
在追求可持续性的过程中,传感器正在减少周期时间、能源使用和浪费,实现闭环过程控制的自动化,并增加知识,为智能制造和结构开辟新的可能性。
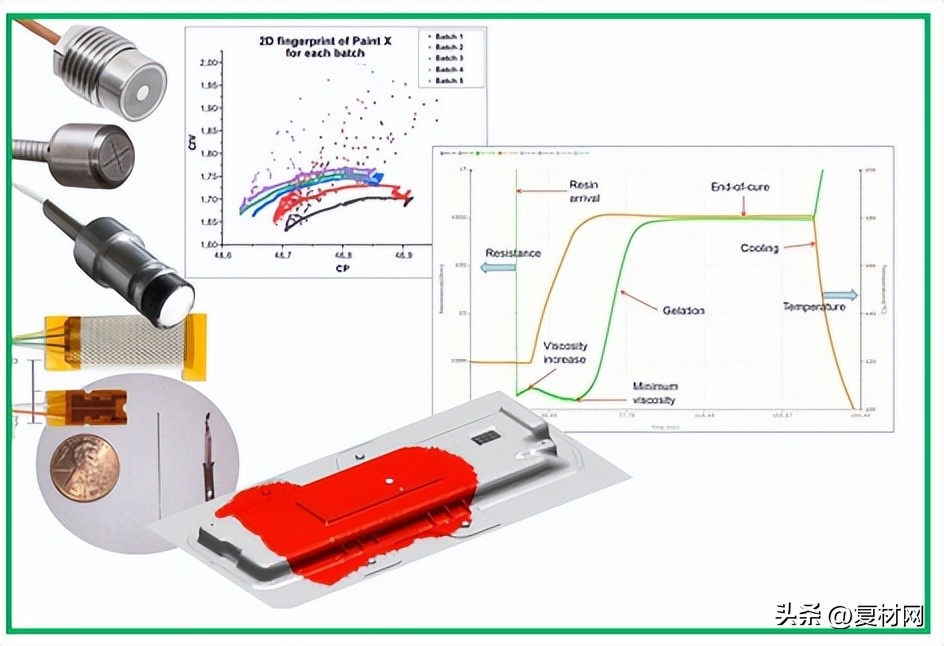
流程可见性
左侧传感器(从上到下):热通量(TFX)、模内电介质(Lambient)、超声波(奥格斯堡大学)、一次性电介质(Synthesites)以及位于penny和热电偶之间的微丝(AvPro)。图表(顶部,顺时针):使用电磁传感器的胶体渗透性(CP)与胶体离子粘度(CIV)的关系、树脂电阻与时间的关系(Synthesites)以及己内酰胺注入预成型体的数字模型(CosiMo项目,DLR ZLP,奥格斯堡大学)。
随着全球工业继续从新冠肺炎疫情中复苏,它已转向优先考虑可持续性,这要求减少废物和资源消耗(如能源、水和材料)。因此,制造业必须变得更加高效和智能化。但这需要信息。对于复合材料而言,这些数据从何而来?
正如CW 2020年关于“复合材料4.0”系列文章所述,确定提高部件质量和生产所需的测量方法,以及实现这些测量所需的传感器,是迈向智能制造的第一步。在2020年和2021年期间,CW报道了传感器——介电传感器、热通量传感器、光纤传感器以及使用超声波和电磁波的非接触式传感器—以及展示其能力的项目。本文基于这些报道,讨论了复合材料中使用的传感器、其预期的益处和挑战,以及正在开发的技术领域。值得注意的是,正在成为复合材料行业领导者的公司已经开始探索和驾驭这一领域。
为什么要使用传感器?
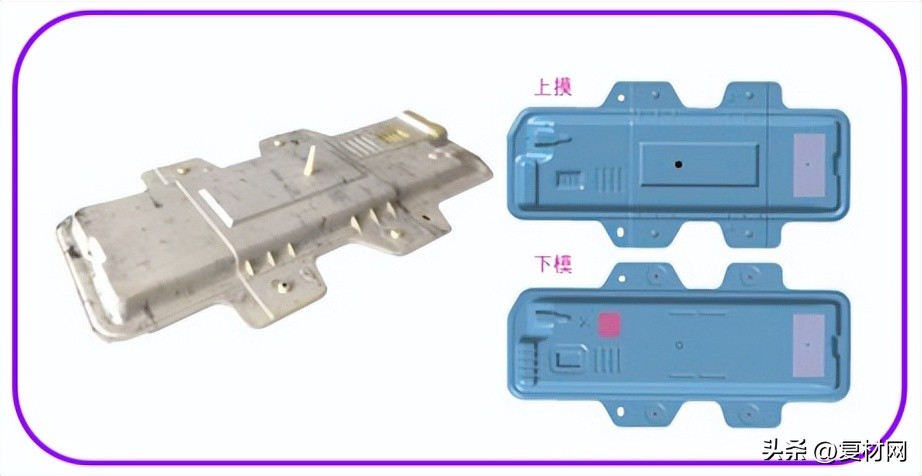
CosiMo中的传感器网络
CosiMo项目的热塑性复合材料电池箱盖演示器的T-RTM成型中使用了74个传感器组成的网络,其中57个是奥格斯堡大学开发的超声波传感器(如右图所示,上半模和下半模中的淡蓝色点)。
目标1. 省钱。CW 2021年12月的博客“为复合材料工艺优化和控制定制超声波传感器”描述了奥格斯堡大学(德国奥格斯堡联合国大学)开发74个传感器网络的工作,该网络用于为CosiMo(智能移动复合材料)项目制造电动汽车电池箱盖演示器。该零件是使用热塑性树脂传递模塑(T-RTM)制成的,该模塑将己内酰胺单体原位聚合成聚酰胺6(PA6)复合材料。联合国大学教授、联合国大学奥格斯堡人工智能(AI)生产网络主任马库斯·绍斯(Markus Sause)解释了为什么传感器很重要:“我们提供的最大优势是在加工过程中可视化黑匣子内发生的事情。目前,大多数制造商只有有限的系统来实现这一点。例如,他们在使用树脂注入制造大型航空航天零件时使用非常简单或特定的传感器。如果注入过程出错,你基本上会有一大块废料。但是如果你有一个解决方案来了解生产过程中出现的问题及其原因,你就可以解决并纠正它,从而节省大量资金。”
热电偶是“简单或特定传感器”的一个例子,几十年来一直用于在热压罐或烤箱固化过程中监测复合材料层压板的温度。它们甚至被用来控制烤箱或加热毯中的温度,以使用热粘合剂固化复合材料修复贴片。树脂制造商在实验室中使用了各种传感器来监测树脂粘度随时间和温度的变化,以开发固化配方。然而,正在出现的是一个传感器网络,它可以根据多个参数(如温度和压力)和材料的状态(如粘度、聚合、结晶)在现场可视化和控制制造过程。
例如,为CosiMo项目开发的超声波传感器使用与超声波检测相同的原理,超声波检测已成为成品复合材料零件无损检测(NDI)的支柱。美捷特(英国拉夫堡)首席工程师佩特罗斯·卡拉帕帕斯表示:“随着我们走向数字化制造,我们的目标是最大限度地减少未来零部件生产后检查所需的时间和劳动力。”。他与国家复合材料中心(NCC,Bristol,英国)合作,演示了由Cranfield大学(Cranfield,英国)开发的线性介电传感器的使用,以监测Solvay(索尔维)的EP 2400环氧树脂基材在商业航空发动机换热器的1.3米长、0.8米宽和0.4米深的复合材料外壳RTM过程中的流动和固化。卡拉帕帕斯说:“当我们研究如何制造更大的组件和更高的生产率时,我们无法承受对每个零件进行所有传统的后处理检查和测试。”。“现在,我们在RTM零件旁边制作测试面板,然后进行机械测试以验证固化周期。但有了这个传感器,就不需要了。”
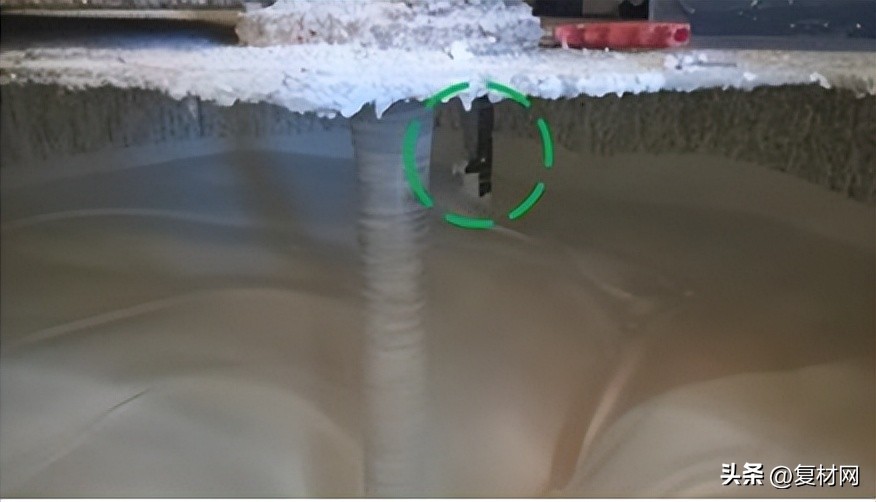

Collo Probe浸没在涂料混合容器中(顶部绿色圆圈),可检测混合何时完成,从而节省时间和
能源
Colloid Tek Oy(芬兰坦佩雷科洛)首席执行官兼创始人马蒂·拉尔韦莱表示:“我们的目标不是成为另一种实验室设备,而是专注于生产系统。”。CW 2022年1月的博客“复合材料的指纹液体”探讨了Collo将电磁场传感器、信号处理和数据分析相结合,以测量任何液体的“指纹”,如单体、树脂或粘合剂。拉尔韦莱说:“我们提供的是一种实时提供直接反馈的新技术,这样你就可以更好地了解这个过程的实际工作原理,并在出现问题时做出反应。”。“我们的传感器将实时数据转换为可理解和可操作的物理量,如流变粘度,从而优化工艺。例如,您可以缩短混合时间,因为您可以清楚地看到混合何时完成。因此,与优化程度较低的加工相比,您可以提高生产率,节约能源,减少废品。”
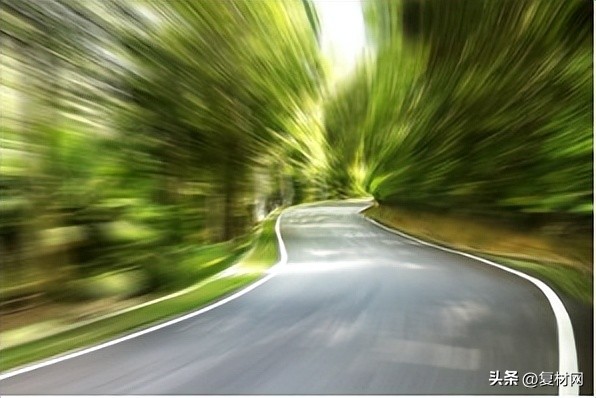
目标2. 增加流程知识和可视化。拉尔韦莱说,就聚合等过程而言,“你不能只从快照中看到太多。你只是取了一个样本,走进实验室,看看几分钟或几小时前的状态。这就像在高速公路上开车,每小时睁开眼睛一分钟,试图预测道路从哪里开始。” 索斯(Sause)表示赞同,并指出CosiMo开发的传感器网络“帮助我们全面了解过程和材料行为。我们可以看到过程中局部效应对零件厚度或集成材料(如泡沫芯)变化的反应。我们试图做的是提供有关实际发生的信息。这使我们能够确定各种因素,如流动前沿的形状、到达预成型件每个部分的时间以及每个传感器位置的聚合度。”
Collo与环氧树脂粘合剂、油漆甚至啤酒的制造商合作,为每批生产的产品创建了工艺配置文件。每个制造商现在都可以看到其工艺的动态,并设置更优的参数,当批次不符合规格时,可以发出警报进行干预。这有助于稳定和提高质量。
Meggitt的卡拉帕帕斯说:“我想知道零件制造过程中发生了什么,而不是打开盒子看看之后发生了什么。”。“我们使用克兰菲尔德的介电传感器开发的东西让我们看到了现场的过程,我们也能够验证树脂的固化。”使用下面描述的所有六种传感器(不是详尽的列表,但只是一小部分选择,供应商也是如此)可以监测固化/聚合和树脂流动。一些传感器具有额外的功能,结合传感器类型可以扩展在复合材料成型过程中跟踪和可视化的可能性。CosiMo使用Kistler(瑞士温特图尔)提供的超声波、电介质和压阻式模内传感进行温度和压力测量,证明了这一点。
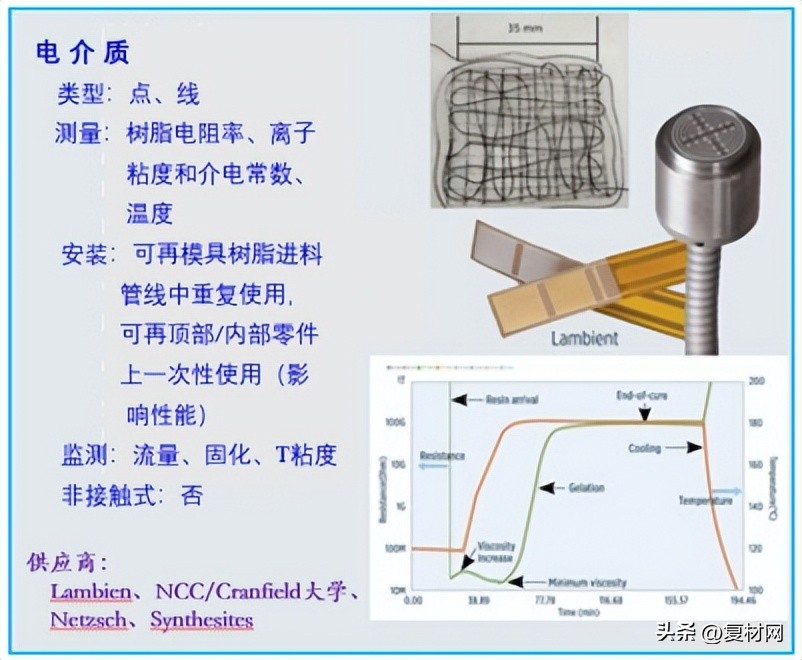


基于模内传感器网络的测量数据,CosiMo零件(注射入口中心为白点)的流动前沿随时间变化的视频。
目标3:缩短循环时间。Collo传感器可以测量由两部分组成的快固化环氧树脂的均匀性,因为在RTM过程中以及放置此类传感器的模具中的每个位置,零件A和B被混合和注射。这可能有助于使更快的固化树脂适用于城市空中交通等应用,与目前的单组分环氧树脂如RTM6相比,UAM将提供更快的固化周期。
Collo传感器还可以监测和可视化正在脱气、注入和固化的环氧树脂,以及每个过程何时完成。根据被加工材料的实际状态(与传统的时间和温度配方相比)结束固化和其他过程称为材料状态管理。几十年来,像AvPro(美国俄克拉荷马州诺曼)这样的公司一直在追求MSM,它跟踪零件材料和工艺的变化,因为它追求玻璃化转变温度(Tg)、粘度、聚合和/或结晶的具体目标。例如,CosiMo中的传感器网络和数字分析用于确定加热RTM压机和模具所需的最短时间,发现在4.5分钟内实现了96%的最大聚合。
Lambient Technologies(美国马萨诸塞州剑桥)、Netzsch(德国塞尔布)和Synthesites(比利时Uccle)等介电传感器供应商也展示了缩短循环时间的能力。Synthesites与复合材料制造商Hutchinson(法国巴黎)和庞巴迪贝尔法斯特(现为Spirit AeroSystems(爱尔兰贝尔法斯特)的研发项目报告称,基于树脂电阻和温度的实时测量,它能够将RTM的固化周期缩短30-50%,这些测量值由其Optimold数据采集单元和Optiview软件转换为估计的粘度和Tg。Synthesites总监尼科斯·潘特利解释说:“制造商可以实时看到Tg,这样他们就可以决定何时停止固化周期。”。“他们不必等待完成比必要的传统周期更长的时间。例如,RTM的传统周期是在180°C下完全固化2小时。我们已经看到,在某些几何形状中,这可以缩短到70分钟。”INNOTOOL 4.0项目也证明了这一(见“使用热通量传感器加速RTM”),其中热通量传感器用于将RTM固化周期从120分钟缩短到90分钟。
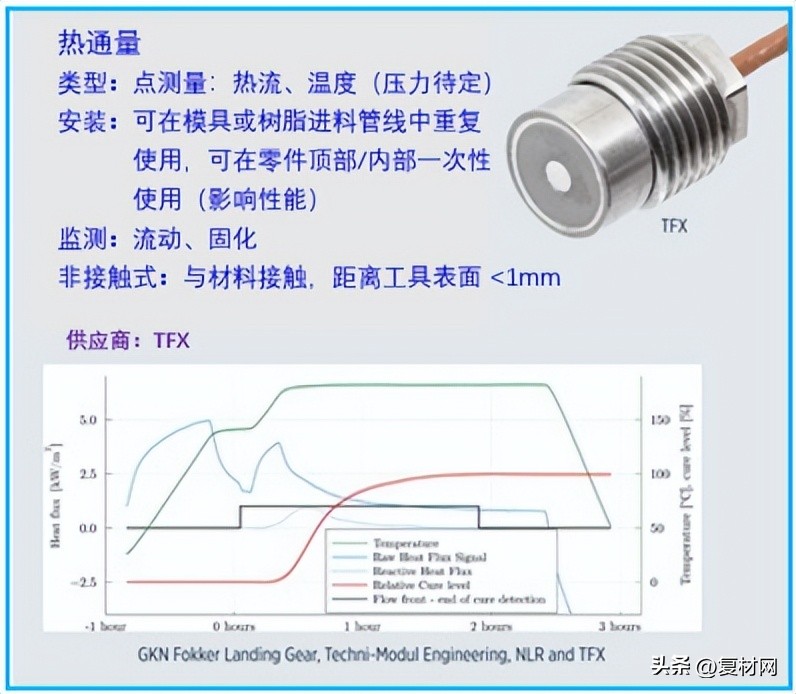


目标4:自适应过程的闭环控制。对于CosiMo项目,最终的目标是在复合材料零件生产过程中实现自动闭环控制。这也是CW在2020年报告的ZAero和iComposite 4.0项目的目标(成本降低30-50%)。请注意,这些涉及不同的工艺—与CosiMo中的高压T-RTM相比,预浸料带的自动放置和用速固化环氧树脂(iComposite 4.0)进行RTM的纤维喷涂预成型。所有这些项目都使用带有数字模型和算法的传感器来模拟过程并预测成品的结果。
索斯解释说,过程控制可以设想为一系列步骤。他说,第一步是将传感器和工艺设备集成在一起,“以可视化加工黑匣子内发生的事情以及要使用的参数。另外几个步骤,也许是闭环控制的一半,是能够按下停止按钮进行干预、调整工艺并防止拒收零件。最后一步,你可以开发数字孪生,这可以实现自动化,但也需要投资机器学习方法。”在CosiMo中,这项投资使传感器能够将数据馈送到数字孪生,然后使用边缘分析(在工艺线边缘进行的计算与从中央数据存储库进行的计算)来预测流动前沿动态、每个纺织预成型件的纤维体积含量和潜在的干燥点。索斯说:“理想情况下,您可以建立设置,以便在过程中实现闭环控制和调整。”。“这些将包括注射压力、模具压力和温度等参数。您还可以使用这些信息来优化您的材料。”
在实现这一目标的过程中,公司正在使用传感器来自动化流程。例如,Synthesites正在与客户合作,将传感器与设备集成在一起,以便在注入完成时关闭树脂入口,或在达到目标固化时打开加热压机。
选择和集成传感器
卡拉帕帕斯指出,为了确定哪种传感器最适合每种用例,“你需要了解你想要监测的材料和工艺的变化,然后你必须有一个分析仪。”分析仪将询问器或数据采集单元收集的原始数据转换为制造商可用的信息。索斯说:“你实际上看到许多公司都集成了传感器,但他们对数据什么都不做。”。他解释说,需要的是“系统的数据采集,以及数据存储架构,以便能够对数据进行处理。”
“终端用户不只是想查看原始数据,” 卡拉帕帕斯说。“他们想知道,‘过程优化了吗?’以及‘什么时候可以进行下一步?’为此,你需要结合多个传感器进行分析,然后使用机器学习来加速过程。”Collo和CosiMo团队使用的这种边缘分析和机器学习方法,通过粘度图、树脂流动前沿的数字模型以及最终控制过程参数和机械的能力来实现可视化。
Optimold是Synthesites为其介电传感器开发的分析仪。Optimold装置由Synthesites的Optiview软件控制,使用温度和树脂电阻测量值进行计算,并显示实时图表,监测树脂状态,包括混合比、化学老化、粘度、Tg和固化度。它可以与预浸料和液体成型工艺一起使用。一个单独的单元Optiflow用于流量监测。
Synthesites还开发了一个固化模拟器,该模拟器不需要模具或零件中的固化传感器,而是在该分析仪单元中使用温度传感器和树脂/预浸料样品。Synthesites总监尼科斯·潘特利表示:“我们正在将这种最新的方法应用于风力涡轮机叶片生产的注入和粘合剂固化。”。
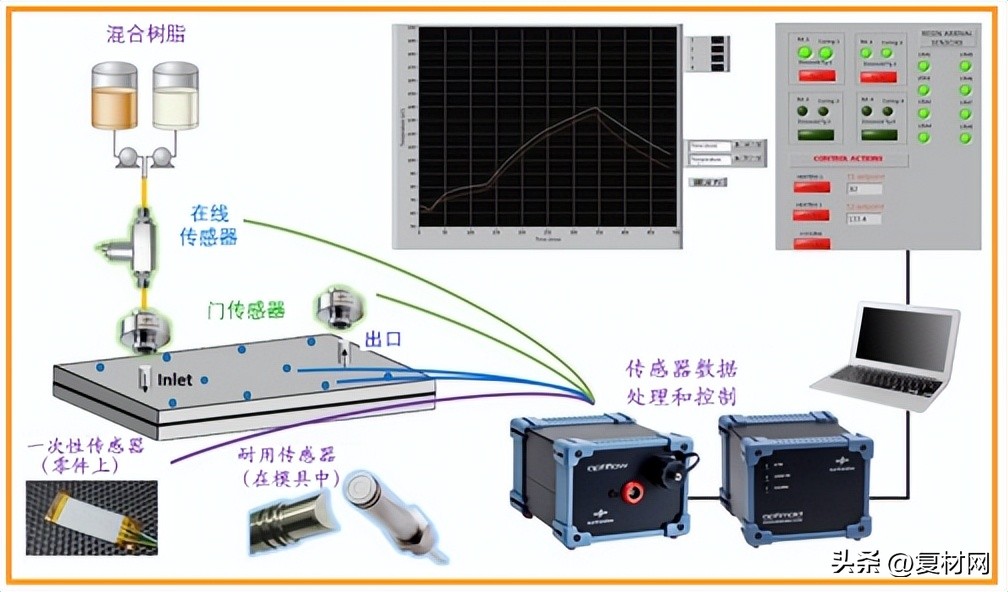
Synthesites过程控制系统集成了传感器、Optiflow和/或Optimold数据采集单元以及
OptiView和/或在线树脂状态(ORS- online Resin State)软件。
因此,大多数传感器供应商都开发了自己的分析仪,有些使用机器学习,而另一些则没有。但复合材料制造商也可以开发自己的定制系统,或购买现成的仪器并对其进行修改以满足特定需求。然而,分析仪的性能只是需要考虑的一个因素。还有许多其他的。
在选择使用哪些传感器时,接触也是一个重要的考虑因素。传感器可能需要与材料、询问器或两者接触。例如,热通量和超声波传感器可以插入距离表面1-20毫米的RTM模具中—与模具中的材料接触对于精确监测来说是不必要的。超声波传感器还可以根据使用的频率在不同深度对零件进行询问。Collo电磁传感器也可以通过与树脂接触的非金属容器或工具读取液体或零件的深度(2-10厘米,具体取决于询问频率)。
然而,磁性微丝目前是唯一能够询问距离复合材料10厘米以内的传感器。这是因为它使用电磁感应来引发嵌入复合材料中的传感器的响应。AvPro的ThermoPulse微丝传感器嵌入粘合剂粘合线中,通过25毫米厚的碳纤维层压板进行询问,以测量粘合过程中的温度。由于微丝的毛发状直径为3-70微米,它不会影响复合材料或粘合线的性能。在100-200微米的稍大直径下,光纤传感器也可以嵌入而不会降低结构性能。然而,由于它们使用光进行测量,光纤传感器必须与询问器有线连接。同样,由于介电传感器使用电压来测量树脂的特性,因此它们也必须连接到询问器,并且大多数传感器还必须接触它们正在监测的树脂。
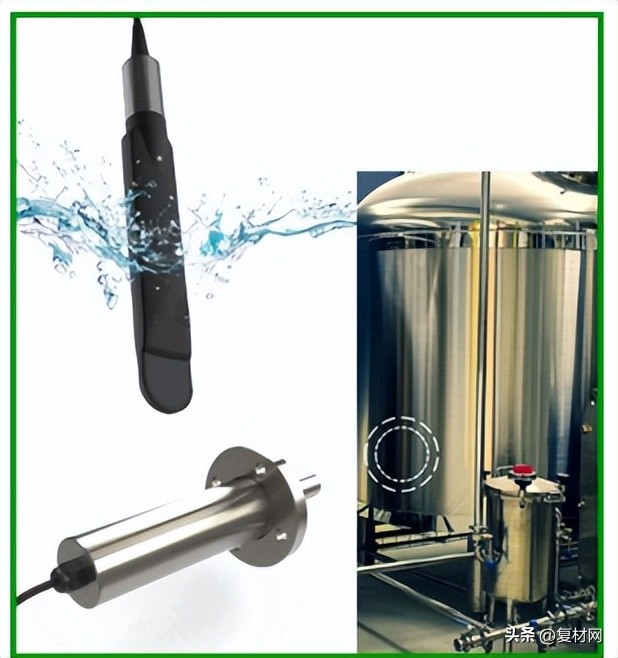
Collo Probe(顶部)传感器可以浸入液体中,而Collo板(底部)安装在安全壳/混合容器或工艺管道/进料管线的壁中
传感器的温度能力是另一个关键考虑因素。例如,大多数现成的超声波传感器通常在高达150°C的温度下工作,但CosiMo中的零件需要在200°C以上的温度下成型。因此,联合国协会不得不设计一种具有这种能力的超声波传感器。Lambient的一次性介电传感器可用于高达350°C的零件表面,其可重复使用的模内传感器可用于250°C。RVmagnetics(斯洛伐克科希策)开发了用于复合材料的微丝传感器,可承受500°C的固化。卡拉帕帕斯说,尽管Collo传感器技术本身没有理论温度限制,但Collo Plate的钢化玻璃屏蔽和Collo Probe的新型聚醚醚酮外壳都在150°C下进行连续使用测试。与此同时,PhotonFirst使用聚酰亚胺涂层为其用于SuCoHS项目的光纤传感器提供350°C的工作温度,以实现可持续和经济高效的高温复合材料。
另一个需要考虑的因素,特别是安装时,是传感器是在单个点进行测量,还是具有多个感测点的线性传感器。例如,Com&Sens(比利时埃克斯)光纤传感器的长度可达100米,具有多达40个光纤布拉格光栅传感点,最小间距为1厘米。这些传感器已用于66米长的复合材料桥梁的结构健康监测,以及在大型桥面板注入过程中监测树脂流动。为这些项目安装单独的点传感器将需要无数的传感器和大量的安装时间。NCC和克兰菲尔德大学声称他们的线性介电传感器也有类似的好处。NCC的技术拉动项目经理杰克·阿尔科克表示,与Lambient、Netzsch和Synthesites提供的单点介电传感器相比,“对于我们的线性传感器,我们可以沿长度连续监测树脂流量,这大大减少了您在零件或工具中所需的传感器数量。”

NLR将一个特殊单元集成到科里奥利AFP头的第八通道中,将四个光纤传感器阵列放置在高温碳纤维增强复合材料测试面板中。
线性传感器也有助于自动化安装。在SuCoHS项目中,皇家NLR开发了一种特殊装置,该装置集成在科里奥利复合材料自动铺丝机(AFP)头的第八通道中,在碳纤维测试面板中嵌入四个阵列(单独的光纤线路),每个阵列有五到六个FBG传感器(PhotonFirst共提供23个传感器)。RVmagnetics已将其微丝传感器放入拉挤玻璃纤维增强塑料的纤维中。RVmagnetics联合创始人拉蒂斯拉夫·瓦尔加说:“这些线是不连续的(复合材料的大多数微丝长1-4厘米),但在生产增强件时会自动连续放置。你有一个1公里长的微丝线圈,并将其送入增强件生产设备,而不改变增强件的制造方式。”与此同时,Com&Sens正在研究在压力容器的纤维缠绕过程中嵌入光纤传感器的自动化技术。
碳纤维由于其导电能力,可能会导致介电传感器出现问题。电介质传感器使用彼此靠近放置的两个电极。“如果纤维桥接电极,它们将使传感器短路,”Lambient创始人李欢解释道。在这种情况下,使用过滤器。“过滤器让树脂通过传感器,但将其与碳纤维绝缘。”克兰菲尔德大学和NCC开发的线性介电传感器使用了一种不同的方法,包括两根绞合铜线。当施加电压时,电线之间会产生电磁场,用于测量树脂阻抗。电线涂有绝缘聚合物,不会影响电场的产生,但可以防止碳纤维短路。
当然,成本也是一个问题。Com&Sens引用了每个光纤光栅传感点的平均成本为50-125欧元,如果按体积应用,成本可能会降至约25-35欧元,例如10万个压力容器。麦科特的卡拉帕帕表示,他收到的带有FBG传感器的光纤线路的报价平均为250英镑/传感器(≈300欧元/传感器),询问器的报价约为10000英镑(12000欧元)。他补充道:“我们测试的线性介电传感器更像是一种现成的涂层线。”。“我们使用的询问器,”Cranfield大学复合材料工艺科学的读者(高级研究员)亚历克斯·斯科多斯补充道,“是一种阻抗分析仪,非常准确,成本至少为30000英镑(约36000欧元),但NCC使用的询问机要简单得多,基本上包括来自商业公司Advise Deta(英国贝德福德)的现成模块。”Synthesites对模内传感器报价1190欧元,一次性/零件式传感器报价20欧元,Optiflow报价3900欧元,Optimold报价7200欧元,多个分析仪单元的折扣不断增加。Pantelelis说,这些价格包括Optiview软件和任何必要的支持,并补充说,风力叶片制造商每个周期节省了1.5小时,每条生产线每月可以额外增加一个叶片,能耗降低20%,投资回报率仅为四个月。
新的可能性,前进的道路
随着复合材料4.0数字化制造的推进,使用传感器的公司将获得优势。例如,Com&Sens业务发展总监格雷瓜尔·博杜安表示:“随着压力容器制造商试图减轻重量、减少材料使用和降低成本,他们可以使用我们的传感器来证明他们的设计,并在2030年达到所需产量时监控生产。在纤维缠绕和固化过程中用于评估层内应变水平的传感器也可以在数千次加油循环中监测油箱的完整性,预测所需的维护,并在设计寿命结束时进行重新认证。我们可以为生产的每个复合压力容器提供一个数字孪生数据池,这个解决方案也在为卫星开发。”
启用数字孪生和线程
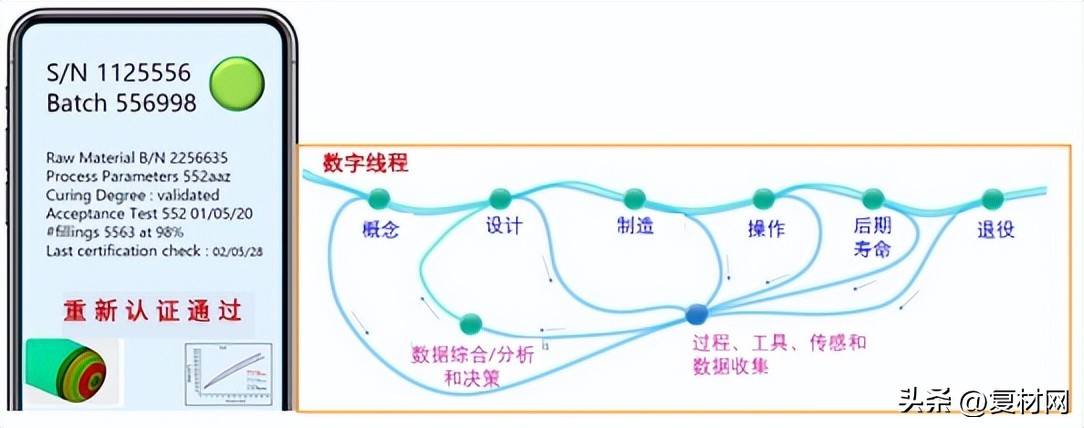
Com&Sens正在与复合材料制造商合作,使用其光纤传感器通过设计、生产和服务(右)实现数字数据流,以支持数字身份证(左),该身份证支持每个制造零件的数字孪生。
因此,传感器数据不仅可以实现数字孪生,还可以实现数字线程跨越设计、生产、在役操作和寿命终止。当使用人工智能和机器学习进行分析时,这些数据会反馈到设计和处理中,从而提高性能和可持续性。这也改变了供应链的合作方式。例如,粘合剂生产商Kiilto(芬兰坦佩雷)使用Collo传感器帮助客户控制其多组分粘合剂混合设备中组分A、B等的比例。“Kiilto现在可以为个人客户调整粘合剂的成分,” 卡拉帕帕斯说,“但它也让Kiilto看到树脂在客户的过程中是如何相互作用的,以及客户是如何与产品相互作用的。这正在改变供应链的协同工作方式。”

OPTO Light使用Kistler、Netzsch和Synthesites传感器,监测固化情况,实现热塑性包覆成型环氧碳纤维增强塑料零件。
传感器也使创新的新材料和工艺组合成为可能。在CW 2019年关于OPTO Light项目的文章中,AZL Aachen(德国亚琛)使用两步法水平压缩成型单向(UD)碳纤维/环氧预浸料,然后用30%的短玻璃纤维增强PA6包覆成型。关键是只部分固化预浸料,这样环氧树脂中的剩余反应性就可以与热塑性塑料结合。AZL使用Optimold和Netzsch DEA288 Epsilon分析仪、Synthesites和Netzsh介电传感器以及Kistler模内传感器和DataFlow软件来优化注塑成型。AZL研究工程师理查德·沙雷斯解释说:“你必须深入了解预浸料压缩成型过程,因为必须确保了解固化状态,才能与热塑性塑料包覆成型良好结合。”。“未来,该过程可能是自适应和智能的,由传感器信号触发过程旋转。”
然而,卡拉帕帕斯表示,存在一个根本问题,“即客户缺乏如何将这些不同传感器集成到其流程中的知识。大多数公司都没有传感器专家。”目前,前进的道路需要传感器制造商和客户之间来回交换信息。还有像AZL、DLR(德国奥格斯堡)和NCC这样的组织正在开发多传感器专业知识。Sause说,联合国协会内部有一些团体,也有一些衍生公司可以提供传感器集成和数字孪生服务。他补充道,奥格斯堡人工智能生产网络为此租用了一个7000平方米的设施,“将CosiMo的开发蓝图扩展到非常广泛的规模,包括连接在一起的自动化单元,行业合作伙伴可以在其中放置机器、运行项目并了解如何整合新的人工智能解决方案。”
卡拉帕帕斯说,美捷特和NCC的介电传感器演示只是第一步。“最终,我想监控我的流程和工作流程,并将其输入我们的ERP系统,这样我就可以提前知道要制造什么组件、需要什么人以及订购什么材料。我们现在已经开始向数字化自动化发展。”
原文,《Sensors: Data for next-gen composites manufacturing》2022.3.1
杨超凡 2025.7.18