来源:Orisage、易车网
经过长时间的材料筛选与测试,一种名为"聚氨酯玻纤增强蜂窝复合材料"的新型环保材料脱颖而出,成为烈马车顶结构的理想解决方案。
复合材料科技深度解析
这种由福特与材料供应商联合研发的复合材料,通过三层结构实现性能突破:表层采用高模量玻璃纤维增强聚氨酯树脂,形成坚韧的防护外壳;核心层则植入特殊改性的芳纶纸蜂窝结构,这种源自航空航天领域的技术,在保证轻量化的同时,将材料抗弯强度提升至传统金属材料的1.8倍。
相比传统钢制车顶重量大幅轻量化,使整车重心降低不少,显著提升操控稳定性。在极端测试中,该材料经受住大幅度温差循环考验,即便在沙漠暴晒或极地穿越场景下均保持结构稳定。
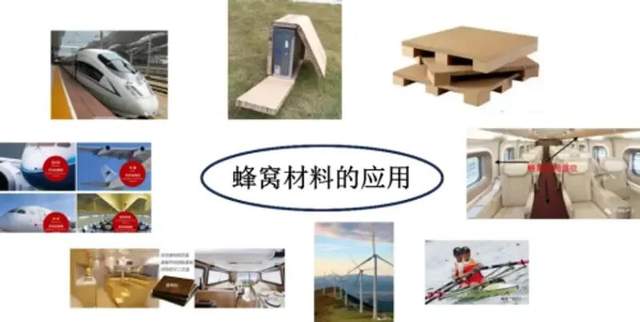
对标芳纶纸的技术跃迁
当前高端制造领域炙手可热的芳纶纸材料,以其优异的耐高温、抗撕裂性能著称,广泛应用于防弹衣、高铁车厢等尖端领域。而福特采用的聚氨酯玻纤增强纸蜂窝复合材料,在继承芳纶纸高强度特性的基础上实现了多维升级:
- 加工性能突破:采用热压成型工艺,可实现复杂曲面的一次成型,生产效率提升40%;
- 功能集成创新:蜂窝结构天然具备隔音降噪特性,使车内噪音值降低5分贝,同时预留管线通道空间,为后期加装车顶行李架、探照灯等配件提供可能;
- 跨领域应用前景展望:这种革命性材料的应用远不止于汽车领域。在建筑行业,其轻质高强特性可打造装配式建筑模板,使施工周期缩短30%;在航空航天领域,某型无人机已采用该材料替代传统复合材料,实现有效载荷提升20%。
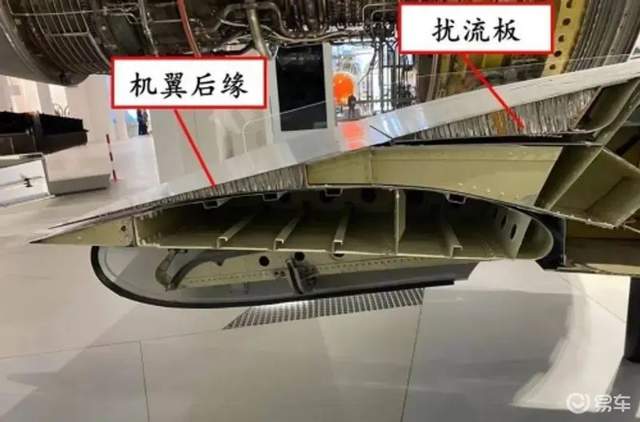
随着消费者对车辆功能延展性的需求持续攀升,福特烈马的创新实践为行业指明了方向:当模块化设计遇见先进复合材料,不仅重新定义了人与机械的交互方式,更在轻量化、环保性、功能集成三大维度树立了全新标杆。这场发生在车顶上的材料革命,或许正是通向未来移动出行生态的关键钥匙。
聚氨酯玻纤增强纸蜂窝复合材料:
在汽车中的应用并非首次
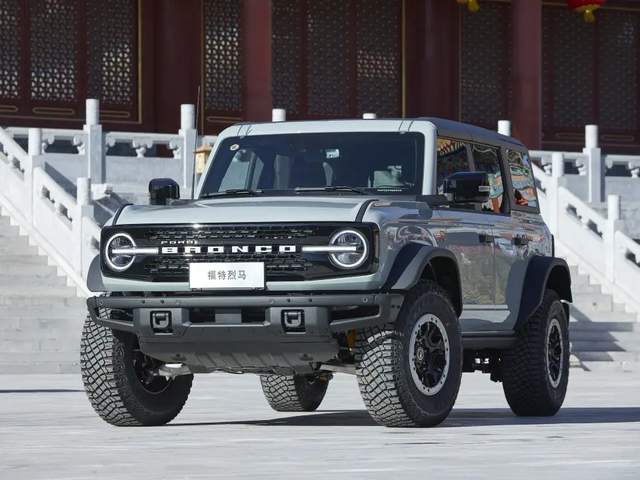
福特烈马在车顶中用到的聚氨酯玻纤增强纸蜂窝复合材料,采用的是喷涂模压成型技术。据悉,该成型技术并非近些年才出现,其诞生时间较早,最初由科思创推出,因此早期这种聚氨酯复合材料成型工艺常被称作Baypreg®法。
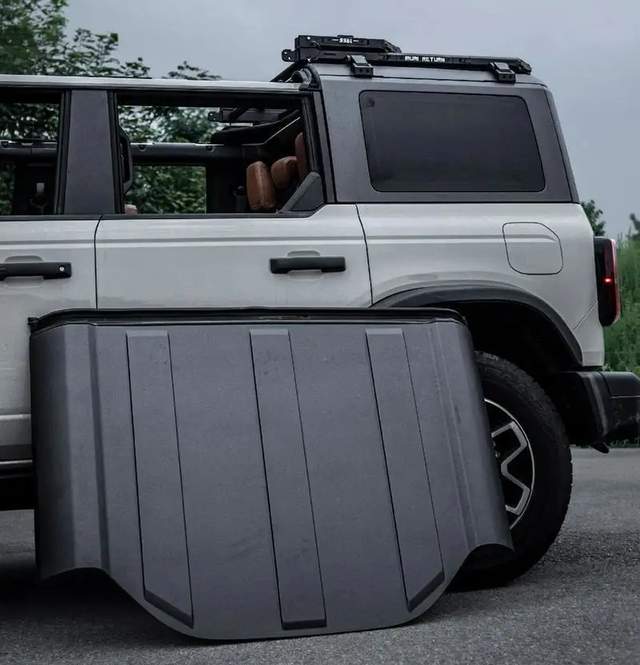
该成型工艺的原理是:将纸蜂窝等芯材埋在两层玻纤毡之间,用双组份聚氨酯喷涂浸渍,然后在闭合模具中压塑并加热固化。由于这种板材比其他夹芯产品更轻,因而对汽车等用途很有吸引力。典型用途有车身底板、行李仓底板、备胎罩、天窗板等。聚氨酯材料可用多种纤维材料如玻璃纤维、碳纤维或天然纤维增强。
早在2015年,巴斯夫的聚氨酯玻纤增强纸蜂窝材料在量产车型smart fortwo中得到了应用,这也意味着全球首个采用A类蜂窝夹芯结构的外车身部件成功实现了量产。smart fortwo的车顶模块由一个纸蜂窝和两层玻璃纤维毡组成,它们在浸渍过程中被喷涂了巴斯夫Elastoflex® E聚氨酯泡沫组合料。该车顶模块的重量与之前车型普通车顶相比减轻了30%,但具备同等的强度和抗弯刚度。
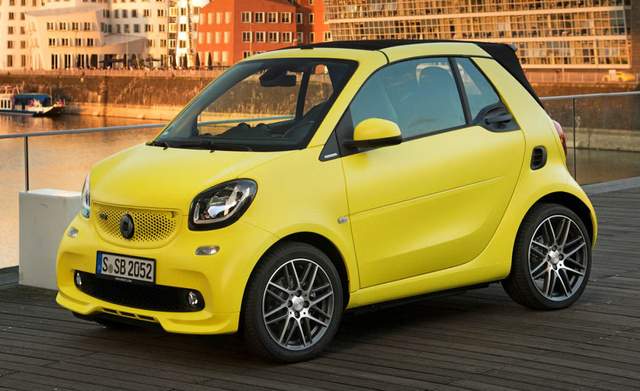
2024年,长安推出全新启源E07车型(电动SUV),其后备箱便采用了巴斯夫的聚氨酯玻纤增强纸蜂窝材料。采用Elastoflex® E半硬质聚氨酯系统对两种玻璃纤维毡包裹的蜂窝纸板进行发泡和压制,在保持强度和刚度不变的情况下,可减少构件重量20-30%。
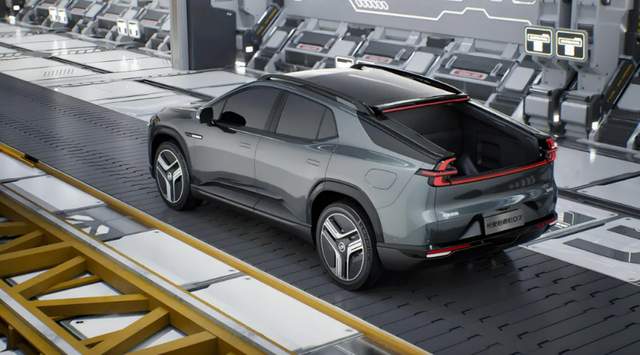
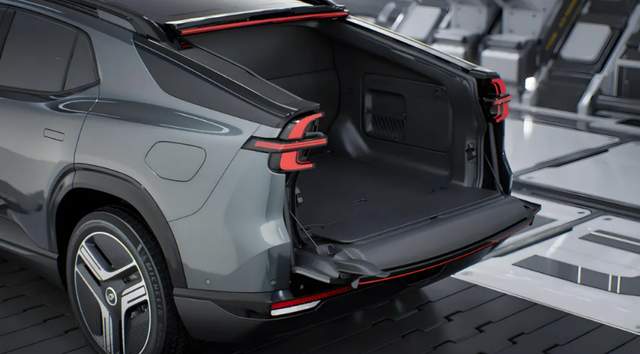
伴随工艺发展,
聚氨酯复合材料进入更多终端应用
凭借轻质高强的特性,复合材料可以在诸多应用中替代金属部件。聚氨酯树脂作为一种制造复合材料的新型材料,逐渐得到了市场的认可。在其快速发展的背后,离不开工艺技术的革新。
从最初的反应注射成型(RIM)工艺到增强反应注射成型(R-RIM)和结构反应注射成型(S-RIM),再到长纤维注射(LFI)、拉挤、真空灌注、纤维缠绕、树脂传递成型(RTM)和喷涂转移模压(STM)等,聚氨酯复合材料在各个下游领域得到了长足的发展。
早期,聚氨酯复合材料常被应用于汽车保险杠、挡泥板、汽车门板、货箱板、车顶组件、公共汽车行李架等一系列汽车部件。而如今,聚氨酯复合材料在门窗型材、铁路枕木、电线杆、5G通信塔、风电叶片、电池包壳体、光伏边框等新型应用领域得到了商业化应用。
以下是聚氨酯复合材料一些有前景的新型应用领域——
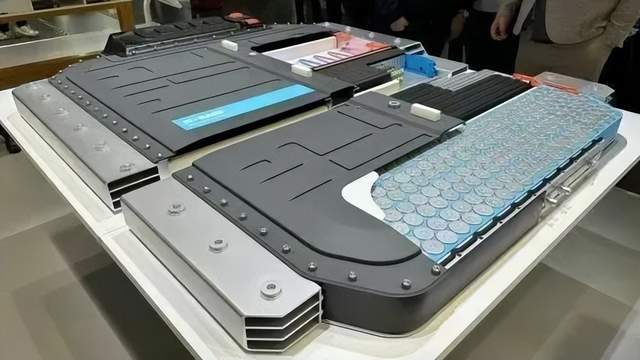
电池包壳体——采用工艺:HP-RTM、STM
近年来,多起电动汽车遭遇热失控引发的自燃事故,引起主机厂对电池包安全性的高度重视。装载电池模组以及阻隔车身底板的壳体阻燃性变得尤为重要。
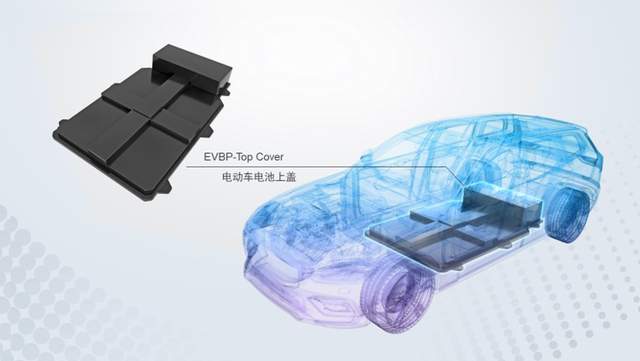
2022年,科思创开发的适用于高压树脂传递模塑成型(HP-RTM)工艺的聚氨酯电池包上壳体解决方案,完成了电池包重重严苛的材料级别和最终电池包成品级别的各项测试,并实现了批量投产。目前行业除了要求电池壳的材料满足UL94 V-0阻燃级别, 也要求上壳体通过严格的外部火烧试验。科思创开发的玻纤增强聚氨酯复合材料树脂,遇火后会在材料表面形成惰性气体保护层和碳化层。同时,高比例的玻璃纤维作为无机非金属材料,阻止火焰继续燃烧,保证了电池上壳体的安全性,且不需要防火涂层的额外费用和工序。聚氨酯复合材料通过了国际欧盟REACH,ROSH和GB38031-2020对机械性能、高温高湿老化、氙灯老化、耐酸耐碱、耐高温和绝缘性能等的测试。
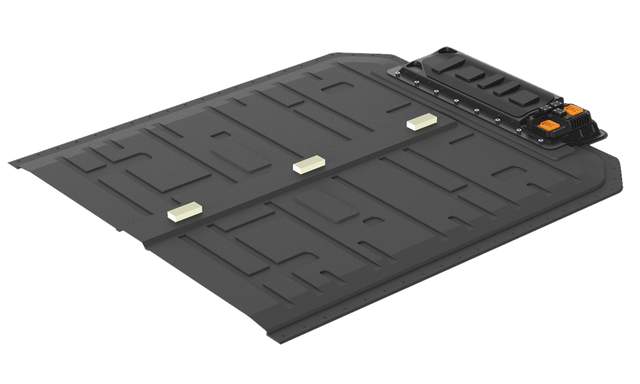
2022年,巴斯夫开发出基于喷涂转移模压(STM)工艺的聚氨酯复合材料电池包壳体解决方案,搭载该创新解决方案的几款电动汽车已经实现了大批量上市。经过充分的量产验证,聚氨酯复合材料电池包壳体兼具阻燃好,重量轻的特性,可以提升电动车的驾驶安全性。此外,在生产方面,其工艺无需预成型,生产效率远远高于其他传统的聚氨酯复合材料成型工艺。它可直接应用于现有成熟的汽车供应链和生产设施,生产的效率高,非常适于汽车行业的快速大规模生产,是电动汽车电池包减重降本的理想解决方案。巴斯夫的聚氨酯复合材料电池包壳体通过的阻燃相关测试包括:UL94V-0阻燃级别,GB 38031-2020外部火烧试验。
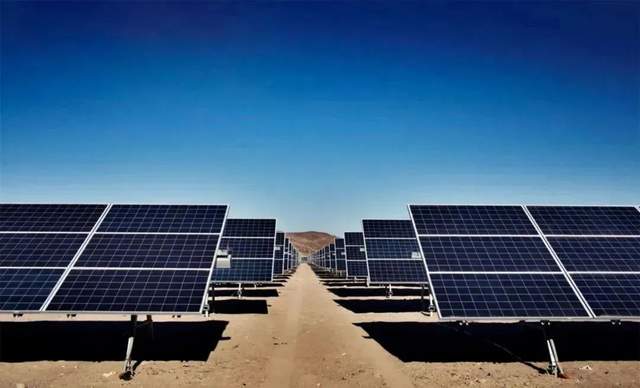
光伏边框——采用工艺:拉挤成型
长期以来,绝大部分光伏组件的边框材料均采用铝合金型材。随着光伏产业的飞速发展,光伏行业用铝量亦随之逐年攀升。铝合金型材的上游材料是电解铝,而电解铝的生产过程需要消耗大量电力,造成大量碳排放。聚氨酯复合材料边框作为一种可持续的解决方案,近年来广受关注。
聚氨酯复合材料光伏边框的优势
① 轻质。只有钢铁的27%重量,铝合金的75%重量。
② 高强。抗弯曲强度是铝合金的6倍多。
③ 绝缘。聚氨酯复合边框是热与电的不良导体,导热系数只是铝合金的1/640。电站可有效的抗雷击。
④ 抗PID。聚氨酯复合材料的体积电阻率可达1×1014 Ω·cm,光伏组件采用非金属边框封装后,大大降低了形成漏电回路的可能性,有助于减少PID电势诱导衰减现象的产生。
⑤ 耐老化、耐腐蚀。
⑥ 防火。聚氨酯复合材料的防火性能可以到达B1级阻燃要求。
⑦ 耐高低温。耐低温-150℃以上。
⑧ 可设计性好。尺寸收缩率是铝合金的1/3,线膨胀系数是1/3~1/4。
⑨ 力学性能优异。其轴向拉伸强度达到了传统铝合金材料的7倍以上。同时,其还具有很强的耐盐雾和耐化学腐蚀性能。
⑩ 色彩、光泽以及表面效果可灵活选择,满足多样化需求;有极好的附着性能,而且VOC排放极低。
国内外厂商纷纷布局
除了光伏、复合材料相关企业外,玻璃纤维和聚氨酯等企业也有开始布局。
浙江德毅隆科技股份有限公司是由国内外复合材料研发、光伏领域等资深专家联合创办的原创技术研发企业,拥有30年以上的复合材料型材拉挤生产经验,复合材料光伏边框研发已有10年历史。公司采用世界最先进的集中控制网络注射拉挤工艺,生产玻璃纤维增强聚氨酯GRPU型材,现已拥有GRPU型材拉挤线108条、型材自动化加工线、环保自动涂装线,已具备年产8GW太阳能边框产能,2024年底将达成年产15GW太阳能边框的综合产能。
福膜科技深耕光伏行业13年,是光伏组件封装背板用PVDF膜龙头企业。2015年3月,福膜科技在三花控股集团梅渚工业园基地建设了一个分布式示范电站,装机容量为1.5MW,是国内首个也是唯一一个兆瓦级别的复合材料边框应用的实证光伏电站,至今依然正常运行中。2020年,在铝锭涨价和聚氨酯原料供应价格显著下降的双重情况下,福膜科技于2020年5月重启复合材料边框的市场推进工作,配合多家国内一线组件公司进行项目联合开发。2023年4月TÜV南德为福膜科技光伏复合材料边框颁发认证证书。
江苏沃莱新材料有限公司是一家致力于光伏复合材料边框领域的创新型企业。2023年2月6日,TÜV南德为沃莱新材的光伏组件复合材料边框产品颁发TÜV南德全球首张基于TÜV南德技术规范PPP 58208A的产品认证证书。2023年12月,巴斯夫与沃莱新材签署合作谅解备忘录(MoU),共同在原材料供应、产品开发、市场拓展、全球推广等多个层面进行广泛和深入的合作,携手推动聚氨酯复合材料边框在光伏行业的应用,探索光伏行业在“海、漠、房”等不同场景下的未来发展。2025年5月,由晶澳科技供货的海上光伏组件“耀蓝”完成首批交付,助力华电昌黎海上光伏试点项目率先开工建设。该项目是河北省海上光伏总体规划的先锋项目,同时也是华电集团首个100%海上光伏项目。在光伏组件“耀蓝”中,100%采用江苏沃莱新材料的玻纤增强聚氨酯复合材料边框制品。
卡法时(江苏)新材料有限公司是一家聚氨酯玻璃纤维复合材料制品和聚氨酯结构件复合材料产品制造的加工型企业。公司经过数年的摸索创新,拥有丰富的聚氨酯拉挤型材的生产加工经验,产品包括聚氨酯复合材料绝缘边框,聚氨酯复合材料绝缘支架等。2024年1月5日,TÜV莱茵为卡法时(江苏)新材料有限公司颁发了光伏组件用复合材料边框产品认证证书。
威远盛祥复合材料有限公司从事复合材料生产30余年,从2017年开始涉足光伏领域,提供全套复合材料光伏支架及解决方案。2023年投产聚氨酯光伏边框生产。2024年1月19日,威远盛祥复合材料有限公司获得国际权威认证机构德国莱茵TÜV 光伏组件用聚氨酯边框认证证书。
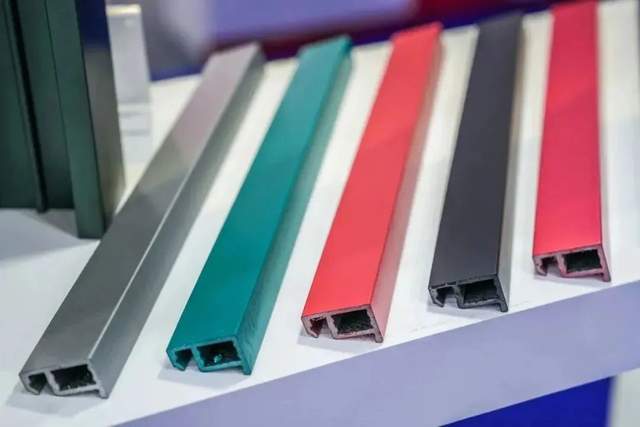
在复合材料边框用聚氨酯方面,2023年3月23日,TÜV莱茵为科思创的拜多®聚氨酯树脂颁发材料认证证书,这是TÜV莱茵颁发的首张应用于太阳能边框的聚氨酯材料认证证书。2023年5月24日,TÜV南德为万华化学光伏组件复合材料边框用聚氨酯产品颁发基于TÜV SÜD技术规范PPP 58208A的TÜV南德公告材料认证证书。万华化学成为在全球范围内首批收获光伏组件复合材料边框用聚氨酯材料TÜV南德认证证书的企业。
