对应的是高昂的价格,将这个素有"黑色黄金“之称的碳纤维的应用只能局限于”奢侈行业“,作为材料,它没有像石器、青铜器、铁器那样能够普及,所以,直到现在,即使是的行业龙头,美国赫氏的营业收入也仅仅是20多亿美元;东丽工业营业规模达到200亿美元,但其碳纤维收入到2020年也只有21.92亿美元。
显然,这不是一个具有诱惑力的市场规模,但它的性能和预期的前景又如此具有诱惑力,对于在碳纤维产业化几十年投入的企业来说,一定不会局限在"特殊”领域的应用。所以,碳纤维一条路线是提高材料的性能,另一条路线则是通过工艺降低成本。
而降低成本的路线又包括产品和工艺两条路线,“提束”或“提速”:
产品路线(“提束”):大丝束。所谓“提束”即通过提高碳纤维丝束量来降低碳化过程中的工艺难度和设备成本。
碳纤维的丝束大小以K来计量划分,1K的意思是一束碳纤维中有一千根碳纤维原丝,24K表示一束有两万四千根碳纤维原丝,大丝束碳纤维是指每束碳纤维的根数为24k以上的碳纤维(现在提高到40K)。大丝束碳纤维的性能较小丝束碳纤维有所降低,为通用级碳纤维,用于一般工业制品。
美国能源局一直致力于低成本新型碳纤维研发和商业化,到2018年,在小丝束碳纤维市场上,日本企业所占有的市场份额占到产能的49%;在大丝束碳纤维市场,美国赫氏占据绝对优势,市场份额高达58%;其次是德国西格里,占比31%;日本三菱排在第三,占比9%;这三家企业占据了大丝束碳纤维市场份额的98%,其他企业仅占剩余的2%。
卓尔泰克(ZOLTEK)公司是美国低成本新型碳纤维研发和商业化项目(2013年6月-2015年6月)的受益者。面对汽车领域轻量化的需求东丽通过收购ZOLTEK的同时实现规模化和低成本。
2018年,用于飞机结构上的3K碳纤维国际售价约USD50/kg 左右,国内售价约为800~900元/kg。而美国卓尔泰克48K大丝束碳纤维,国际售价仅为USD 12~15/kg,而国内售价为150元/kg,大约只相当于小丝束碳纤维价格的20~40%。
德国SGI.集团生产的牌号为C30 T050的大丝束碳纤维,性能与T300相当,而成本只有其1/4。
总体来看,大丝束碳纤维的生产相对于小丝束来说成本要低很多,其售价只有小丝束碳纤维的50%-60%。性能价格比(单位价格的强度、模量、比强度和比模量)远高于小丝束碳纤维。
工艺路线("提速"):干喷湿纺。可以将原丝线速提高5倍。
“干喷湿纺”是一种碳纤维原丝制备工艺,是相对“湿喷湿纺”而言的。湿喷湿纺是指纺丝液经喷丝孔喷出后直接进入凝固浴进行双扩散、相分离和形成丝条的方法;干喷湿纺是指纺丝液经喷丝孔喷出后,先经过空气层,再进入凝固浴进行双扩散、相分离和形成丝条的方法,经过空气层发生的物理变化有利于形成细特化、致密化和均质化的丝条。
干喷湿纺的难度非常高,但可以大大提高原丝线速,如湿纺工艺原丝线速80-100米/分钟,采用干喷湿纺可以提高到300-500米/分钟,预氧化时间也由原来的60分钟缩短为35分钟,氧化炉也比原来减少了一个。
日本东丽表示,他们采用干喷湿纺生产T700既提高了效率、降低了成本,又实现了纤维性能的提升。
林刚在《2020碳纤维复合材料市场报告》中描述:“碳纤维的应用曾经是以航空航天为主驱动的,这些年,已经变成了航空航天驱动与工业用驱动的双引擎驱动模式。这对全碳纤维的产业格局已经形成了深刻的变化。就在短短的几年前,大丝束碳纤维企业还在为生存而挣扎,这两年,大丝束成了市场的香饽饽。”
有意思的是,所有的人几乎都将低成本的碳纤维市场的目标放在材料应用多的汽车领域,这固然与汽车的减重和节能需求有关,但实际上,近拉动大丝束碳纤维的恰恰又是新能源,其中风电叶片、储氢瓶和光伏产业晶硅熔炼炉成为大的驱动力。
在这一背景下,这类企业迅速成长 ,比如卓尔泰克的一万吨产能的扩建仅仅用了三年不到的时间,依然供不应求,而且效益也很好,另外由于较低成本,它具有吞噬部分传统小丝束市场的能力,比如国际上已经开始用大丝束缠绕大型气瓶, 提升缠绕效率;国内不少厂家采用大丝束制造低成本预浸料。
西格里与卓尔泰克的预氧丝采用 300-320K 制备,这个预氧丝被加工成预氧毡,再加工成碳毡,有着越来越广阔的市场应用;其中,也有部分巨丝束被直接制备为碳纤维,作为碳毡的原料,进入了刹车片的功能化市场。
小丝束 Small Tow(或常规丝束 Regular Tow)1-24K(含)
大丝束 Heavy Tow:大于等于 48K (东丽的定义是大于 40K)
巨丝束 Giant Tow:大于 100K
资料来源:林刚《2020碳纤维复合材料市场报告》
2019 年大丝束占比 42.2%, 2020 年因新冠疫情对航空领域的影响和风电市场的增长,大丝束产品继续快速提升市场份额到 48.3%,不过,林刚认为,今后三年时间,大丝束的市场份额扩大的趋势还会增加。
林刚在《2020碳纤维复合材料市场报告》中预测,今后 3-5 年,是低成本大丝束碳纤维发展的黄金年份,数万吨的碳纤维的产能将供应市场。而增长快的市场将来自风电叶片、压力容器和碳碳复材。
其中,压力容器市场增长的主要驱动力是氢能及燃料电池汽车的发展,按照各国对氢能及燃料电池汽车的规划,预计到2025年,燃料电池汽车产量将超过10万辆,如果按照平均每辆车5个气瓶计算,仅氢气瓶带来的需求就将达到25000吨;而碳碳复合材料的主要驱动力则来自光伏产业,光伏产业中所使用的碳碳复合材料主要是用于制造坩埚,作为熔炼多晶硅或单晶硅的器皿,在氢化炉热场、直拉单晶热场、多晶铸锭炉热场、太阳能电池镀膜等工艺作为关键设备。
02碳纤维的复兴之路
碳纤维起步并不比主要碳纤维生产国晚太多,只是和大飞机一样,改革开放反倒因为引进技术而中断了国产化进程,而长期以来的技术封锁,让我们不得不再次起航。目前,碳纤维已经走过了情怀时代,进入经济和成本时代。
(1)及早起步,中道停滞
PAN碳纤维产业化的起点是1959年,用聚丙烯腈为原料生产碳纤维的研究始于1962年,这个起点比发达并不算太晚。
1962年,中科院长春应用化学研究所和沈阳金属所成立以李仍元为组长的“聚丙烯腈基碳纤维的研制”课题组,开始碳纤维的基础研究。
1970年代初,中科院化学所组建高分子复合材料物理研究室,重点研究“碳纤维连续化制备”和“缩短碳纤维制备周期研究”并取得“四氯化锡”催化等成果。
1972年,化工部吉林化工研究院开展硝酸法研制碳纤维PAN原丝,并在年产3吨装置上取得硝酸一步法制取原丝,供山西燃化所和长春应化所研究碳纤维。山西燃化所以间接预氧化和碳化研究,并开展连续预氧化和碳化试验。
1970年代初,上海合成纤维研究所开展硫氰酸钠法丙烯腈原丝研究,1975年提供给冶金部上海碳素厂2吨原丝研制碳纤维。
我国碳纤维历史上著名的一次产业会议是1975年时任国防科工委主任张爱萍主持召开的专题会议,部署国内碳纤维研究工作,由计委安排500万元资金做启动费,并制定了10年发展规划,组织了原丝、碳化、结构材料、防热材料、测试检验技术5个 “攻关组” ,安排20多家研究和企业单位参加,由吉林化学工业公司研究院、吉林辽源石油化工厂、兰州化学工业公司化纤厂、上海合成纤维研究所采用不同溶剂路线研发聚丙烯睛(PAN)原丝,上海合成纤维研究所、吉林、上海、兰州、抚顺4家碳素厂、山西燃化所、中科院化学所等负责碳化技术研究,另外还安排了织物和材料应用研究。这就是碳纤维行业史上著名的“7511”会议。
从1975至1981年底,各部委共投入到承担碳纤维原丝、碳纤维制品等项目资金约2600多万元,共建设厂房、试验室20000多平方米。建成PAN原丝试制动力约50t/a,碳纤维长丝的试制能力1.5~2.0t/a,大体满足了国防急需,但质量和成本都远不及国外。
而这一阶段恰好是国外碳纤维技术突飞猛进的时期,改革开放后的80年代中期,科委鼓励引进国外先进技术,但受制于 “巴黎统筹条约” ,各知名碳纤维公司均不转让技术、不出售设备,只有一些不知名的小公司愿意将设备卖给,其结果是两套进口设备都未能正常运转,几千万买入的进口设备变成了“废铜烂铁”。
一连串的失利严重挫伤了各方面的信心,各部门在20世纪后期的10多年内都不愿或不敢大量投资,使碳纤维研发成为一块令人望而生畏的“烫手山芋”。
(2)院士呼吁,民企突破
到2000年,就在碳纤维产业低迷的时候,国内只有吉化公司、吉林碳素厂和北京化工学院还在 “惨淡经营” ,维持小批量供货,其他研发单位基本退出了这一领域。
这时,上世纪50年代从美国留学回国的材料科学家、科学院、工程院院士师昌绪关注到碳纤维产业,他意识到的碳纤维上不去,影响国防科技和高新技术发展,关系到安全。因此,80岁的师先生开始推动重启碳纤维项目。
2001年师先生给江泽民总书记写了一封信: “关于加速开发高性能碳纤维的请示报告” ,并通过两会代表将信转上去,他说,芯片和碳纤维对国防发展非常重要,他想抓一抓碳纤维。
2001年10月科技部决定设立碳纤维专项;2003年1月17日,自然科学基金委员会批准碳纤维2个重点项目;2005年碳纤维项目被批准为重大基础研究项目(九七三项目)。
与此同时,在的威海,一个倔强的农民企业家正带领他的团队夜以继日地研发碳纤维——他就是光威集团创始人陈光威,因为公司生产的钓鱼竿需要进口碳纤维,价格和供货周期都受到限制,所以,他决定自己生产碳纤维。1999年,陈光威请来原吉林石化公司研究院总工程师陈光大,他们投入100万美元,用一年的时间完成了碳纤维试验线的调试,并生产出高强碳纤维的样品。
2001年,陈光威秘密创建原丝开发部,2002年,光威成立威海拓展纤维有限公司。2002年,光威有机会参加由师昌绪主导的碳纤维研讨会,并在2003年迎来光威碳纤维的“大考”,这几乎代表着碳纤维产业化的一次大考,2003年光威在6家企业提供的样品盲测中脱颖而出。
2005年,光威拓展承接的两项“863”碳纤维专项通过鉴定,并建成国内条T300百吨生产线,同年,启动国产碳纤维航天航空的实验研究。
师昌绪启动的项目和光威的成功重启了碳纤维的信心,2006年-2008年,中复神鹰、江苏恒神、中简科技、吉林碳谷等数十家碳纤维企业相继成立,国内涌现一批“碳纤维报国”的企业。
这些企业都不是无本之源,他们都与上世纪70年代我国碳纤维研究基础有关,其中吉林化学研究所和山西煤化所是重点,要么是原有团队重启项目,要么是这些科研单位的专家与资本组建实体。至此,我国碳纤维行业走上了复兴之路。
(3)技术降成本,产能大扩张
很多科技都是从军品开始的,但军工行业毕竟是小市场,规模化应用还是要依靠民用工业市场。但民用市场大的障碍是成本,也就是说,如果要在民用市场广泛应用,就必须走降低成本的路线。
一部分企业走不下去退出了市场,还有一部分企业选择攻克降低成本的技术难关:干喷湿法工艺或大丝束产品。
其中,中复神鹰就放弃了湿纺工艺,专攻干喷湿纺并取得突破。公司“干喷湿纺千吨级高强/百吨级中模碳纤维产业化关键技术及应用”项目荣获2017年科技进步一等奖。该项目填补了国内以干喷湿纺工艺为代表的高性能碳纤维生产技术的空白,打破了国外高性能碳纤维企业在市场的长期垄断,降低工艺成本,扩展了碳纤维的应用领域。
另外,秉承吉林化学研究所科研体系的吉林碳谷则用晴纶技术在原丝上攻关。2018年浙江精功和吉林碳谷联合攻关,由光威复材提供上浆剂,2020年在大丝束碳化上获得突破,可以在风电叶片的碳梁上应用。再次为碳纤维的民用化创造了条件。
从范围来看,大丝束是在2015年、2016年以后发展起来的一条技术路径,国外美国ZOLTEK和德国的SGL是大丝束企业的代表,国内则以吉林碳谷为代表,而他们一个共同的特点就是拥有腈纶纺织技术的基础。
而光威复材早在2014年就以自有资金投入参与风电碳梁产品的开发,从2016年第四季度光威便开始为塔斯维斯提供碳梁,进入批量生产,目前,光威碳梁业务占全部收入的30%以上。
我们关注到,在国内“两公一民”的碳钎维龙头企业中,带有“吉化”、“煤化”等研究院基因的企业更多是从工艺和产品技术路线上的突破,如吉林碳谷和中简科技,中复神鹰的董事长张国良也带有很深的装备研发基因;而民营企业光威复材的基因是从市场出发的,其对市场的变化更加敏感,他们不仅提前布局风电叶片,到2020年从五大客户中已经可以看见中材科技的名单,表明他们已经在气瓶领域开始布局。
台塑本是一家历史悠久的优秀碳纤维公司,然而近十年技术没有明显的进步,一直处于亏损中,前几年关闭了其腈纶装置,失去了发展低成本碳纤维的基础。
恒神公司也在技术上投入很多,但由于其选择全产业链战略,从碳纤维(包括织物)—中间产品(树脂和预浸料)—复合材料产品开发技术服务(包括设计分析、成型工艺与制造)一条龙服务。这种商业模式对东丽这样的综合型大企业来说可以养得起,但对创业型企业来说是难以承受的,所以,恒神股份巨大的资产负担导致公司无法盈利,目前已经被陕西化工集团收购。
2011年中安信在廊坊成立,全套进口碳纤维设备,2013年被康得新收购,但因为康得新财务造假项目搁置,目前处于重组中;隶属于化工集团的兰州蓝星纤维有限公司,成立于2008年,碳纤维产能3100吨/年。原丝技术来源于2007年蓝星(集团)总公司全资收购的英国老牌碳纤维生产企业,也是早引进英国技术的企业,至今都有一些消化不良。
碳纤维是一个涉及战略和基础工业的重要产业,而且投入比较大,目前处于技术趋于成熟,方向明确的阶段,企业如上海石化、宝武集团、太钢股份、建材等都在拓展碳纤维产能。
03碳纤维市场的供求关系与发展趋势
到2019年,也就是碳纤维产业化60周年时,碳纤维需求次突破10万吨到10.37万吨, 林刚在《2020碳纤维复合材料市场报告》中预测,到2025年碳纤维需求将达到20万吨。也就是说,从1959年到2019年,个10万吨经历了60年,预计下一个10万吨仅需要6年!
趋势一:从情怀时代到效益时代,应用领域工业化
改革开放前,我国碳纤维一直都处于产业化研究阶段,是由科研机构主导的。2000年师昌绪院士呼吁发展碳纤维的初心是出于国防安全的考虑,他说:“如果碳纤维研发止步不前,国防安全就无保障,我将死不瞑目。”
如果说陈光威一开始研发碳纤维的动机是为了解决钓鱼竿的供应链瓶颈的话,那么,后来成就光威集团“发扬威海精神,创建碳纤维基地”(师昌绪)就是他的报国情怀了,自2000年起,陈光威为了攻克碳纤维难关,为了航空验证,先后投入30多亿,将房子都做了抵押。
在师昌绪院士的引领和光威初见成效的吸引下,自2006年,国内一批企业怀着报国的激情进入到碳纤维行业。
国防事业固然非常重要,但毕竟是一个小市场,而且航空的产品验证需要十年,是一个优中选优的产业生态,如果挤在这个赛道,更多的企业将被淘汰,只有进入到民用大市场才有更大的市场空间。中复神鹰、吉林碳谷就是这条路线的成功者,他们通过“提速”或“提束”将碳纤维推向更加广阔的民用市场。
从国际市场碳纤维需求量与需求金额比较来看,2020年需求量大的是风电叶片,而需求金额高的是航空航天,两个领域的碳纤维价格相差4.29倍。但在新冠疫情影响下,航空航天需求出现大幅下降,恰恰是风电、压力容器等工业领域支撑了整个市场的增长。
从树脂基碳纤维复合材料的单价来看,航空航天的价格更是像它产品的验证周期一样,十倍于民用工业领域,但同样,未来民用市场的空间,特别是当碳纤维实现规模化和买方市场后,工业用途将成为大的驱动力。
行业专家预计,到 2030 年,航空航天市场:8-10 万吨;风电:19-20 万吨;氢气瓶及 CNG 气瓶:18 万 吨;汽车+轨道交通:9-10 万吨,功能材料:5-6 万吨。可以预期,未来 10 年,从商业上, 碳纤维的应用主驱动是工业,辅驱动是航空航天;从技术发展上,碳纤维依然是航空航天及工业的双驱动模式。
从上市公司的表现来看,服务于航空航天的光威股份和中简科技固然有不错的盈利表现,但近年来,随着技术的突破和规模经济的显现,中复神鹰、吉林碳谷都已经进入盈利阶段,即使全产业投入压力巨大的恒神股份也在逐步走出困境。
趋势二:从技术攻关到生产制造,生产能力规模化
经过60年的发展,碳纤维在体育休闲和航空领域的应用解决了几个问题:产品的性能、产品的制造工艺、产品应用效果的验证、甚至是回收利用等技术难点,已经形成了具有规模化的产业,碳纤维市场容量26.15亿元,树脂基碳纤维复合材料市场容量150亿美元。但过去60年,碳纤维市场需求仅仅只有10万吨,所以,在尽管已经实现产业化,但更多体现在功能的验证阶段。
碳纤维的原材料来自石化产品,之所以被称为“黑色黄金”不是资源稀缺,而是工艺复杂,是可以通过工艺优化和规模生产来降低成本的。所以,才有从0到1解决从无到有,从1-10解决产品功能性的问题,从10-100解决成本问题。
在过去,碳纤维企业的产能规模也很少超过万吨级,这显然不是一个具有规模的行业,即使龙头企业日本东丽和美国赫氏的碳纤维收入仅仅是20亿美元左右,而且东丽经历了30年才进入稳定盈利阶段,所以,在过去60年中,这个产业并没有呈现规模经济效应。
目前,行业依然处于卖方市场,碳纤维价格相对比较稳定。对于原材料来源广泛依靠工艺优化的产业来说,规模经济效应是可以期待的经济模型。
随着市场结构的调整,工业应用的主导地位提升,预计未来进入规模生产,碳纤维的平均成本将会逐渐下降,预计未来价格波动主要来自原材料聚丙烯腈的价格波动。
目前,正值碳纤维产业投入高峰期,但显然,未来的重点将是多领域市场的开拓和成本管控能力。从任何一家企业的投资规划来看都是万吨级以上,超过20亿元的投资规模。需要注意的是,这个行业毕竟是材料行业,技术指标和工艺创新将是永恒的课题,如果企业仅仅只是做产能投入,不具备创新能力风险将是巨大的。
因此,即使行业处于规模工业应用爆发的拐点,同样是风险与机会均等,受益的是风电、光伏、压力容器、汽车等应用端。
趋势三:从供应主导到市场主导,生产基地化
长期以来,因为碳纤维的技术门槛较高,碳纤维市场几乎被六大家所垄断,行业体现为卖方市场,是一个由供应端主导的产业生态。也就是说,无论是产品,还是设备,不是你想买就能买到的。2020年下半年日本限制碳纤维对华销售,导致市场一度出现恐慌。
2020年,碳纤维产能171650吨,其中36150吨,占全部产能的21.1%;碳纤维需求106860吨,其中48851吨,占全部需求的45.71%。自给率逐年提高,但仍有62%依赖进口。
不过这一现象正随着碳纤维核心关键技术的突破发生改变。就像很多从科研阶段进入产业化阶段的产业一样,行业的发展是由供给方主导的,当技术逐渐成熟,产能的复制相对容易的时候,就转向市场主导。
是一个制造大国,未来增长快的领域如风电、光伏、氢能等行业都是需求大的市场,无论是从碳纤维需求还是从碳纤维本身从科研属性变为制造属性的角度,我们都将看到未来将成为碳纤维制造大国。2020年主要企业的产能16.315万吨,六大家族占了70.73%,不过在未来的新增产能中,则占据了绝大部分。
2019年,碳纤维经历了60年的努力,把碳纤维的需求做到10万吨以上。这是碳纤维复合材料产业链的复杂性决定的。当绝大部分核心技术被人类掌握之后,下一个10万吨的增长,时间会急剧缩短,预计2025年就会进入20万吨,2030年会进入40-50万吨。
我们可以说,是风电、光伏和氢能的发展给碳纤维带来了规模化市场机会,也可以说,正是因为有碳纤维的规模化和成本优化才给予了这些新能源产业更加完美的配套条件。
参考文献:
1、周宏《日本碳纤维技术发展史研究》(碳纤维生产技术,2018)
2、天津研究院《美国碳纤维生产技术发展近况》(碳纤维生产技术,2018)
3、沈真《深度思考?深入探讨国产碳纤维产业化之路》(碳纤维生产技术,2018)4、林刚《2020碳纤维复合材料市场报告》
5、《碳纤维简史:今天从美国碳纤维技术发展史说起!》 (碳纤维生产技术,2018)
6、周宏《美日英高性能碳纤维技术与产业发展比较》(碳纤维生产技术,2018)
7、李克健《碳纤维研究的过去与现在》(碳纤维生产技术,2018)
8、陈润、谢再红、邱恒明《民族之冠——陈光威传》(中信出版集团,2020)
9、中复神鹰、中简科技《招股说明书》