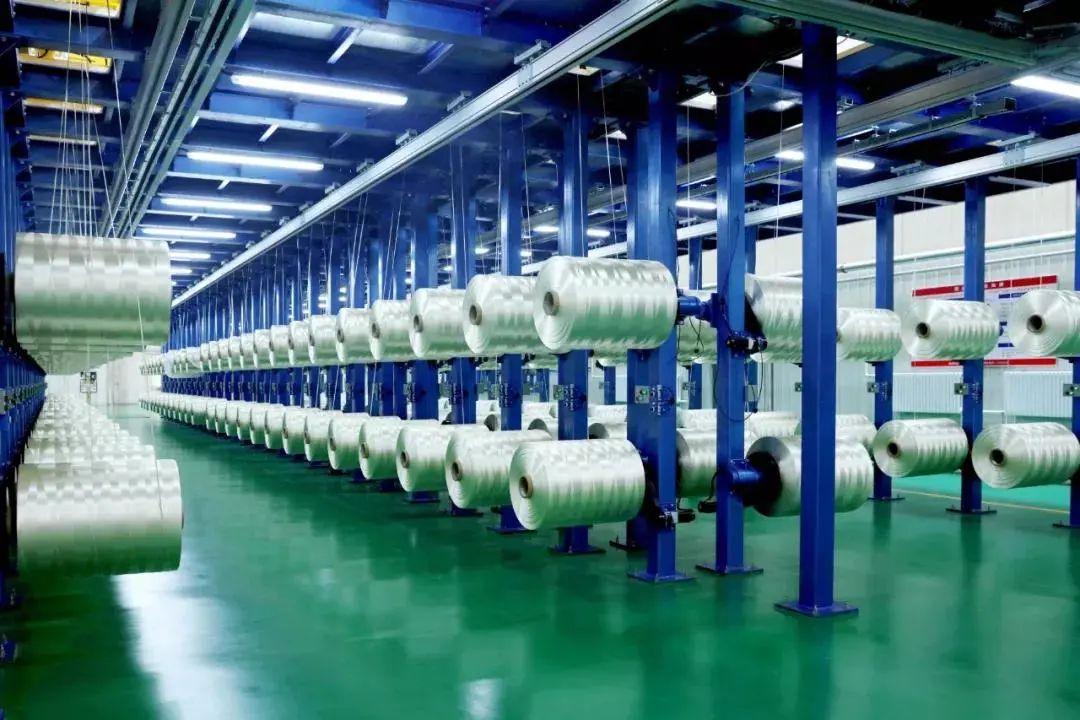
1国内供需缺口持续扩大
碳纤维实际产能仍集中于日美企业
碳纤维运行产能稳步增长,我国实际产量较低。从产能分布来看,碳纤维运行产能(处于正常生产状态且具备生产能力)稳步扩张,2020 年达到 17.2 万吨,其中美国产能占比 22%位列,大陆和日本产能占比分列第二、三名,三者合计占比 60%。虽然我国运行产能占比达到 21%,但由于较多国产碳纤维企业尚未实现关键技术突破,核心设备多为进口且适配性不强,生产线运行及产品质量不稳定,致使实际产量仅约 1.8 万吨,产能利用率不足 60%,长期存在高产能、低产量的现象。
碳纤维实际产能仍集中于日美企业。从企业产能份额占比来看,碳纤维市场依然为日、美企业所垄断,其中:(1)小丝束市场以日本企业(东丽、东邦、三菱)为主,CR3 达49%,目前碳纤维核心生产技术主要掌握在日本公司手中,产品主要应用于航空航天等高端领域,日本东丽作为高性能碳纤维龙头企业,其在小丝束市场的份额占比超过 26%。(2)大丝束市场以欧美企业(赫式、西格里)为主,CR3 高达 98%,美国产业链生态完备且生产要素具备优势,产品主要用于航天军工企业,其中赫式市场份额占比近 60%。
海外供给收紧,国内供需缺口持续扩大。2020 年以来,新冠疫情影响持续扩散,贸易整体受到较大冲击,运力紧张且不确定性强,国外碳纤维出口国内的难度逐渐加大,国内碳纤维市场供不应求。国内碳纤维主要进口来源国为日本和美国,二者合计占比近40%,2020 年底至 2021 年初,日本、美国先后加强了对碳纤维出口的政策管控,其中东丽因向未获日本《外汇及外国贸易法》许可的企业出口碳纤维而被实施行政处罚与出口禁运,美国对碳纤维等关键产品供应链进行出口审查以免于未来面临产品短缺,导致海外碳纤维供应能力进一步收紧。国内碳纤维供需缺口自 2013 年以来持续扩大,并于2020 年增至约 3 万吨,以 T700 级小丝束产品为例,产品价格由 2020 年初的 140 元/千克上涨至 2022 年初的 260 元/千克,期间涨幅近 86%。
2国产替代正当时
碳纤维产业具备崛起的主观能力与客观基础
我国碳纤维产业具备崛起的主观和客观基础。基于碳纤维及其复合材料在国防和民生中的重要作用,我国军用装备更新换代和以风电为代表的民用领域快速发展所带来的碳纤维旺盛内需,与海外供给的收缩和不确定性形成鲜明反差,也为我国碳纤维产业的国产替代之路奠定了客观基础。从制度层面来看,我国已将碳纤维列为重点支持的新兴产业,并于 2015 年起陆续出台了一系列关于碳纤维及其复合材料的产业支持政策,为碳纤维行业的蓬勃发展提供了强有力的政策支持。从公司层面来看,下游行业对国产替代产品的接受度不断提高,同时各厂商的技术工艺、产品性能及产业链整合能力持续加强,国产碳纤维产品具备“提质、增量、降本”的主观能力。
政策鼓励支持,持续引导
资金、政策扶持,我国碳纤维产业化成效初现。我国碳纤维研究与日本同时起步,但受制于自身研发基础与条件薄弱,而日美等国又对相关核心技术进行垄断与封锁,我国碳纤维研发项目几近停滞,生产技术和装备水平整体落后于国外。碳纤维是关系到国计民生的战略性新兴产业,为实现军用和民用关键装备的自主可控,自 2000 年至今,密集出台多项专项资金和产业政策来支撑碳纤维产业的发展。经过十余年的建设和研发,我国碳纤维打破了国外技术、装备封锁,产业化取得初步成效。
一方面,专项资金支持碳纤维及复合材料产业化生产及应用,已累计支持碳纤维及复合材料产业化项目百余项,支持范围覆盖了碳纤维、碳纤维复合材料及制品应用的全产业链,奠定了我国碳纤维产业从无到有、从弱到产业壮大的发展基础和物质保障。
另一方面,及地方政府相继出台了一系列关于碳纤维及其复合材料的产业支持政策,明确高性能碳纤维行业的发展重点和目标,持续引导并提升相关的生产和应用技术。此外,科技部、财政部等部委通过“973 计划”、“863 计划”、科技支撑计划等多项科技计划,支撑高性能碳纤维行业的基础研究、产业化及工程应用。
提质技术突破,自主创新
我国碳纤维申请快速提升,技术创新不断突破。我国制度于 1985 年建立,1985~2000 年我国碳纤维技术进入萌芽期,年均申请量不超过 5 件。2000 年之后,我国碳纤维技术迈入快速发展期,碳纤维申请量急速增长,2010 年之后年均申请量超过 300 件,增速显著于。由于从申请到公开有较长时间的滞后期,因此近两年申请数据有所回落。
设备方面:基于瓦森纳协定,各成员国承诺不向非成员国(包括我国在内)出口该协定清单中列出的高端技术、先进材料以及军民两用产品,通常发达只会把落后一代甚至两代的产品出口给国内厂商,即使某些先进设备能够绕过重重关卡审批进口至国内,但是工艺适配性差,也难以发挥原有价值。随着我国碳纤维研发的进度加快,部分卡脖子的设备领域不断实现技术突破,以光威、中复神鹰和中简科技为代表的碳纤维产品供应商已可自行设计、制造包括氧化炉、碳化炉在内的核心设备;以精功科技为代表的碳纤维整线设备供应商已可完成国产化千吨级碳纤维生产线的整线设计与制造,部分核心设备预氧化炉、碳化炉次出口韩国,部分关键技术指标已达国际先进水平。
技术方面:拉伸强度和拉伸模量是衡量碳纤维性能的两大核心指标。在高强度产品方面,目前国内主要碳纤维厂商基本实现了对日本东丽主要碳纤维型号的对标,产品覆盖 T300、 T700、 T800 及 T1000 等高强及高强中模型产品,部分厂商产品性能已优于东丽同型号产品。在高模量产品方面,目前国内已经形成了 M40J、M55J 级高模量碳纤维工程化技术,并突破了 M60J、M65J 级高模量碳纤维实验室技术,国内部分科研院所与企业的联合技术攻关有序推进,技术差距逐步缩小。
除强度和模量之外,原丝质量均一性指标 CV 值,也是衡量碳纤维质量稳定性的关键指标。产品 CV 值会对后续工艺的连续性和产品性能的一致性造成重要影响,CV 值越低,表示产品质量越一致、越稳定。以中简科技为例,旗下主要产品 ZT7 系列碳纤维已具备优异的CV 值,其质量稳定性已优于东丽同级别 T700S 级碳纤维,实现了材料质量稳定性与高性 能的紧密结合。
增量扩产加速,增量可期
龙头扩产加速,国产化率持续提升。根据赛奥碳纤维统计,2020 年我国主要厂商原丝产能约 10.5 万吨,碳纤维产能 3.62 万吨,实际产量 1.85 万吨,产能利用率约 51%,部分正常开车企业的产能利用率已达 90% 以上,整体来看我国已趋近国际水平的达产率。2020 年我国碳纤维自给率 38%,已初步摆脱了完全依赖进口碳纤维及原丝等产品的被动局面。未来碳纤维行业的产能增量主要由我国厂商贡献,随着后续产能的陆续释放,2025 年我国碳纤维产量有望达到 8.3 万吨,届时国产化率将进一步提升至 55%。
此前国内碳纤维生产主要以小丝束碳纤维为主,自产自销的小丝束碳纤维主要应用在军工等高附加值领域上。从当前在建产能产品结构来看,我国厂商在大丝束碳纤维上布局加速,产品多聚焦于 50K 大丝束产品,在民用以及工业级市场拥有极大发展潜力。
降本规模优势,成本下行
对碳纤维产品来说,国内厂商的降本空间来源于:(1)工艺技术优化带来的原料单耗降低;(2)规模效应优势带来的生产成本下行。
碳纤维原丝约占碳纤维生产成本的一半左右,丙烯腈价格有望保持稳定并进一步下降。原丝制备是碳纤维产业链的关键环节,其性价比与供应稳定性直接影响碳纤维产品的质量和成本。质量过关的原丝是产业化稳定生产的前提,如果原丝的分子结构和聚集态结构存在不同程度的缺陷,将严重影响碳纤维的质量和性能。而原丝成本将在很大程度上决定碳纤维产品成本,并进一步影响到碳纤维应用领域的延伸。
工艺技术优化带来原料单耗降低。丙烯腈在直接材料成本中占比超 70%,根据中复神鹰及吉林碳谷披露,1 吨碳纤维需消耗 2.0~2.2 吨聚丙烯腈原丝,1 吨聚丙烯腈原丝的丙烯腈单耗为 0.98 吨,即生产 1 吨碳纤维的丙烯腈理论单耗约 1.96 吨。经过长期的技术研发与工艺优化,各主要碳纤维公司的产品性能、一级品率逐步提升,原料单耗逐步下降,与理论耗用量逐步趋同:
➢ 在原丝方面,吉林碳谷原丝丙烯腈单耗由 18 年的 1 吨降至 20 年的 0.95 吨,2021年 6 月公司对聚合工段进行大修导致 21 年上半年的丙烯腈单耗有所上升;
➢ 在碳纤维产品方面,中复神鹰碳纤维丙烯腈单耗由 18 年的 2.02 吨降至 20 年的 1.96吨,21 年上半年神鹰西宁处于投产初期,生产线运行调试对原材料消耗较高,本部仍维持 1.96 吨的丙烯腈实际单耗。
图片
不同产品结构的企业成本构成差异较大,吉林碳谷仅包含原丝生产环节,直接材料成本占比较高,2021H1 达到 78%。;光威复材、中简科技及中复神鹰包含原丝及碳纤维生产环节,制造费用成本占比高,主要包括生产设备折旧及相关能源动力费用,体现了碳纤维产品环节的高设备开支与高能耗。总体来看,不论企业产品结构如何,直接材料的成本占比均维持下降趋势(光威复材制造费用下降速度更快)。
规模优势效应带来生产成本下行。随着各碳纤维厂商生产工艺的持续优化与技术的不断突破,各企业产能持续扩张,规模效应逐渐显现。据《碳纤维产业化发展及成本分析》统计,原丝和碳纤维的生产成本同生产规模呈反比,非直接生产因素占比在不断增加生产规模和产量的情况下会逐渐减小,大规模原丝(3000t/a)和碳纤维(1000t/a)直接生产费用分别是小规模原丝(250t/a)和碳纤维(100t/a)直接生产费用的 61%和 47%。即通过规模化生产可使碳纤维生产成本得以有效降低。
目前各主要碳纤维公司产能均突破千吨级,其中中简科技和光威复材产品主要以小丝束为主,军品业务占比较大,因而产能规模相对较小;中复神鹰以民品业务为主,前期 1 万吨 /年高性能碳纤维募投项目已陆续投产,总产能达到 1.35 万吨/年;吉林碳谷产品主要以民 用大丝束原丝为主,总产能已达 5 万吨/年。不同产品结构及规模的碳纤维企业,单吨成本有所差异,但总体下行趋势明显。